What are the advantages of these flexible, thin, and often disposable circular products? How are they crucial in various applications?
These thin, circular, and frequently disposable items are a vital component in a range of industrial and medical procedures. They often consist of a flexible material like metal or plastic and are shaped as discs, used for specific tasks, and are not necessarily interchangeable with other products. Examples include specialized, disposable medical devices or specific industrial components.
These items' importance stems from their adaptability, disposability, and often, precise design. Their flexibility allows for targeted application, while their disposability minimizes the risk of contamination or cross-infection in medical settings. Specific design considerations lead to the precise implementation needed in industrial processes. Historical context points to the development of these items as solutions to specific challenges, highlighting their crucial role in specific technologies and methodologies, be it medical treatment or manufacturing applications. Their evolution showcases a continuing drive towards efficiency and safety in these applications.
- Epic Loser Strips Hilarious Fails Funny Fails
- Verizon Service In Kilmarnock Va Reliable Phone Internet
No specific individuals or celebrities are associated with the development or use of these products. The focus remains on the product itself and its functionality in various contexts.
Flex Disc
Understanding the essential elements of a flex disc reveals its critical role in diverse applications. This analysis explores key attributes and operational considerations of this product.
- Material
- Flexibility
- Shape
- Size
- Durability
- Application
- Disposability
- Precision
The listed aspects, such as material selection (metal or plastic) and flexibility, directly impact a flex disc's suitability for specific tasks. Shape, size, and durability determine its operational efficiency. The intended application dictates the appropriate material and design. Precision manufacturing ensures intended performance. Disposability impacts sanitation and safety protocols in specific sectors. Understanding these interrelated components is key to appreciating the crucial functionality of a flex disc in diverse sectors.
1. Material
Material selection is paramount in defining a flex disc's performance characteristics and suitability for its intended application. The inherent properties of the material directly influence the disc's flexibility, durability, and resistance to wear and tear.
- Impact on Flexibility and Shape Retention
The material's elasticity and plasticity determine the disc's ability to flex and maintain its intended shape under stress. A highly flexible material allows for greater adaptability, whereas a rigid material limits the disc's bending capabilities. This directly affects the disc's functionality in tasks requiring deformation or precision application. For example, a medical device needing to adapt to varying anatomical structures will necessitate a more flexible material than one for industrial applications, such as sealing components.
- Influence on Durability and Wear Resistance
Material strength and resilience affect the disc's resistance to wear and tear. A material's ability to withstand repeated stresses and potential abrasions is crucial to longevity. For instance, a disc used in an abrasive environment necessitates a material with high resistance to wear, potentially involving high-grade polymers or certain metals, depending on the specific application. This is directly linked to the disc's lifespan and operational efficiency.
- Effect on Chemical Resistance and Compatibility
In specific applications, the material must resist chemical reactions and remain compatible with the surrounding environment or working media. This is especially important in medical applications or industrial settings where the disc comes into contact with fluids or chemicals. Choosing appropriate materials minimizes contamination or degradation of the disc, enhancing performance and lifespan.
Ultimately, appropriate material selection ensures optimal performance of a flex disc in various application scenarios. Trade-offs between flexibility, durability, and chemical resistance determine the ideal material. This highlights the importance of careful consideration and the potential impacts of material selection on safety, performance, and overall effectiveness.
2. Flexibility
Flexibility is a defining characteristic of a flex disc. Its ability to deform without fracture is crucial to its function. This deformation allows for targeted application in diverse scenarios, from medical procedures to industrial processes. The degree of flexibility is directly correlated to the material composition and design. A highly flexible disc is better suited for complex, nuanced applications, where precise adjustments or conforming to irregular shapes are necessary. Conversely, a less flexible disc may be more robust, suitable for tasks that involve significant pressure or repetitive stress. Real-world examples include the use of flexible surgical instruments, where the flexibility of the disc permits access to hard-to-reach areas in the body, or in the manufacture of complex components where conformity to specific contours is essential.
The importance of flexibility extends beyond mere adaptability. The controlled deformation inherent in flexibility allows for precise application of force, often in delicate or confined spaces. This control is paramount in certain medical procedures, where a disc's ability to conform to tissue structures is essential. In manufacturing, flexibility plays a role in shaping materials or manipulating tools within tight tolerances. The significance of flexibility stems from the ability to optimize tasks, improve precision, and ensure safety through controlled movement and force distribution. Understanding the interplay between flexibility and the specific application is vital for ensuring optimal performance and avoiding unintended consequences.
