What is the significance of this specialized pipe design? This specialized pipe configuration offers unique advantages in various applications.
A specific type of pipe bend, often employed in engineering and construction projects, possesses a distinct curvature. This specialized bend might be a crucial component in a system requiring a precise change in direction for fluids or gases. The design ensures smooth transitions and minimizes pressure drops or blockages. Examples of applications include plumbing, HVAC systems, and industrial piping. The particular shape and dimensions of the bend are integral to the overall performance of the pipeline system.
The importance of this specialized pipe bend lies in its ability to efficiently convey fluids or gases. Minimizing friction losses and maintaining uniform flow is essential in many industrial and engineering settings. This design also aids in system maintenance and safety by facilitating access for inspections and repairs. Over time, the design may have evolved to optimize performance in specific applications, perhaps accounting for high pressures or unusual operating conditions. Proper selection and installation of this bend, along with other piping components, are critical to ensuring efficient and safe operations.
Moving forward, this article will delve into the specific applications and manufacturing considerations of this type of pipe fitting.
ibend pipe
Understanding the key aspects of this specialized pipe configuration is crucial for effective implementation in various applications. Its design, materials, and manufacturing processes directly influence system performance.
- Curvature
- Fluid Dynamics
- Material Strength
- Pressure Rating
- Manufacturing Process
- Dimension Accuracy
- Installation Techniques
- System Integration
Curvature dictates flow path and pressure loss. Material strength determines the bend's ability to withstand operating pressures and temperatures. Precise dimensions ensure proper system integration. Fluid dynamics, pressure ratings, and manufacturing processes all contribute to overall system efficiency and safety. Installation techniques dictate long-term structural integrity, and proper system integration ensures seamless functionality. A high-quality ibend pipe, with careful consideration of these key factors, contributes significantly to overall pipeline system reliability and efficiency. For example, a poorly manufactured bend might cause excessive pressure loss in a gas pipeline, compromising safety and output. Conversely, a correctly designed and installed bend might reduce pressure drop and increase flow rate.
1. Curvature
The precise curvature of a pipe bend, particularly within an ibend pipe design, is a critical factor influencing its overall functionality and performance. This curvature directly affects fluid flow, pressure loss, and the structural integrity of the system. Understanding the principles governing curvature is essential for optimizing the design and ensuring safe and efficient operation of piping systems.
- Flow Path and Pressure Loss
Pipe curvature dictates the path of fluids or gases within the pipe. A carefully engineered curve minimizes pressure drops by reducing turbulence and friction. Conversely, abrupt or poorly designed bends can cause significant pressure loss, impacting flow rate and efficiency. This principle is particularly important in applications where maximizing flow rate and minimizing energy consumption are paramount, such as industrial pipelines. A well-designed ibend pipe minimizes these losses.
- Stress Concentration and Structural Integrity
Curvature affects the internal stress distribution within the pipe material. Sharp bends concentrate stress, potentially leading to material fatigue and failure over time. Smooth, gradual curves, as often found in ibend pipe designs, distribute stress more evenly, increasing the pipe's lifespan. The radius of curvature is a key factor in determining the magnitude of stress concentration and thus, the pipe's structural capability.
- Access for Maintenance and Inspection
The curvature of an ibend pipe can influence the accessibility for maintenance and inspection tasks. Properly designed bends may facilitate access for technicians to perform necessary checks, repairs, or replacements. Conversely, an inappropriate curve can obstruct access, increasing maintenance costs and reducing operational efficiency.
- System Integration and Compatibility
Curvature, alongside other dimensions, must be compatible with the overall system design. Incompatible bends can cause misalignment, stress points, or even prevent complete system integration. Proper curvature, as implemented in ibend pipe designs, ensures smooth transitions and safe connections with other components.
In conclusion, the curvature of an ibend pipe is paramount to its effectiveness. Careful consideration of flow path, stress concentration, maintenance accessibility, and system integration is essential to achieving optimal performance, safety, and durability of the pipeline system.
