What is the significance of this specialized material, and how does it impact various industries?
This material, a synthetic polymer composite, exhibits unique characteristics regarding its strength, durability, and resistance to various environmental factors. Formulations can be tailored to specific applications, resulting in a material optimized for performance. Examples include components in aerospace, automotive, and construction sectors, where lightweight yet robust materials are highly valued.
The material's importance stems from its ability to offer a balance of properties. High-strength-to-weight ratios, coupled with resistance to corrosion and degradation, make it a valuable substitute for heavier, less resilient materials in numerous applications. Historical context points to the ongoing search for enhanced materials, and this material represents a recent advancement in meeting these demands, particularly in the context of sustainability by potentially reducing material use and waste. Moreover, its customized formulability allows tailoring to precise application requirements.
Now, let's delve into the specifics of the design and manufacturing processes involved, examining how specific properties are achieved and the challenges in scaling this material for diverse industrial applications.
Plastorex
Understanding Plastorex requires examining its key attributes, emphasizing the material's composition, properties, and applications. Each aspect contributes to the overall understanding of this advanced material.
- Polymer composite
- Customized formula
- High strength
- Light weight
- Environmental resistance
- Aerospace use
- Sustainable solutions
These key aspects showcase Plastorex's multifaceted nature. A polymer composite allows for tailored formulas, resulting in high strength and lightweight properties crucial for aerospace applications. Resistance to environmental factors contributes to durability, while the material's design and production can contribute to sustainable practices. Ultimately, Plastorex demonstrates the potential for optimized materials to meet specific demands across diverse sectors, from aerospace to general construction.
1. Polymer composite
Polymer composites are crucial to understanding Plastorex. They represent a class of materials derived from combining polymers with other materials, often reinforcements like fibers. This composite nature dictates the specific properties and applications of Plastorex, and their interrelationship demands exploration.
- Component Materials and Their Roles
The specific polymers and reinforcing materials in a polymer composite directly influence the final product's characteristics. For instance, the selection of a particular polymer can dictate properties like flexibility, stiffness, or resistance to chemicals. Reinforcing materials, such as fibers or particles, provide strength and durability, while the matrix polymer holds these components together. The careful selection and proportioning of these components are key to tailoring the composite's performance.
- Properties of the Composite
The combined properties of the constituent materials define the composite's overall characteristics. This includes strength, stiffness, toughness, and resistance to various environmental factors. A well-designed composite can exhibit superior properties compared to its individual components, leading to enhanced performance in diverse applications. This optimized performance is a critical aspect of Plastorex.
- Manufacturing Processes
The manufacturing methods for polymer composites influence the final material's properties. Techniques like molding, pultrusion, and filament winding determine the uniformity and quality of the composite structure. These methods, crucial for reproducibility in the production of Plastorex, need to be precisely controlled to ensure desired performance and quality.
- Application Examples and Industries
Polymer composites have broad industrial applications, frequently replacing traditional materials due to their enhanced properties. Examples include aerospace components, automotive parts, construction materials, and sporting goods. The specific composite formulations tailored for Plastorex are directly linked to their specialized requirements within these sectors. This customization reflects the fundamental understanding of how different components contribute to different end-use products.
In summary, polymer composites are foundational to the understanding of Plastorex. The precise composition and manufacturing processes determine the final properties, leading to optimized performance in demanding applications. The specialized nature of Plastorex highlights the potential of engineered polymer composites to satisfy specific needs in the modern industrial landscape.
2. Customized Formula
The concept of a "customized formula" is fundamental to the characterization of Plastorex. A customized formula dictates the precise composition of the material, enabling tailoring to specific performance requirements. This customization is not a superficial aspect but rather the core of Plastorex's value proposition. It allows for optimization in various applications, directly impacting factors like strength, durability, and resistance to environmental stressors.
This tailored approach contrasts with generic materials, which often compromise performance across diverse applications. For instance, a customized formula for an aerospace component might prioritize high-strength-to-weight ratios, while a customized formula for a structural component in construction might emphasize impact resistance and weathering resistance. The ability to adjust the composite's properties according to the specific needs of the application is crucial. This approach ensures optimal performance and reduces material waste, aligning with sustainability goals. Real-world examples in industries using polymer composites like automotive and construction demonstrate the direct and substantial benefits of optimized formulas.
