What is the Significance of This Specialized System? A Novel Approach to Precise Automation.
This system, a specialized form of automated control, prioritizes accuracy and precision in complex mechanical or digital processes. It facilitates highly intricate sequences of actions, often with tight tolerances. Consider a robotic arm precisely positioning micro-components or a manufacturing process requiring highly predictable outputs. The system's function hinges on a detailed understanding of all relevant variables, enabling the attainment of desired results with minimal error margins.
The advantages of this approach are substantial. Reliability and consistency are key benefits, enabling high production standards. Efficiency is also enhanced, reducing time and resource consumption associated with manual or less precise methods. Reduced error rates mean minimizing waste, rework, and potential failures. Over time, such control systems can lead to considerable cost savings. The historical context involves the evolution of automation, with this system marking a significant advancement toward enhanced precision. Continuous improvements and integration with evolving technologies will likely enhance its applications and benefits.
The exploration of this approach to automated systems opens numerous avenues for investigation. From optimization strategies to potential integration with artificial intelligence, a wide range of further developments is anticipated. The focus will be on broader applications in manufacturing, research, and beyond.
tolomatic
Understanding the core components of tolomatic systems is crucial for effective implementation and optimization. The following key aspects provide a framework for comprehension.
- Precision control
- Automated processes
- Variable management
- Minimized error
- Enhanced efficiency
- System integration
These aspects highlight the multifaceted nature of tolomatic systems. Precision control, the cornerstone of the system, requires meticulous management of variables to achieve minimal error. Automated processes enhance efficiency by automating tasks, streamlining operations and reducing reliance on human intervention. Efficient system integration ensures seamless interaction with other components, further optimizing overall performance. Examples include robotic assembly lines maintaining exacting tolerances or sophisticated control systems in aerospace applications. These elements combined represent a critical advancement in achieving optimal performance within automated systems.
1. Precision control
Precision control forms the bedrock of tolomatic systems. Its importance lies in the ability to achieve highly accurate and repeatable results in automated processes. Without exacting standards of precision, the benefits of automation are diminished, and potential errors can lead to costly rework or failures. This facet examines the crucial role of precise control in achieving optimal performance within tolomatic systems.
- Variable Management
Accurate control demands a thorough understanding and management of all relevant variables. Factors such as temperature, pressure, and material properties must be tightly controlled to maintain consistent results. This includes methods for monitoring and adjusting these variables in real-time to ensure the desired outcome. Examples include automated systems in microelectronics manufacturing, where precise control over temperature prevents material damage, or in 3D printing, where precise layer deposition ensures dimensional accuracy. Effective variable management is critical to the reliability of tolomatic systems.
- Sensor Integration and Feedback Loops
Effective precision control hinges on real-time data acquisition and analysis. Advanced sensors provide constant feedback on process parameters, enabling the system to adjust and maintain precise control. Sophisticated feedback loops translate sensor readings into immediate adjustments in system operations. This allows for continuous optimization, preventing deviation from the desired output. For instance, CNC machining utilizes sensors to monitor cutting parameters and adjust the machine's actions to maintain precise tolerances. Accurate feedback loops improve overall efficiency and quality in tolomatic systems.
- Tolerance Determination and Adjustment
Defining and maintaining precise tolerances is paramount in tolomatic systems. Setting allowable deviations from target values is crucial for acceptable output. Systems must be designed with the ability to continuously adjust to maintain these tolerances, adapting to variations or unexpected circumstances. This adaptation ensures consistent quality across production runs. A robotic assembly line, for example, must adjust its movements to account for slight variations in component size to maintain assembly precision and efficiency.
- Redundancy and Fail-Safes
Critical to ensuring precise control in a tolomatic system is the implementation of redundancy and fail-safe mechanisms. This ensures that should a sensor fail or a component malfunction, the system can maintain control and prevent significant errors. Redundant systems allow continuous monitoring and operation even during component or system failures. In aerospace manufacturing, redundancy is crucial for maintaining precise control during flight operations.