2. Fluid Dynamics
Fluid dynamics plays a critical role in the design and performance of ibend pipes. The interaction between the flowing fluid and the pipe's curvature significantly impacts pressure drop, flow rate, and overall system efficiency. Proper understanding of fluid dynamics principles is essential for optimizing the ibend pipe's functionality. Considerations include the velocity of the fluid, its viscosity, the geometry of the bend, and the resulting forces acting upon the pipe walls. Turbulence, a common phenomenon in fluid flow, is intensified by sharp bends, increasing pressure loss and potentially leading to cavitation or erosion.
Minimizing pressure drop is crucial in numerous applications, especially in high-flow systems. A well-designed ibend pipe, taking fluid dynamics principles into account, can significantly reduce this loss. For example, in a gas pipeline transporting natural gas, minimizing pressure drop is critical for maximizing delivery efficiency and minimizing energy consumption. Conversely, an improperly designed ibend pipe, ignoring fluid dynamics principles, can result in excessive pressure drops, decreased flow rates, and potentially catastrophic operational failures. The concept is applicable to many systems, from plumbing in residential buildings to complex industrial processes like oil refining and chemical production. Calculations based on fluid dynamics principles help engineers determine optimal bend radii and pipe wall thicknesses, ensuring safe and efficient operation.
In summary, fluid dynamics is fundamental to the design and performance of ibend pipes. By correctly applying these principles, engineers can create optimal bend geometries that maximize flow efficiency, minimize pressure loss, and enhance the structural integrity of the entire piping system. Failure to adequately consider fluid dynamics can lead to significant operational inefficiencies and safety risks. The interplay between fluid properties, pipe geometry, and resulting forces is a critical area of study for designing high-performing, reliable ibend pipes across various applications.
3. Material Strength
Material strength is a critical component of ibend pipe design. The ability of the pipe material to withstand stresses and strains imposed during operation, particularly at the bend, dictates the pipe's longevity and safety. The material's tensile strength, yield strength, and resistance to fatigue are paramount. For example, a pipe material exhibiting low tensile strength will be susceptible to premature failure under sustained pressure, while a material with insufficient yield strength might deform permanently under stress, compromising the pipe's structural integrity and potentially leading to leakage or rupture. Moreover, the material's ability to resist fatigue is crucial for ibend pipes subjected to repeated or cyclical loads. This is especially critical for piping systems operating under high-pressure environments.
Specific applications demand materials with specific strength characteristics. For instance, in high-pressure gas pipelines, the pipe material must possess exceptionally high tensile strength to withstand the significant pressure exerted by the contained gas. Similarly, in situations involving fluctuating temperatures, material selection must consider thermal expansion and contraction properties, alongside strength. The choice of material directly impacts the pipe's ability to endure the stresses and strains associated with bending, and the implications for structural integrity are profound. Improper material selection can result in cracks, leaks, or catastrophic failures, thereby posing significant risks to human life and property. A high-strength material within an ibend pipe helps ensure operational safety and long-term reliability.
In conclusion, material strength is inseparable from the performance and safety of ibend pipes. Careful material selection, considering the specific application and operating conditions, is vital for ensuring durability, resistance to failure, and overall system reliability. Engineers must rigorously evaluate the material's properties under anticipated operating conditions to prevent catastrophic failures. This critical consideration, coupled with proper design and installation procedures, ensures the longevity and safety of systems incorporating ibend pipes.
4. Pressure Rating
Pressure rating is an integral aspect of ibend pipe design and selection. It defines the maximum pressure the pipe can withstand without failure. A crucial consideration when using an ibend pipe, it directly relates to the pipe material's mechanical strength and the bend's geometry. Higher pressure ratings necessitate stronger materials and more intricate bending processes to ensure structural integrity. A pipe rated for a lower pressure, used in a system exceeding that rating, risks catastrophic failure, leading to leakage, ruptures, or potentially more serious consequences.
