How does the execution of manufacturing processes drive economic success and efficiency? A robust production process is fundamental to a thriving economy.
Production execution encompasses the comprehensive management of all activities involved in the creation of goods or services. This includes planning, scheduling, resource allocation, quality control, and continuous improvement efforts throughout the entire production lifecycle. For example, a car manufacturer might utilize sophisticated software to track the movement of parts through assembly lines, ensuring optimal flow and minimizing bottlenecks. This precise coordination, along with the rigorous application of quality standards, is essential for delivering a high-quality product on time and within budget. Another illustration could be a restaurant managing its kitchen operations, from ingredient procurement to dish preparation and serving, following a well-defined procedure to deliver customer satisfaction.
Effective production execution offers several key advantages. It enhances efficiency by optimizing resource utilization, reducing waste, and streamlining processes. This, in turn, leads to lower production costs and increased profitability. By maintaining consistent quality standards, a well-managed production process builds a positive brand image, fostering customer trust and loyalty. Historical context reveals that the pursuit of improved production methods has been a constant driver of technological advancement and economic growth, from the assembly line innovations of the early 20th century to the modern use of automation and data analytics in today's manufacturing settings.
Performing Production
Effective production hinges on meticulous planning and execution. These key aspects are critical to achieving optimal results.
- Planning
- Scheduling
- Resource allocation
- Quality control
- Process improvement
- Efficiency
- Cost management
Planning and scheduling lay the groundwork for successful production. Resource allocation ensures appropriate materials and personnel are available. Quality control mechanisms prevent defects and maintain product consistency. Process improvement strategies continually refine operations, enhancing efficiency. High efficiency translates into lower costs. Sound cost management ensures profitability. These aspects are interconnected, with strong planning leading to effective scheduling, efficient resource allocation, and superior quality control, ultimately driving improvement and cost management. For example, a well-defined production plan for a manufacturing plant will optimize the use of materials, minimize delays, and contribute to overall cost reduction, showcasing the direct link between each aspect and successful outcomes. Successful production execution is not merely a series of individual steps but a tightly integrated process.
1. Planning
Effective production hinges on meticulous planning. Strategic planning is not a standalone activity but a foundational element intrinsically linked to the successful execution of manufacturing processes. Without robust planning, resources may be misallocated, timelines missed, and quality compromised, ultimately impacting overall productivity and profitability. Sound planning forms the bedrock upon which successful production is built.
- Resource Allocation and Optimization
Accurate forecasting of material needs is paramount. Planning encompasses meticulous resource assessments, ensuring sufficient raw materials, skilled labor, and machinery are available at the right time and in the correct quantities. This proactive approach prevents bottlenecks and delays, contributing directly to efficient production. For instance, a manufacturing plant planning for a surge in demand needs to anticipate and acquire the required materials in advance to maintain a smooth production flow. Conversely, failing to plan for fluctuations in demand can lead to shortages and production disruptions.
- Process Design and Standardization
Planning includes the design and standardization of production processes. Clear, well-defined procedures ensure consistent product quality and reduce errors. This detailed planning also streamlines workflows, improving operational efficiency. A standardized procedure for assembling a product, for example, will minimize inconsistencies and potential faults. Failing to properly standardize procedures leads to variability in product quality and increased production time.
- Timeline Management and Sequencing
Production planning involves establishing realistic timelines for each stage of the production process. Sequencing tasks logically to avoid conflicts and dependencies is crucial for adhering to deadlines and maximizing output. A well-structured timeline for a manufacturing project will allow proper allocation of resources and coordination among various departments. Poorly planned timelines, on the other hand, lead to delays, missed deadlines, and escalated production costs.
- Contingency Planning and Risk Mitigation
Proactive planning anticipates potential disruptions and risks, establishing backup strategies and contingency plans for addressing unforeseen issues. This includes preparing for equipment malfunctions, material shortages, or unexpected delays. For instance, a manufacturing company might have backup suppliers for crucial components to mitigate the impact of supply chain disruptions. Without such planning, production may be severely hampered by unexpected problems.
In conclusion, planning is an integral aspect of successful production execution. Well-defined plans for resource allocation, process standardization, timeline management, and risk mitigation are crucial for efficiency, quality, and profitability. Strong planning leads to a smoother, more controlled production process, reducing potential issues and maximizing the overall output.