In summary, precision control is not merely a component but the foundational principle of tolomatic systems. Effective variable management, sensor integration, tolerance determination, and redundancy are essential for achieving and maintaining precise control, thus contributing significantly to the overall reliability and effectiveness of automated processes.
2. Automated Processes
Automated processes are integral to tolomatic systems. These systems demand precision and consistency, making automation a critical component. The seamless integration of automated processes with precise control mechanisms is what distinguishes tolomatic systems from other forms of automation. This section examines key facets of automated processes within the framework of tolomatic systems.
- Sequential Task Execution
Tolomatic systems rely on meticulously defined sequences of actions. These automated sequences are critical in maintaining the desired precision and consistency. A specific order of operations ensures that each step contributes to the overall goal, minimizing errors and maximizing efficiency. Examples include robotic assembly lines where components are precisely positioned in a predetermined order, or in 3D printing, where layer-by-layer deposition is carefully controlled. Maintaining this sequential execution is paramount to maintaining accuracy and efficiency within tolomatic operations.
- Real-time Monitoring and Control
Automated processes in tolomatic systems are not passive. Continuous monitoring of process parameters is crucial. Real-time adjustments to variables are necessary, as the system adapts to dynamic conditions or variations in input. Sensors provide data on critical parameters, enabling the system to make immediate corrections. This dynamic feedback loop is essential for maintaining precision and avoiding errors, especially in complex manufacturing environments. Examples include adaptive control systems in CNC machining, where real-time monitoring and adjustment of cutting parameters ensures precise tolerances. Automated control systems in industrial processes ensure minimal waste and maximal productivity.
- Process Optimization through Automation
Automation within tolomatic systems goes beyond simple task execution. It allows for continuous optimization through data analysis and process improvements. Automated data collection and analysis can highlight areas for process enhancement or identify deviations that may affect precision or efficiency. Machine learning algorithms can further refine processes over time, improving overall performance. This continuous optimization aligns with the goal of maintaining precision and efficiency in tolomatic operations.
- Integration with Other Systems
Tolomatic systems are typically interconnected with other systems and processes. The integration between automated processes and other elementssuch as data management systems or quality controlis necessary for the comprehensive functioning of the entire operation. The integration enables a unified and coordinated system where each component contributes to the overall performance and precision of the tolomatic system. This interconnectivity ensures the consistent performance of the entire system.
In conclusion, automated processes are not merely a component of tolomatic systems; they are fundamental to its operation. The meticulous sequence, real-time adjustments, and continuous optimization through automation within the framework of tolomatic systems, are crucial to maintaining precision and efficiency in complex operations, ultimately contributing to the system's reliability and superior performance.
3. Variable Management
Effective variable management is fundamental to the operation of tolomatic systems. Precise control over variables is the cornerstone of achieving consistent and reliable outcomes within automated processes. The ability to monitor and adjust variables in real-time is crucial for maintaining tolerances and preventing deviations from desired performance parameters. Inconsistent variables directly correlate to inaccuracies and decreased efficiency within a tolomatic system.
Consider a robotic assembly line tasked with precise component placement. Variations in component size, material properties, or environmental factors (temperature, humidity) can significantly impact the accuracy of the assembly process. Without mechanisms for continuous monitoring and adjustment of these variables, the system risks accumulating errors, leading to defective products and reduced output. Variable management in this context involves intricate sensors to track component dimensions and environmental conditions, followed by real-time adjustments to the robotic arm's movements, ensuring alignment and minimizing errors. This highlights the direct causal relationship between precise variable management and achieving desired accuracy within tolomatic systems.
Understanding the interplay between variable management and tolomatic systems has significant practical implications. Accurate predictions and adjustments based on monitored variables can lead to substantial cost savings by minimizing waste, rework, and potential failures. In advanced manufacturing or scientific research, maintaining controlled variables is essential for producing high-quality products and replicable results. Moreover, successful implementation of variable management within tolomatic systems can lead to process optimization, which further enhances efficiency and output. By recognizing the crucial role of variable management, organizations can enhance the reliability and performance of their automated systems, ultimately boosting profitability and productivity.