The importance of understanding and adhering to pressure ratings cannot be overstated. Real-world examples highlight this: in a high-pressure natural gas pipeline, an ibend pipe mismatched with the system's pressure rating could result in a significant safety hazard, potentially leading to explosions or leaks with severe environmental and economic repercussions. Likewise, in a high-temperature water system, an inadequate pressure rating could lead to pipe breakage, causing damage to equipment and possible injury. Accurate pressure rating assessments are thus essential for ensuring the long-term reliability and safety of piping systems containing ibend pipes. The pressure rating isn't just a label; it's a critical safety parameter defining the limits of the ibend pipe's operation.
In summary, the pressure rating of an ibend pipe directly affects its applicability in a given system. Understanding this relationship is essential for choosing the correct pipe for a specific application and avoiding potentially hazardous situations. A thorough evaluation of operating pressures and temperatures, combined with appropriate selection based on pressure ratings, is crucial for safe and reliable pipeline systems integrating ibend pipes. Choosing the correct pressure rating is a critical design step ensuring the longevity and safety of the entire system. Ignoring these crucial aspects can lead to significant failures.
5. Manufacturing Process
The manufacturing process significantly influences the performance and reliability of ibend pipes. Precise manufacturing techniques are vital to achieving the desired curvature, maintaining material integrity, and ensuring consistent quality. Variations in manufacturing processes can lead to inconsistencies in bend radius, stress concentrations, and ultimately, the pipe's ability to withstand operating conditions. Inadequate manufacturing procedures might result in premature failure, leaks, or system malfunctions. For instance, a poorly controlled bending process could lead to material fatigue at the bend, compromising the pipe's overall structural integrity. Conversely, advanced manufacturing techniques, such as specialized bending presses or heat treatments, can create a precisely curved pipe with minimal stress concentrations, thereby extending the pipe's lifespan.
Specific manufacturing processes directly impact the final properties of an ibend pipe. Processes like hydroforming, cold bending, or heat-treating the metal used for these pipes will affect their ductility, yield strength, and fatigue resistance. The selection of the most suitable process depends on factors such as the intended application, the material's characteristics, and the required precision in the final bend. Different industrial sectors have varying tolerances for irregularities, affecting the manufacturing standards needed for compliance. In the automotive industry, high-precision bending processes are crucial for ensuring that pipes fit precisely into complex systems. In contrast, the tolerances in certain plumbing applications may be less stringent, allowing for slightly less precise manufacturing techniques. The manufacturing approach impacts the pipe's final cost, which also affects the wider cost-benefit analysis of the pipe in a project. Considerable research and development is often required to optimize manufacturing processes to achieve optimal performance and cost-effectiveness for an ibend pipe's specific application.
In conclusion, the manufacturing process is inextricably linked to the quality and performance of ibend pipes. A meticulously controlled and standardized manufacturing approach is essential for ensuring consistency, minimizing stress concentrations, and maximizing the pipe's overall lifespan. Careful consideration of the chosen manufacturing process, coupled with quality control measures, is crucial for realizing the full potential of ibend pipes in various applications. Understanding the intricate relationship between manufacturing and the final product is vital for the safe, efficient, and economical operation of systems incorporating ibend pipes. This involves continuous refinement of manufacturing procedures to address changing needs and improve final product characteristics.
6. Dimension Accuracy
Precise dimensional accuracy is paramount in the design and manufacture of ibend pipes. Variations in dimensions directly impact the pipe's functionality and safety within a system. Accurate measurements ensure compatibility with other components, proper fluid flow, and stress distribution. Inaccurate dimensions can lead to misalignment, stress concentrations, reduced efficiency, or even catastrophic failure. This applies equally to bends, elbows, and other shaped components in piping systems.