In conclusion, flexibility is a key component of a flex disc's design and functionality. The relationship between flexibility and application dictates the suitable material and design. This crucial understanding ensures optimal performance, safety, and efficacy, from medical diagnostics to precision manufacturing. Challenges lie in achieving the desired level of flexibility while maintaining necessary structural integrity and longevity. Understanding and managing this crucial design element is fundamental to the successful application of flex discs in a variety of contexts.
3. Shape
The shape of a flex disc is intrinsically linked to its function and effectiveness. A disc's form dictates its interaction with target materials or environments. This interaction is critical in diverse applications. Circular or disc-like shapes offer a concentrated point of application, optimizing force distribution. Irregular or specialized shapes may be required for intricate tasks or for accommodating specific anatomical structures in medical applications. Precisely shaped discs can better conform to complex surfaces, ensuring a secure and effective hold. The shape allows for controlled movement and application of force. Deviation from the optimal shape compromises performance and potentially increases risk.
Real-world examples underscore the significance of shape. A medical device with a rounded edge might be better suited for delicate tissue handling, whereas a disc with sharp edges might be more appropriate for cutting or dissecting. In industrial contexts, a precisely contoured disc allows for the tight sealing or fastening of components. The intricate design of the shape allows for precise, localized interaction with the target material, thereby affecting the overall process efficacy. This precision is vital in industrial applications. In any application, a discs shape directly impacts its operational efficiency and safety. Understanding these aspects ensures optimal performance and minimizes risk factors.
In conclusion, the shape of a flex disc is not a mere aesthetic consideration; it is a critical design element. The interplay between the disc's form and its intended use strongly affects its performance and safety. A thorough understanding of the shape-function relationship allows for the selection of the most appropriate disc for each specific task, thereby optimizing performance and reducing potential hazards. This is crucial to ensuring that the disc reliably and efficiently achieves its intended function. The importance of shape extends beyond mere form to encompass essential functional aspects of the flex disc.
4. Size
The size of a flex disc is a critical determinant of its suitability for a given application. Precise size is vital, impacting both functional efficacy and safety protocols. Smaller discs, for instance, might be more maneuverable in confined spaces, but their reduced surface area limits the force they can exert. Larger discs, on the other hand, might offer greater strength and stability, but their size can restrict access or increase the risk of accidental damage during deployment. The selection of appropriate size is directly linked to the task requirements. A disc too large for the intended application could hinder the process, while one too small might be ineffective.
Real-world examples highlight the practical significance of understanding size-related considerations. In minimally invasive surgical procedures, the size of a flex disc dictates the extent of access and the precision of the intervention. A disc that is too large would impede visibility and potentially damage surrounding tissues. Similarly, in industrial applications requiring controlled force distribution, the disc size dictates the amount of pressure exerted and the potential for damage or malfunction. The proper sizing ensures the disc performs its intended role without compromise. Mismatched sizing can compromise outcomes, ranging from discomfort or pain in medical settings to machine malfunction or component damage in industrial procedures. A thorough understanding of the size-function relationship is essential for effective usage and safety.
In summary, the size of a flex disc is not a trivial aspect; it represents a fundamental design consideration. Appropriate sizing is inextricably linked to the functional success and safety of the application. Understanding the interplay between size and application allows for the selection of the optimal disc size, enhancing operational efficiency and mitigating risks. This principle holds across a range of applications, from surgical procedures to industrial manufacturing processes, underscoring the importance of size optimization.
5. Durability
Durability of a flex disc is paramount. Its ability to withstand repeated use and stresses directly impacts the device's lifespan and reliability in diverse applications. Understanding the factors affecting durability is crucial to ensuring safe and effective performance, from medical procedures to industrial processes. This analysis explores critical elements impacting the long-term viability of a flex disc.
- Material Composition and Properties
The inherent qualities of the material are fundamental to a flex disc's durability. Materials with high tensile strength, resistance to wear, and resilience to deformation are preferred. For instance, a disc intended for high-pressure environments necessitates a material with superior tensile strength, while one for repeated flexure demands materials with exceptional elasticity and fatigue resistance. The selection of appropriate materials is critical in maintaining structural integrity under diverse operating conditions.
- Manufacturing Techniques and Processes
Manufacturing methods play a substantial role in the disc's structural integrity. Rigorous quality control measures throughout the production process ensure a consistent level of durability. Defects in manufacturing, like flaws in the material or improper joining techniques, can compromise the disc's ability to withstand stresses, thereby directly affecting its lifetime. Precise manufacturing is paramount for a durable product.