4. Minimized Error
Minimizing error is a defining characteristic of tolomatic systems. This principle emphasizes the importance of precise control and consistent outcomes within automated processes. The reduced possibility of errors inherent in these systems directly translates into improved efficiency, reduced waste, and increased reliability, making it a critical component in various applications, from manufacturing to scientific research.
- Precise Control Mechanisms
The foundation of minimizing error in tolomatic systems lies in meticulous control mechanisms. Sophisticated sensors and feedback loops are integral components, enabling real-time adjustments to counteract any deviations from the desired parameters. These adjustments contribute to maintaining precise tolerances and consistency in the process output. For example, highly accurate positioning systems in robotic surgery or in the manufacturing of microchips rely on this principle of precise control, ensuring the minimal deviation from planned trajectories or specifications.
- Redundancy and Fail-Safes
Implementing redundancy and fail-safe mechanisms is crucial to mitigating errors in complex automated systems. Redundant systems provide backup capabilities in case of component failures or unexpected disruptions. By employing redundant sensors, actuators, or control processes, the system can continue functioning without catastrophic failures, ensuring continuous operation and minimizing the risk of significant errors. This is essential in sectors like aerospace engineering, where the reliability and precision of automated systems are paramount for safety and operational efficiency.
- Data Analysis and Optimization
Continuous monitoring and analysis of operational data are essential for identifying patterns that might indicate potential errors or deviations from optimal performance. Tolomatic systems often incorporate data analysis techniques to understand and predict potential issues, enabling proactive adjustments to maintain the desired level of precision and accuracy. Analysis of data from various sensors allows for optimization and refinement of procedures, leading to a marked decrease in error rates over time. This is exemplified in automated manufacturing processes where identifying patterns in defects leads to modifications in the production line to enhance consistency and reduce defects.
- Robust Design and Calibration
A robust design incorporates features that anticipate and mitigate potential errors. Regular calibration and maintenance procedures are essential to ensure consistent performance and reduce deviations over extended periods. This approach involves meticulous attention to detail in the design phase and systematic maintenance protocols to sustain the desired level of accuracy. For instance, in high-precision machine tools, regular calibration and maintenance procedures are crucial for minimizing deviations in cutting or machining tolerances and ensuring the consistent quality of the output.
Minimized error, a central theme within tolomatic systems, significantly contributes to reliability, efficiency, and cost-effectiveness. The combination of precise control mechanisms, redundancy, data-driven optimization, and robust design principles leads to a system that not only performs with precision but also learns and adapts to minimize deviations from the expected outcomes. This approach minimizes waste, improves production rates, and allows for repeatable and accurate results in a wide range of industrial and scientific applications.
5. Enhanced Efficiency
Enhanced efficiency is a crucial outcome directly linked to tolomatic systems. The precise control and automation inherent in tolomatic methodologies significantly reduce operational time, minimize waste, and improve overall productivity. This enhanced efficiency translates into substantial cost savings and increased profitability for organizations utilizing these systems.
- Reduced Cycle Times
Tolomatic systems automate tasks, eliminating the need for manual intervention at critical stages. This streamlining of processes directly reduces cycle times, accelerating production and enabling faster output. Automated assembly lines, for instance, dramatically shorten the time required to assemble products, leading to increased throughput and higher output levels compared to manual counterparts. This accelerated output is a direct result of the automation and precise control mechanisms within tolomatic systems.
- Minimized Waste and Defects
Precise control and consistent operation in tolomatic systems minimize errors and defects. Reduced errors, in turn, translate directly into less waste and rework. Automated quality control systems, integrated with tolomatic components, proactively identify and address deviations from the desired parameters. Consequently, fewer defective products require rectification, directly reducing waste and improving the overall efficiency of the production process.
- Optimal Resource Utilization
Tolomatic systems often optimize resource allocation, maximizing the utilization of materials, energy, and labor. This optimization is achieved through precise control over resource dispensing, preventing over-allocation or under-utilization. Automated systems can, for example, adjust machinery operations based on material availability or production demands, improving the efficiency of resource use. This ensures that resources are employed effectively, reducing idle time and maximizing output.