Consider a system for transporting highly pressurized gas. Slight deviations in the ibend pipe's dimensions, even seemingly minute, can create localized stress points exceeding the material's capacity. This could lead to cracks or fractures, potentially causing catastrophic leaks or explosions. Conversely, a perfectly aligned and dimensionally accurate ibend pipe ensures consistent stress distribution, preventing premature failure and extending the system's lifespan. Precise measurements and tolerances are crucial in ensuring that pipes accurately fit within the overall system and work together effectively. Examples include intricate automotive exhaust systems, high-precision hydraulic lines in machinery, and critical piping in chemical processing plants. In each case, minute variations in dimension accuracy can compromise safety and operational efficiency.
Maintaining dimensional accuracy in ibend pipe production requires stringent quality control measures throughout the manufacturing process. From initial material selection to the final bending and inspection stages, precise tolerances must be strictly adhered to. This necessitates advanced measurement technologies, skilled operators, and robust quality assurance procedures. The consequences of neglecting dimensional accuracy in ibend pipe production can be substantial, ranging from increased operational costs due to rework and repairs to serious safety risks that can have significant financial and human consequences. Consequently, rigorous adherence to standardized dimensional tolerances for ibend pipes is critical for safe and reliable operation in various industries.
7. Installation Techniques
Installation techniques directly influence the performance and longevity of ibend pipes. Proper installation procedures are crucial for ensuring the pipe's ability to withstand operating pressures and stresses, minimizing potential leaks, and maximizing system efficiency. Inadequate installation can lead to premature failure, compromising safety and requiring costly repairs. In contrast, meticulous installation methods contribute to a pipe's long-term reliability and reduce the risk of incidents. A poor installation might lead to localized stress concentrations at the bend, potentially causing fractures or fatigue failures over time, highlighting the critical role of proper installation techniques.
Several factors necessitate careful consideration during installation. Precise alignment of the ibend pipe with the surrounding piping system is critical to avoid misalignment stresses. Correct support systems are equally vital to prevent excessive bending moments or deflection that can compromise structural integrity. Proper anchoring of the pipe and careful consideration of thermal expansion and contraction are imperative. For example, in high-temperature environments, neglecting thermal expansion considerations can lead to stress-induced fractures in the pipe bend over time. Moreover, the installation procedure should ensure that the pipe is correctly supported and secured to prevent movement or vibration-induced stress. In certain applications, like high-pressure pipelines, the meticulous use of gaskets and seals at connection points is essential to prevent leaks. Proper installation minimizes the risk of such incidents. Furthermore, adhering to manufacturer specifications for installation procedures is essential for achieving optimal performance and avoiding unexpected problems.
In conclusion, installation techniques are an inseparable aspect of ibend pipe performance. Carefully executed installation procedures are not merely a secondary step but a critical component directly impacting the ibend pipe's longevity, efficiency, and safety. Understanding and adhering to these techniques is vital in ensuring the reliable operation of any piping system incorporating ibend pipes. Inadequate installation can lead to significant problems, while proper techniques contribute to long-term system dependability. This underscores the importance of comprehensive training and adherence to safety protocols throughout the installation process.
8. System Integration
System integration is fundamental to the effective application of ibend pipes. The success of a piping system, including an ibend pipe, hinges on its seamless integration with other components. This encompasses not only physical connection but also the compatibility of material properties, operational pressures, and flow characteristics. A poorly integrated ibend pipe can lead to stress concentrations, leaks, reduced flow efficiency, and ultimately, system failure. Conversely, a well-integrated ibend pipe is a key component in a cohesive and reliable system.
Consider a high-pressure industrial process. An ibend pipe's seamless integration with the upstream and downstream piping, valves, and pumps is critical. Mismatched material properties between the ibend pipe and connecting components can lead to corrosion or stress-induced failures. Similarly, inadequate consideration of pressure ratings during system design can cause the ibend pipe to fail under the operating pressure. In a commercial HVAC system, integrating an ibend pipe with ductwork, air handling units, and associated controls ensures consistent airflow and optimal temperature regulation. An improperly integrated ibend pipe could restrict airflow, negatively impacting the system's efficiency. In each case, the overall system performance and longevity are directly affected by the quality of system integration, including the selection and installation of the ibend pipe.