- Design and Engineering Considerations
The design of a flex disc is intricately tied to its durability. Optimized stress distribution, robust joints, and carefully engineered geometries significantly impact the disc's resilience to external forces. Designing for redundancy and incorporating fail-safe mechanisms are often vital to prevent catastrophic failure. Careful attention to the structural design during the development phase significantly affects durability.
- Environmental Factors and Operating Conditions
Exposure to harsh environments, such as extreme temperatures, chemicals, or abrasive substances, can significantly degrade a flex disc's durability. Specific material choices, design modifications, and protective coatings become necessary to ensure the disc can withstand the specific operating environment. For instance, a disc intended for use in corrosive chemical processes will require different material properties or protective coatings than one intended for a controlled laboratory setting. Predicting and mitigating environmental impacts is crucial to the disc's longevity.
In conclusion, durability in a flex disc is a multifaceted aspect dependent on careful selection of materials, sophisticated manufacturing, thorough design evaluation, and meticulous consideration of operating conditions. A comprehensive understanding of these factors guarantees the long-term reliability of a flex disc across a spectrum of applications and ensures its consistent performance.
6. Application
The application of a flex disc is not merely incidental; it fundamentally shapes the disc's purpose and impact. The specific function for which a flex disc is designed directly influences its material composition, shape, size, and overall design. Without a clear application in mind, the effectiveness and suitability of the disc are compromised. Real-world examples illustrate this principle. A flex disc designed for delicate medical procedures requires a different material composition and shape compared to one intended for heavy-duty industrial tasks. This crucial link between application and design necessitates a thorough understanding of the specific use case before production.
The range of applications for flex discs is extensive. In medical settings, they may be components of surgical instruments or endoscopes, offering precise control and maneuverability. In industrial contexts, flex discs can facilitate intricate sealing tasks, enabling precise application of force and control within constrained spaces. Specific industrial processes like manufacturing or assembly frequently leverage flex discs to manipulate, shape, or apply pressure to materials. The application dictates the critical design features needed to ensure the disc performs its role efficiently. Mismatched application and design could compromise performance or introduce safety concerns. Proper application understanding leads to optimized use and safety protocols.
In conclusion, the application dictates the very nature of a flex disc. Understanding the specific intended usewhether medical, industrial, or anotheris critical for selecting appropriate materials, designing the correct shape and size, and ensuring the disc effectively fulfills its intended role. The importance of aligning application with design elements cannot be overstated. Failure to recognize this connection can lead to ineffective or unsafe implementations, highlighting the crucial link between the intended use and the design of a flex disc.
7. Disposability
Disposability, a key characteristic of many flex discs, significantly impacts their application. The ability to discard a flex disc after a single use or a limited number of uses is a critical factor influencing its design, function, and overall safety in various contexts. This feature often outweighs concerns of material costs and, in some instances, limits the applicability of reusable alternatives. The link between disposability and flex disc design is particularly pronounced in medical and industrial settings where concerns about contamination and sterility are paramount.
The practical significance of disposability is most evident in medical procedures. A disposable flex disc minimizes the risk of transmitting infections. This characteristic is essential for maintaining a sterile environment, especially during procedures involving sensitive tissues or high-risk areas. In industrial contexts, disposability reduces the risk of cross-contamination, ensuring the quality and reliability of the manufacturing process. For instance, a disposable flex disc used in a chemical reaction eliminates the need for extensive cleaning and sterilization between uses, saving time and preventing contamination. Further, in applications involving hazardous materials, disposability minimizes the risk of exposure and environmental impact.
In conclusion, the disposability of a flex disc is a critical design feature impacting its application in medical and industrial settings. This characteristic directly addresses concerns about contamination, sterility, and safety. While the initial cost of disposable flex discs might be higher than reusable options, the associated benefits in terms of safety and efficiency often outweigh this consideration. The understanding of the interconnectedness of disposability and application design is crucial for ensuring safe, reliable, and effective procedures across various sectors.
8. Precision
Precision in the design and manufacture of flex discs is not merely a desirable trait; it's a fundamental requirement for effectiveness and safety across various applications. Precise manufacturing ensures the disc accurately conforms to its intended shape and dimensions, directly influencing its functional performance. Variations in size, shape, or material properties can significantly impact the disc's ability to perform its intended task, from delicate surgical procedures to precise industrial applications.