- Improved Scalability
Tolomatic systems often lend themselves to scalability. Their modular design and automated nature allow for easier expansion to accommodate increased production demands. Expanding a tolomatic system often involves adding additional modules or units without requiring significant restructuring of the overall process. This adaptability to increasing output requirements ensures that systems can adjust to changing market demands without a proportionate increase in operational complexity or downtime.
These factors, taken together, highlight the significant contribution of tolomatic systems to enhanced efficiency. The precise control and automated nature of these systems lead to reduced cycle times, minimized waste, optimized resource allocation, and improved scalability. Consequently, organizations implementing tolomatic systems can expect improved productivity, reduced costs, and a significant enhancement in overall operational efficiency.
6. System Integration
System integration is a critical component of tolomatic systems, enabling seamless interaction between various interconnected components. The effectiveness of a tolomatic system hinges on the ability of these disparate parts to communicate and function harmoniously. Proper integration ensures that data flows smoothly and controls operate cohesively, leading to optimized performance and reduced error.
- Data Flow and Communication Protocols
Effective system integration requires well-defined protocols for data transmission and communication between different components. These protocols ensure that information, such as sensor readings, control signals, and process parameters, is transferred reliably and accurately. A robust data-flow architecture is essential for tolomatic systems to function effectively. This includes standardized interfaces and communication protocols that enable components to interact smoothly, regardless of their specific functionalities. Examples include industrial Ethernet protocols, fieldbus systems, and specialized communication networks.
- Hardware Compatibility and Interoperability
Integration demands compatibility among various hardware components. This ensures that different equipment operates seamlessly together. Tolomatic systems often incorporate diverse equipment, from sensors and actuators to controllers and processing units. Interoperability and hardware compatibility guarantee efficient data exchange and seamless control. For instance, a robotic arm's controller must communicate with sensors to measure object position, and the controller's instructions must translate into precise movements. Compatibility across the hardware spectrum, including power management systems, is vital.
- Software Integration and Control Systems
Integration extends to software components that control and coordinate the system's operation. Software platforms and control systems manage data processing, task scheduling, and feedback loops. The successful integration of various software components, such as programming languages and data management systems, ensures consistent and reliable operation of tolomatic systems. Sophisticated algorithms might manage complex processes across integrated systems, maintaining precise control in robotic surgeries or advanced manufacturing.
- Security and Redundancy in Integrated Systems
Security and redundancy are paramount within integrated systems. This involves implementing safeguards to protect sensitive data and ensure continuous operation. System failures can have significant consequences in critical applications. Robust security protocols, including encryption and access controls, must be incorporated into integrated systems to prevent unauthorized access or malicious interference. Redundancy, through duplicate components or backup systems, mitigates disruptions, ensuring uninterrupted operation even in the event of component failure.
In conclusion, effective system integration is essential for the successful operation of tolomatic systems. The seamless interaction between various components, through standardized protocols, compatible hardware, integrated software, and robust security measures, is vital for achieving high-precision performance, reliability, and optimal efficiency in complex automated processes. This collaborative approach is critical for achieving the precise results expected from tolomatic methodologies.
Frequently Asked Questions about Tolomatic Systems
This section addresses common inquiries regarding tolomatic systems, offering clear and concise answers to promote understanding and effective application of these advanced methodologies.
Question 1: What distinguishes tolomatic systems from other automation technologies?
Tolomatic systems prioritize exceptionally high precision and accuracy. While other automation technologies focus on task execution, tolomatic systems emphasize meticulous control of variables, minimizing errors, and ensuring repeatable outcomes. This superior precision arises from advanced sensor integration, real-time feedback loops, and a rigorous focus on minimizing variations throughout the process. Tolomatic systems deliver results with a level of accuracy that transcends standard automation, making them ideal for applications requiring consistent, high-quality output, such as in microelectronics, aerospace, and precision manufacturing.
Question 2: What are the key components of a tolomatic system?