In conclusion, system integration is not merely an ancillary consideration but a core component of any piping system containing an ibend pipe. Proper integration, encompassing material compatibility, dimensional accuracy, and adherence to design specifications, is crucial for safety, reliability, and cost-effectiveness. A thorough understanding of how the ibend pipe interacts with other components within the larger system is essential to guarantee optimal operation and avoid costly repairs or failures. This understanding is crucial for both design and maintenance protocols.
Frequently Asked Questions about Ibend Pipes
This section addresses common inquiries regarding ibend pipes, offering clear and concise answers to potential concerns. Understanding these details can help ensure proper application and system longevity.
Question 1: What distinguishes an ibend pipe from other types of pipe bends?
Ibend pipes exhibit a specific, often optimized, curvature design. This particular design minimizes stress concentrations and pressure losses during fluid flow, compared to standard bends. The precise curvature and radius, often calculated using fluid dynamics principles, are key differentiators, contributing to enhanced system performance.
Question 2: What materials are commonly used for ibend pipes, and why?
Materials like carbon steel, stainless steel, and various alloys are used, selected based on the system's operating conditions. Factors such as pressure ratings, temperature ranges, and potential chemical interactions determine the most suitable material. Choosing the appropriate material is crucial for the pipe's resistance to corrosion, stress, and other environmental factors throughout its operational lifetime.
Question 3: How does the manufacturing process impact ibend pipe performance?
Precision in the manufacturing process is critical. Factors such as the bending technique and quality control measures directly impact the pipe's dimensional accuracy, stress distribution, and overall structural integrity. Rigorous manufacturing processes minimize irregularities and potential weaknesses, leading to longer service life.
Question 4: What are the crucial considerations when integrating an ibend pipe into a system?
Careful attention must be given to compatibility with other piping components, including proper dimensional matching, material compatibility, and pressure ratings. The system's operating parameters, including pressure and temperature, must be carefully considered. The installation method directly affects the system's long-term integrity and safety.
Question 5: What are potential failure modes for ibend pipes, and how can they be mitigated?
Potential failures include stress-induced cracking, leaks at connections, and material fatigue. Preventing such issues requires meticulous design, high-quality materials, precise manufacturing, and proper installation techniques. Thorough system evaluation, including pressure testing and regular inspections, is essential to mitigate failure risk.
Understanding these FAQs provides valuable insight into the critical aspects of ibend pipe design, application, and maintenance. By addressing these frequently asked questions, organizations can effectively integrate these specialized pipes into their systems for optimal performance and safety.
The following section will explore specific applications of ibend pipes in more detail.
Conclusion
This exploration of ibend pipes underscores the multifaceted nature of their design and application. Key factors, including curvature, fluid dynamics, material strength, pressure rating, manufacturing processes, dimensional accuracy, installation techniques, and system integration, all contribute to the pipe's overall performance and reliability. The precise design and implementation of ibend pipes are crucial in various applications, from high-pressure industrial pipelines to complex HVAC systems. Failure to meticulously consider these interconnected elements can lead to significant operational inefficiencies, safety hazards, and costly repairs. Consequently, a thorough understanding of these factors is paramount for successful design, installation, and maintenance.
The information presented highlights the critical importance of ibend pipe technology in modern engineering. Precise fabrication, adhering to established standards and rigorous quality control, is essential for achieving optimal performance and safety. Further research and development in advanced manufacturing techniques and materials could lead to even more robust and efficient ibend pipes in the future. A commitment to rigorous design principles, coupled with adherence to established safety protocols, is essential to ensure the long-term integrity and reliability of systems incorporating this specialized pipe technology.