In essence, the "customized formula" aspect of Plastorex underscores the material's adaptability and performance-driven design. Understanding this crucial component reveals the meticulous engineering behind the material's development and highlights the strategic advantages gained through tailored composition. Challenges in achieving complex customized formulas relate to the precise control of material proportions and the optimization of manufacturing processes. Success in these areas is critical to maximizing the practical application of the material.
3. High Strength
High strength is a defining characteristic of Plastorex, directly impacting its suitability for a range of applications. The material's ability to withstand substantial forces and stresses is a key factor in its performance and end-use applications. This characteristic, when considered alongside other properties, determines the material's efficacy in various scenarios.
- Tensile Strength and its Significance
Tensile strength, a crucial aspect of high strength, measures the material's resistance to being pulled apart. High tensile strength in Plastorex allows for the creation of components capable of bearing significant loads without deformation or failure. This is essential in industries like aerospace, where lightweight, yet robust components are paramount. Examples include structural elements within aircraft and spacecraft, where safety and reliability are paramount.
- Compressive Strength and Structural Integrity
Compressive strength, the material's resistance to crushing or collapsing under pressure, is equally critical. High compressive strength enables the design of robust structures capable of enduring substantial pressure. This property is vital for components subjected to compressive forces, such as load-bearing elements in bridges and buildings. Plastorex's high compressive strength is a key consideration in these applications.
- Impact Resistance and Durability
Impact resistance, the ability to withstand sudden, forceful impacts, is directly related to high strength. This property is vital for applications where components are prone to collision or shock, such as safety components in vehicles. A high degree of impact resistance ensures longevity and reliable performance under challenging conditions, a critical attribute of Plastorex in these applications.
- Manufacturing Considerations and Design Parameters
The high strength of Plastorex influences the design parameters and manufacturing processes. Engineers must account for the material's ability to support load-bearing characteristics. Careful consideration must be given to stress concentrations, reinforcement strategies, and fabrication methods to fully leverage the material's strength characteristics within specific designs and manufacturing processes.
In summary, the high strength of Plastorex is a multifaceted attribute that allows for the design of components and structures that are both durable and efficient. This translates to a wide range of practical applications, particularly where lightweight, high-strength materials are required. Considering the combined effect of tensile, compressive, and impact resistance, along with the associated manufacturing parameters, is essential in harnessing the full potential of Plastorex's high-strength properties.
4. Light Weight
The attribute of "light weight" is intrinsically linked to Plastorex's suitability for specific applications. Minimizing weight while maintaining structural integrity is a critical design consideration in numerous industries. This characteristic is particularly relevant for Plastorex in applications where reduced mass directly translates to enhanced performance, fuel efficiency, and cost savings.
- Reduced Mass and Enhanced Performance
A lighter material allows for increased payload capacity or greater speed in applications like aerospace. Reduced weight in components leads to a corresponding decrease in the overall system's mass, which is often crucial for maximizing efficiency and performance in air and space travel. This characteristic is highly relevant to Plastorex's applications in aerospace, allowing for improved aircraft performance.
- Fuel Efficiency and Cost Savings
Lighter components directly translate to decreased fuel consumption in transportation applications. In industries like automotive and marine transportation, lower weight leads to more efficient use of fuel resources, lowering operational costs and reducing environmental impact. For Plastorex, this aspect is significant in its applicability within these sectors.
- Improved Handling and Maneuverability
Reduced weight facilitates improved handling and maneuverability in various applications. In sectors like robotics, drones, and specialized equipment, reduced mass enables greater agility and precision. This translates to enhanced controllability, which is a crucial advantage of Plastorex in applications requiring responsive and agile performance.
- Structural Integrity and Design Considerations
While lightweight design prioritizes minimizing mass, structural integrity must remain paramount. Plastorex's unique formulations need to be engineered to balance light weight with necessary strength and durability for specific applications. Careful design considerations are crucial to ensure the material can withstand stresses and loads without compromising its lightweight characteristics.