Tolomatic systems comprise interconnected components designed for precise control. Essential elements include sophisticated sensors for real-time data acquisition, robust actuators for precise execution, and intelligent control algorithms to manage variables and maintain tolerances. A critical element involves seamless data communication protocols between these diverse components. The integration of these components results in a system capable of adapting to dynamic conditions and consistently delivering desired outcomes.
Question 3: What are the potential applications of tolomatic systems?
Tolomatic systems find application across various sectors requiring precision and accuracy. Microelectronics manufacturing benefits from tightly controlled processes. Aerospace applications demand precise movement and positioning for component assembly and assembly. Precision machining, medical technology (such as robotic surgery), and other sectors requiring high accuracy are well-suited to tolomatic system implementation.
Question 4: What are the advantages of employing tolomatic systems?
Tolomatic systems offer numerous advantages. Reduced error rates translate to decreased waste and rework, saving resources and minimizing costs. Enhanced precision leads to higher quality outputs, consistent production, and improved efficiency in completing tasks. The automation inherent in these systems enables increased productivity and greater output levels compared to manual approaches. These features position tolomatic systems as valuable tools for optimizing processes in a range of industries.
Question 5: How can organizations determine if tolomatic systems are a suitable solution?
Organizations contemplating the implementation of tolomatic systems should consider the requirements of their specific applications. Factors such as production volume, tolerance specifications, environmental variables, and anticipated output quality should be assessed. Consultations with experts in tolomatic systems can provide crucial insights into the feasibility and effectiveness of such implementations, which ultimately allows organizations to make informed decisions regarding the integration of tolomatic systems into their existing processes.
Understanding the intricacies of tolomatic systems requires a careful evaluation of the application's specific needs and the capabilities of the proposed implementation. These systems offer considerable potential for enhancing process efficiency, quality, and profitability within sectors requiring optimal precision.
The subsequent section will delve deeper into the specific implementation strategies and integration considerations for tolomatic systems.
Conclusion
This exploration of tolomatic systems has highlighted their crucial role in modern manufacturing and specialized applications. The core principles of precise control, automated processes, variable management, and minimized error are paramount to achieving exceptional results. The ability of these systems to optimize resource utilization, reduce defects, and enhance overall operational efficiency underscores their significant impact. System integration and consistent communication protocols facilitate the smooth operation of interconnected components, contributing to the reliable performance of intricate processes. The benefits extend from higher output and reduced costs to consistent product quality and the capacity to adapt to evolving technological landscapes.
The evolution of tolomatic systems is an ongoing journey. Further research and development in areas such as advanced sensor technology, intelligent control algorithms, and seamless integration with other automation platforms will likely push the boundaries of what is achievable. The integration of emerging technologies, including artificial intelligence and machine learning, promises even greater precision and adaptability, opening avenues for improved efficiency and the creation of innovative solutions across numerous sectors. Organizations seeking to enhance their production processes, achieve higher quality standards, and navigate the dynamic landscape of modern manufacturing will likely find tolomatic systems an invaluable investment.