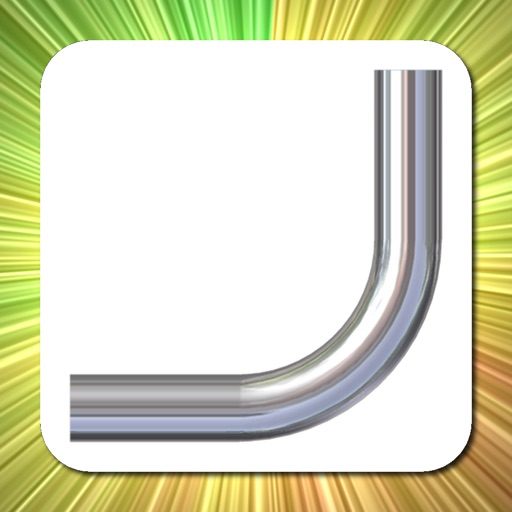
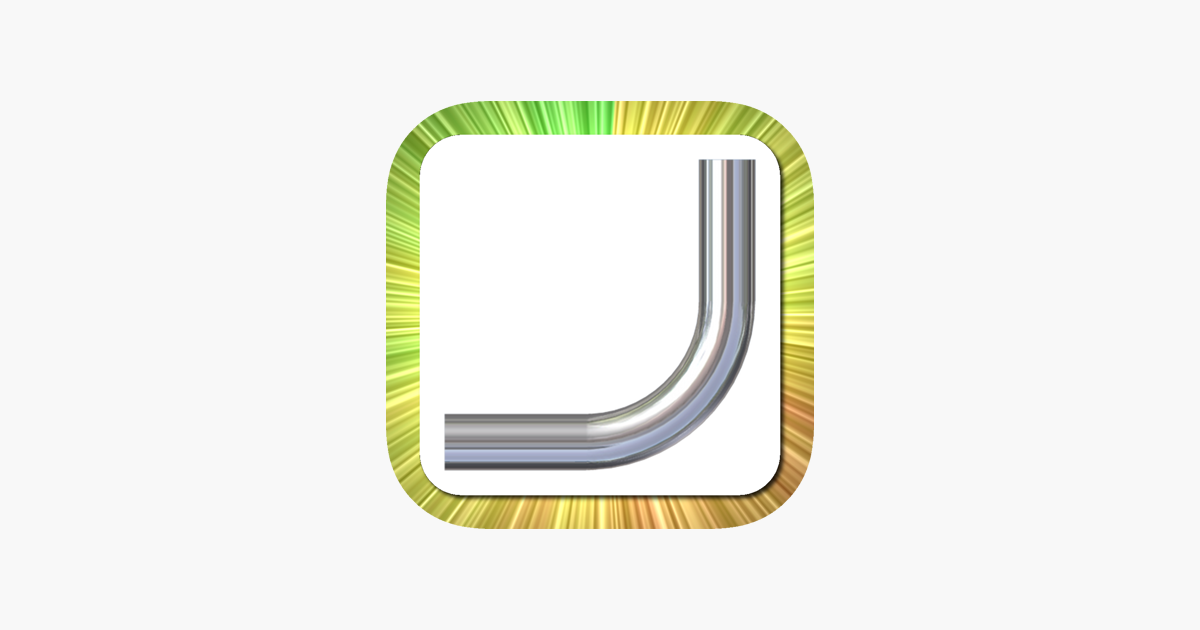
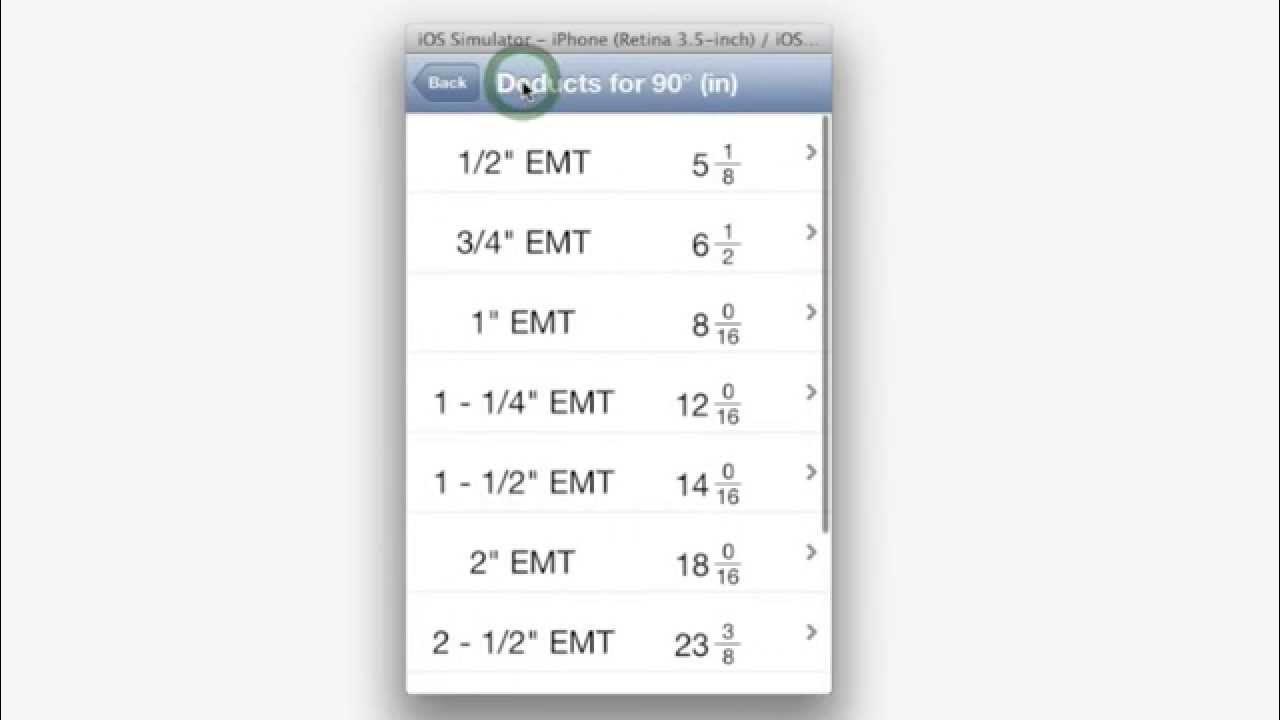
Detail Author:
- Name : Karl Emard MD
- Username : maymie.boyer
- Email : jakob94@hotmail.com
- Birthdate : 1984-08-10
- Address : 59795 Hessel Course Port Roman, SC 91538-2649
- Phone : 734.870.4213
- Company : Prosacco Group
- Job : Physicist
- Bio : Et veniam modi sit culpa cum et. Similique distinctio voluptatem consequatur facilis. Vel hic in sed eligendi.
Socials
tiktok:
- url : https://tiktok.com/@patsy_official
- username : patsy_official
- bio : Perspiciatis ad nihil et quasi animi asperiores.
- followers : 2875
- following : 1525
facebook:
- url : https://facebook.com/corwinp
- username : corwinp
- bio : Nam suscipit aut fugit officia soluta omnis dolores.
- followers : 4863
- following : 1018
instagram:
- url : https://instagram.com/pcorwin
- username : pcorwin
- bio : Et maxime vel consequatur dignissimos. Quae facere assumenda modi. Veniam quam dolore iusto sit.
- followers : 4942
- following : 2149
linkedin:
- url : https://linkedin.com/in/pcorwin
- username : pcorwin
- bio : Expedita ex quos tempora tempora.
- followers : 6733
- following : 2511