The "light weight" property of Plastorex is a significant factor influencing its applications. By optimizing the material's density and strength, industries can realize improvements in performance and efficiency. The successful integration of this characteristic necessitates careful design, material selection, and manufacturing processes, ensuring the balance between reduced mass and maintained structural integrity. The implications of Plastorex's light weight for various industries are substantial.
5. Environmental Resistance
Environmental resistance is a critical component of Plastorex's value proposition. The material's ability to withstand various environmental factorsincluding extreme temperatures, moisture, chemicals, and UV radiationis paramount to its longevity and suitability for diverse applications. This resilience directly impacts the material's performance and lifespan in demanding environments.
Factors influencing environmental resistance include the specific polymer matrix and reinforcing elements in the composite. Careful selection and precise ratios of these components directly influence the material's ability to resist degradation. For instance, a composite designed for outdoor construction applications would prioritize resistance to UV degradation, moisture absorption, and temperature fluctuations. In contrast, a composite for aerospace applications might emphasize resistance to extreme temperatures and corrosive elements found in the atmosphere at high altitudes. Real-world examples include bridges and other infrastructure projects, where the material's sustained performance under various weather conditions is crucial. The ability of Plastorex to maintain its properties across a wide spectrum of environmental challenges is crucial for its successful integration into diverse sectors.
Understanding the interplay between environmental resistance and material composition is essential for optimized application design. This understanding allows engineers to predict and mitigate potential performance issues that arise from environmental factors. Selecting the appropriate Plastorex formulation for a given application ensures sustained performance and reliability over the material's expected lifespan. Challenges may arise with specific combinations of environmental factors, such as extreme temperature fluctuations coupled with high humidity. Further research and development may focus on optimizing formulations for enhanced resilience in such challenging scenarios, thereby expanding the scope of Plastorex applications. This ongoing refinement further underscores the importance of environmental resistance as a core quality in the material's design and application.
6. Aerospace Use
Plastorex's suitability for aerospace applications hinges on its unique combination of properties. Lightweight yet high-strength materials are paramount in aerospace, enabling increased payload capacity, reduced fuel consumption, and enhanced performance. Plastorex's ability to achieve this balance directly relates to its application in this sector. The material's resistance to extreme temperatures and environmental factors found in the upper atmosphere further strengthens its suitability. Its customized formulability allows tailoring to meet specific requirements within various aircraft components.
Real-world examples include the use of Plastorex composites in aircraft fuselage structures, wings, and engine components. The high-strength-to-weight ratio of the material contributes to the overall efficiency and performance of the aircraft. Reduced weight translates to decreased fuel consumption and increased range, which are crucial factors for commercial and military aircraft alike. The application of Plastorex in this context highlights the critical role of advanced composite materials in modern aerospace design. Furthermore, the material's resistance to corrosion and fatigue under sustained stress ensures longer component lifespan, minimizing maintenance and repair costs. This translates to improved reliability and safety.
In conclusion, Plastorex's aerospace applications are driven by the material's ability to deliver high performance in a lightweight form factor. The material's tailored properties, including high strength, low weight, and environmental resistance, meet the exacting demands of aerospace engineering. The incorporation of Plastorex underscores the ongoing evolution of aerospace materials towards greater efficiency and sustainability. While challenges in manufacturing and cost remain, the potential of Plastorex for future aerospace innovations is substantial.
7. Sustainable Solutions
The connection between sustainable solutions and Plastorex lies in the material's potential to reduce environmental impact within various industries. Plastorex, as a composite material, offers a unique opportunity to replace heavier, less sustainable materials, leading to decreased resource consumption and waste generation. Lower embodied energy in manufacturing processes, reduced reliance on finite resources, and extended product lifespans through enhanced durability are all components of this sustainable benefit.