The importance of precision is exemplified in medical contexts. A flex disc designed for minimally invasive surgery must exhibit extreme precision in its dimensions and flexibility to minimize tissue damage. Variations in thickness or curvature can potentially compromise the integrity of delicate tissue, leading to complications or negative health outcomes. Similarly, in industrial settings, precise tolerances in flex discs are crucial for sealing components or performing complex manipulations. Deviations from specified dimensions can impair sealing efficiency, leading to leaks, malfunctions, or potentially catastrophic consequences. In intricate assembly processes, a precisely manufactured flex disc ensures the smooth and accurate fitting of parts, resulting in reliable functionality. Examples include high-precision equipment like robotics and in tasks requiring tight tolerances, like electronic device fabrication.
In conclusion, precision is not merely a technical detail but a critical component in the design and manufacture of flex discs. Understanding the direct link between precision and effectiveness, safety, and the efficacy of the application is paramount. Challenges often arise in maintaining precision across large-scale production; sophisticated quality control measures are essential to ensure consistent quality and predictable performance. Failure to maintain high precision standards can lead to significant operational issues and safety concerns. Therefore, ensuring precision throughout the manufacturing process is an integral part of the flex disc's reliability and dependability, underpinning its successful application across diverse industries.
Frequently Asked Questions about Flex Discs
This section addresses common questions and concerns regarding flex discs, providing clear and concise answers based on established knowledge and application practices.
Question 1: What materials are typically used in the manufacture of flex discs?
Flex discs utilize a range of materials, primarily chosen for their specific properties. Common materials include metals like stainless steel and specific alloys for their strength and durability. In applications requiring greater flexibility, polymers and composite materials are employed, offering flexibility and a wider range of mechanical properties. The selection of materials is always application-specific.
Question 2: How does the size of a flex disc impact its function?
Disc size significantly affects performance. Smaller discs are often more maneuverable in confined spaces but might exert less force. Larger discs, conversely, provide greater strength and stability but can be less adaptable to tight areas. The optimal size depends on the specific application's requirements.
Question 3: What are the benefits of using disposable flex discs?
Disposable flex discs minimize the risk of cross-contamination, particularly in medical settings. This single-use characteristic ensures sterility, preventing the spread of pathogens and maintaining a controlled environment. Disposables also streamline cleanup procedures. However, environmental considerations are sometimes pertinent.
Question 4: How does the shape of a flex disc influence its effectiveness?
The shape of a flex disc directly impacts its application. A circular shape often concentrates force, while specialized shapes enable targeted application. A disc's form must align with its intended function to optimize results, ensuring successful performance in various scenarios.
Question 5: What are the factors determining the durability of a flex disc?
Factors like material selection, manufacturing techniques, design specifications, and environmental conditions all play critical roles in a flex disc's durability. A material with superior tensile strength and resilience, robust manufacturing techniques, well-engineered design, and specific protective coatings, minimize the degradation of the disc under operational stress. Environmental considerations are critical.
Understanding the diverse factors influencing flex disc function and application is vital for selecting and implementing them effectively across a range of sectors. Careful consideration of these factors contributes to improved performance, safety, and cost-effectiveness.
This concludes the FAQ section. The following section will delve into specific manufacturing processes.
Conclusion
This analysis explored the multifaceted nature of flex discs, highlighting their crucial role in diverse applications. Key aspects, including material selection, flexibility, shape, size, durability, application, disposability, and precision, were examined. The importance of aligning these attributes with the specific functional requirements was underscored. Each element plays a vital part in the overall success and safety of using these devices. The analysis demonstrates the intricate interplay between design characteristics and operational efficacy in various sectors. Careful consideration of these factors is essential for optimal performance and risk mitigation.
The application of flex discs spans a wide spectrum, from intricate medical procedures to specialized industrial processes. The continued evolution of materials and manufacturing techniques ensures flex discs remain relevant and vital. Future advancements in design and material science will likely further enhance their capabilities and applications in challenging environments. Ultimately, a comprehensive understanding of the principles governing flex disc design and function is vital for continued innovation and safe implementation in existing and emerging sectors.