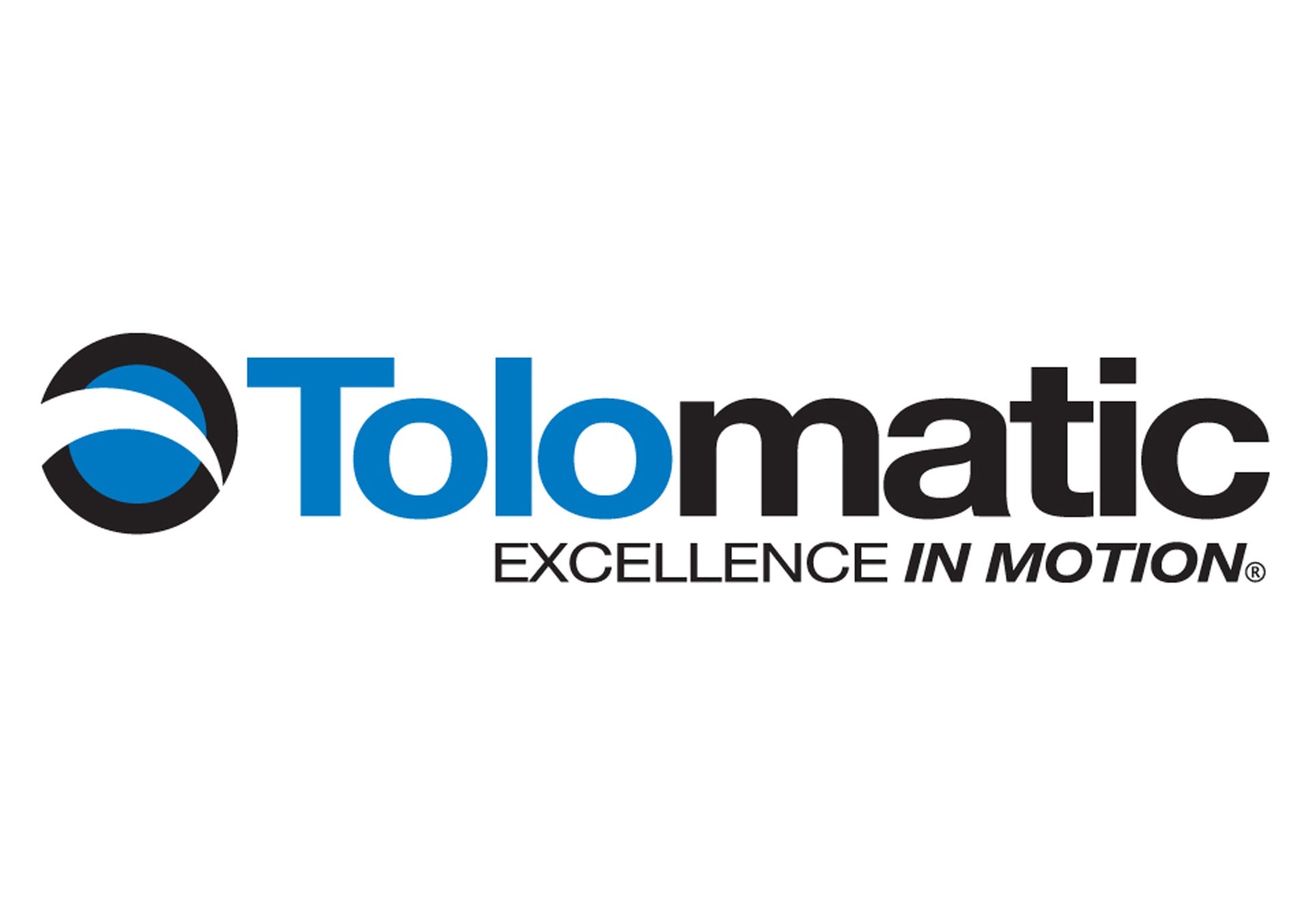


Detail Author:
- Name : Thad Mante
- Username : koss.lilly
- Email : kayli.okon@powlowski.com
- Birthdate : 1987-07-28
- Address : 828 Talia Stream Suite 466 Dickinsonberg, HI 48947-2585
- Phone : 952-734-7849
- Company : Bradtke, Konopelski and Champlin
- Job : Custom Tailor
- Bio : Vel nobis unde consequatur vero amet. Quas reprehenderit sunt possimus. Tempore omnis est hic vel reiciendis non veritatis quia. Cupiditate labore in et delectus sapiente facere.
Socials
twitter:
- url : https://twitter.com/julie1053
- username : julie1053
- bio : Nostrum sit laborum recusandae ullam. Iusto quia nemo ut nesciunt. Officia sunt neque qui cumque sapiente dolores.
- followers : 5838
- following : 893
instagram:
- url : https://instagram.com/julie_schimmel
- username : julie_schimmel
- bio : Ipsa voluptatem earum asperiores magnam dolor illum. Alias eius ut quos et molestiae vero cumque.
- followers : 4948
- following : 1009