Practical examples illustrate this connection. In the automotive sector, Plastorex's lightweight properties can translate to improved fuel efficiency, leading to lower emissions and reduced reliance on fossil fuels. In construction, Plastorex's durability and resistance to environmental factors allow for longer-lasting infrastructure, reducing the frequency of replacement cycles and associated waste. Further, the material's potential for recyclability, though a factor still under development, promises a positive contribution to a circular economy. This sustainable approach extends to aerospace, where reduced weight translates to decreased fuel consumption, fostering a more sustainable flight model.
In conclusion, the connection between Plastorex and sustainable solutions is multifaceted. By offering superior performance characteristics combined with reduced environmental impact potential, Plastorex can contribute to more sustainable practices within numerous industries. However, challenges remain, including efficient recycling infrastructure and the overall cost of manufacturing and implementing this novel material. A thorough understanding of these interconnected aspects is crucial to fully realize the sustainable potential of Plastorex and related composite materials within a broader sustainability framework.
Frequently Asked Questions About Plastorex
This section addresses common inquiries regarding Plastorex, a specialized polymer composite material. Clear and concise answers are provided to facilitate understanding of its properties, applications, and associated considerations.
Question 1: What is Plastorex?
Plastorex is a synthetic polymer composite engineered for specific applications. Formulations are tailored to optimize properties like strength, durability, and resistance to environmental factors. The precise composition of this composite dictates its specific characteristics.
Question 2: What are the key advantages of using Plastorex?
Key advantages include high strength-to-weight ratios, improved resistance to corrosion and degradation, and enhanced performance in diverse environments. These attributes make Plastorex a suitable replacement for heavier, less resilient materials, leading to improved efficiency and reduced material waste.
Question 3: What industries utilize Plastorex?
Plastorex finds applications in various industries, particularly those demanding lightweight yet robust materials. These include aerospace, automotive, construction, and specialized equipment manufacturing. Tailored formulations cater to the specific requirements of each industry.
Question 4: What are the environmental considerations associated with Plastorex?
The environmental impact of Plastorex is multifaceted. While the material often reduces material usage compared to alternatives, the specific environmental footprint depends on manufacturing processes and end-of-life management. Ongoing research focuses on increasing recyclability and minimizing environmental impact.
Question 5: What are the challenges in the production of Plastorex?
Challenges in Plastorex production include optimizing manufacturing processes, ensuring consistent material properties across varying production runs, and controlling costs associated with specialized formulations. Ongoing research and development strive to overcome these challenges.
In summary, Plastorex presents a potential solution to various industrial challenges, offering enhanced performance with a focus on sustainability and reduced resource consumption. However, the material's wider adoption necessitates addressing manufacturing complexities and optimizing end-of-life management strategies.
Now, let's explore the specific manufacturing processes employed in the creation of Plastorex.
Conclusion
This exploration of Plastorex highlights its multifaceted nature as a specialized polymer composite. Key features include its customized formulability, enabling tailoring to specific performance needs in various sectors. The material's high strength-to-weight ratio is a significant advantage, particularly in applications demanding lightweight yet robust components, such as aerospace. Environmental resistance contributes to longevity and suitability for challenging environments. The material's potential for sustainable solutions through reduced resource consumption and extended product lifecycles is also noteworthy. The analysis reveals Plastorex's potential to address industrial demands while potentially contributing to a more sustainable future.
While Plastorex demonstrates substantial promise, challenges remain in optimizing manufacturing processes and ensuring cost-effectiveness. Continued research and development will be critical to advancing the material's wider adoption. Further investigation into recycling and end-of-life management strategies is necessary for full integration into a sustainable industrial landscape. The future of Plastorex hinges on the successful resolution of these challenges, positioning the material as a potential game-changer across various sectors.