/flex-df461d3966d54eae907fa9fd76dbdb8b.jpg)

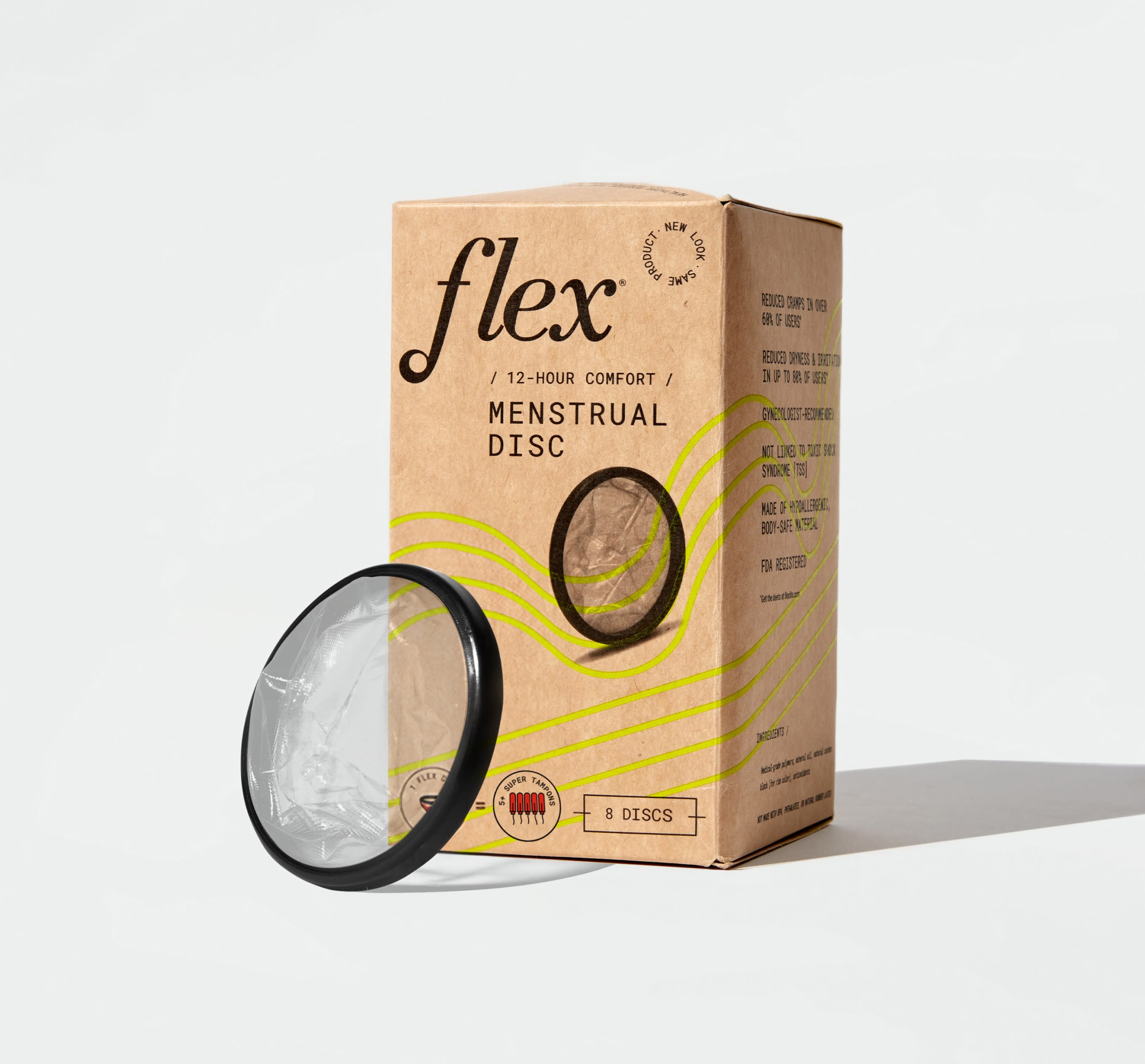
Detail Author:
- Name : Prof. Athena Blick
- Username : alphonso34
- Email : lorn@spencer.com
- Birthdate : 2000-10-02
- Address : 2775 Nader Fall Suite 184 East Kassandra, HI 38263-2850
- Phone : 352-394-4952
- Company : Hintz-Koelpin
- Job : Adjustment Clerk
- Bio : Rerum rerum alias quia optio. Sit et sint unde qui earum. Quisquam magnam officiis ducimus eaque.
Socials
twitter:
- url : https://twitter.com/nicolasg
- username : nicolasg
- bio : Et ut eveniet dolores. Accusamus delectus cum iste reprehenderit. Odio doloribus fuga nobis.
- followers : 5815
- following : 468
facebook:
- url : https://facebook.com/golden_nicolas
- username : golden_nicolas
- bio : Quis laudantium consequuntur dignissimos quia at iure quidem suscipit.
- followers : 4811
- following : 1505