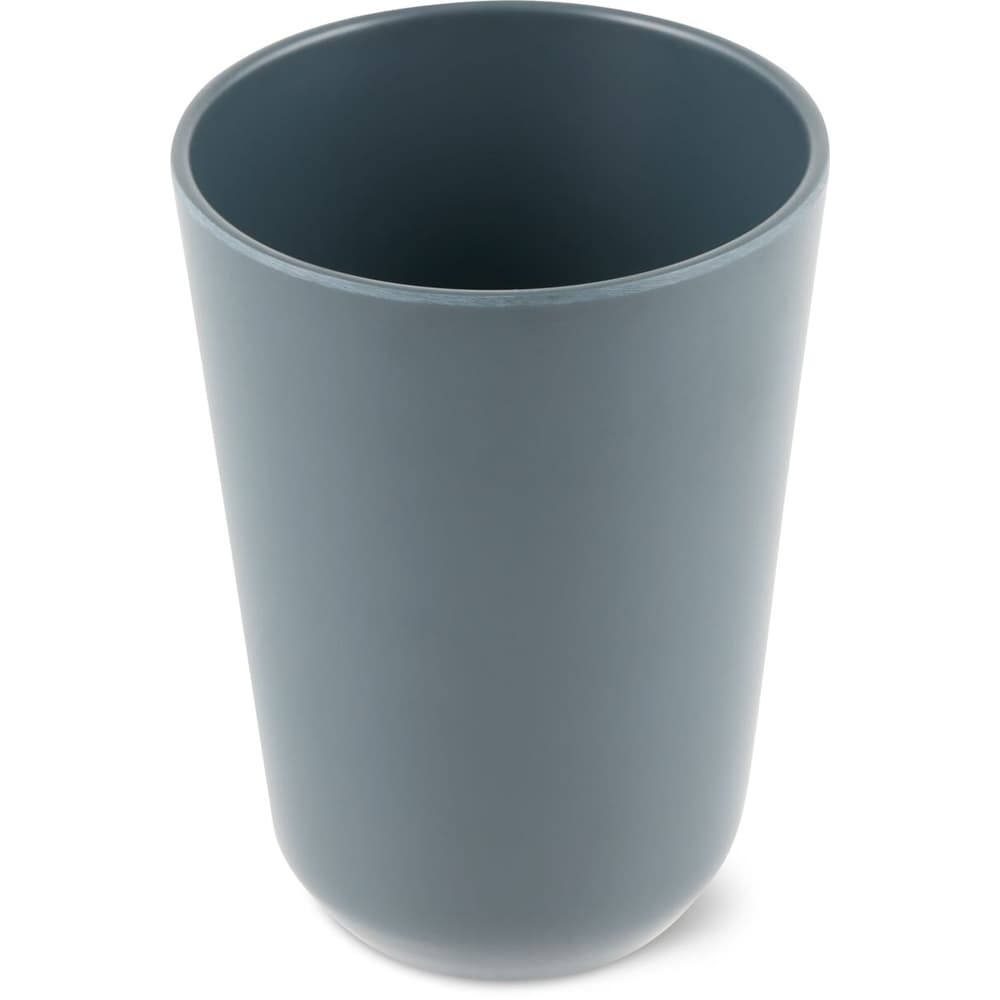
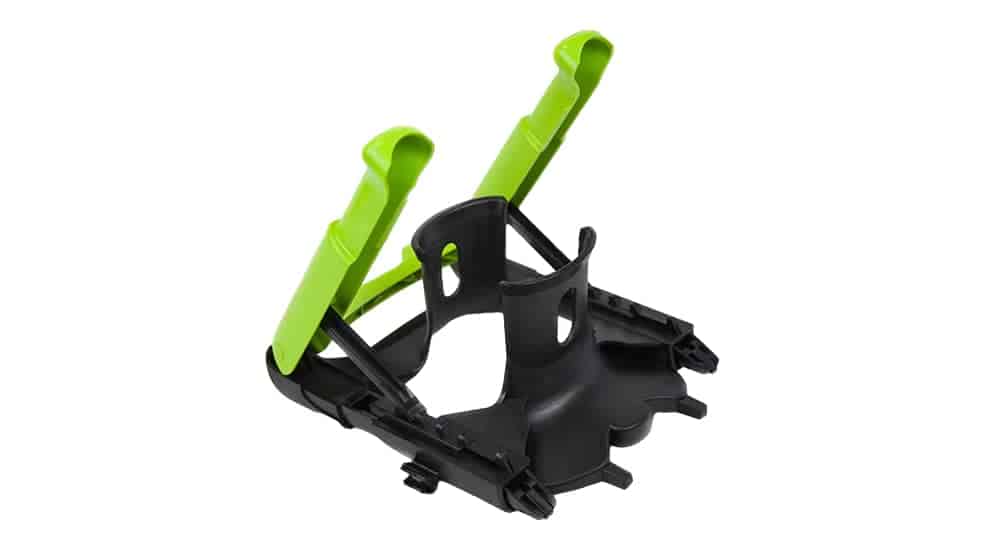
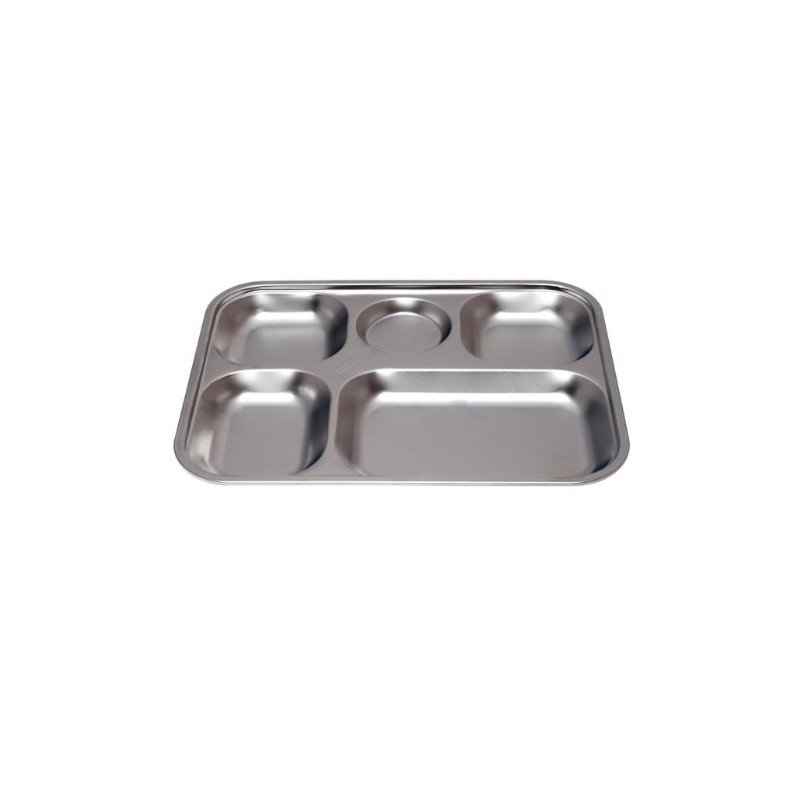
Detail Author:
- Name : Tiara Greenholt
- Username : homenick.estel
- Email : williamson.ford@hotmail.com
- Birthdate : 1981-12-21
- Address : 1124 Kuphal Court New Gia, IA 82130
- Phone : 1-719-859-3126
- Company : Bradtke-Harvey
- Job : Refractory Materials Repairer
- Bio : Repellat sunt placeat eum adipisci. Non laudantium id reprehenderit et similique commodi. Quam dolorum unde deleniti culpa.
Socials
tiktok:
- url : https://tiktok.com/@lisette4276
- username : lisette4276
- bio : Minus quisquam voluptate est et voluptates.
- followers : 5848
- following : 1778
twitter:
- url : https://twitter.com/cormier1981
- username : cormier1981
- bio : Debitis atque ratione repellat dolores. Adipisci voluptatem quia odio sed cum voluptates.
- followers : 6263
- following : 1659
instagram:
- url : https://instagram.com/lisette_xx
- username : lisette_xx
- bio : Consequuntur provident et voluptatem. Rerum eveniet quo expedita sint natus omnis.
- followers : 3476
- following : 1777
facebook:
- url : https://facebook.com/lisette.cormier
- username : lisette.cormier
- bio : Repudiandae nobis est in hic eum. Perferendis molestiae at eius.
- followers : 1917
- following : 1479