2. Scheduling
Scheduling is intrinsically linked to effective production. Optimal scheduling directly impacts the efficiency and overall success of production processes. Proper scheduling ensures resources are allocated optimally, tasks are completed on time, and potential bottlenecks are mitigated. This proactive approach reduces delays and waste, contributing to cost-effectiveness and enhanced productivity. Consider a manufacturing facility producing consumer electronics. Efficient scheduling ensures parts arrive precisely when needed on the assembly line, minimizing idle time and maximizing output. In contrast, poor scheduling leads to delays, equipment downtime, and ultimately, a reduction in production volume and an increase in operational costs.
The importance of scheduling extends beyond the factory floor. In a service-oriented business, such as a restaurant, meticulous scheduling of staff, orders, and kitchen operations is crucial. Accurate staffing schedules prevent understaffing during peak hours and overstaffing during slower periods, saving labor costs. Similarly, scheduling delivery routes for a logistics company ensures timely delivery and optimized fuel usage, impacting profitability and customer satisfaction. The strategic allocation of resources dictated by a well-organized schedule is fundamental to any operational process.
In essence, scheduling in production forms a critical bridge between planning and execution. It translates plans into tangible actions, optimizing resource utilization and ensuring timely completion of tasks. Effective scheduling minimizes disruptions, allowing for smooth and predictable workflows. Without proper scheduling, production processes become vulnerable to delays, inefficiencies, and ultimately, reduced output. The connection between scheduling and successful production is undeniable; a well-structured schedule is fundamental to a robust and profitable operation in any industry.
3. Resource Allocation
Optimal resource allocation is fundamental to successful production. The efficient and effective utilization of available resourcesmaterials, personnel, and equipmentdirectly impacts the overall output and profitability of any production process. Without a strategic approach to allocation, potential bottlenecks, inefficiencies, and wasted resources can significantly hamper production efforts. This exploration examines critical facets of resource allocation in the context of production.
- Material Management
Careful planning and allocation of raw materials are critical. Anticipating future needs and securing timely supplies is essential to avoid production halts. Accurate inventory management, minimizing waste, and employing just-in-time delivery systems are crucial for maintaining a steady production flow. For example, a car manufacturer needs precise calculations to ensure a constant supply of steel, electronics, and other components to prevent production bottlenecks. Effective material allocation directly influences production speed, quality, and cost-effectiveness.
- Labor Allocation
Assigning the right personnel to specific tasks is crucial. Considering employee skills, experience, and workload capacity is vital. Optimizing labor allocation prevents overworking some employees while others remain underutilized. This involves assessing job roles, skill sets, and workloads across the production process. In a food processing plant, allocating workers with expertise in cutting vegetables to that task ensures efficiency and precision. Inadequate labor allocation results in delays, errors, and decreased overall productivity.
- Equipment Utilization
Allocating and maintaining optimal equipment utilization is vital. Consideration should be given to machine capabilities, maintenance schedules, and potential downtime. Preventive maintenance and efficient scheduling minimize disruptions. In a printing press facility, allocating printing presses to projects with similar dimensions and colors optimizes resource use and reduces setup time. Inadequate equipment allocation leads to wasted time, decreased capacity, and increased production costs.
- Financial Resources
Allocating financial resources effectively across the production process is crucial. Budgeting for materials, labor, and equipment maintenance is essential. Proper financial planning allows for accurate estimations of costs and profits. A bakery, for example, must effectively allocate funds to acquire ingredients, pay staff, and maintain equipment to ensure profitability. Lack of financial planning can lead to operational issues and ultimately, business failure.
In conclusion, effective resource allocation significantly influences the performance of production. A strategic and meticulous approach to material, labor, equipment, and financial resources yields improved efficiency, reduced costs, and enhanced production output. By addressing these aspects, organizations can optimize their production processes and achieve greater profitability and sustainability.
4. Quality Control
Quality control is not a separate entity from production; it is an integral component deeply intertwined with every stage of the process. A robust quality control system directly influences the efficiency, cost-effectiveness, and reputation of a production operation. Maintaining consistent quality standards minimizes defects, reduces waste, and ultimately, boosts profitability. Consider a manufacturing plant producing consumer electronics. Implementing rigorous quality checks at every production stage prevents faulty components from reaching the assembly line, thereby minimizing rework and costly replacements. This proactive approach to quality control is crucial to ensuring a high-quality final product and a satisfied customer base. The absence of effective quality control can lead to decreased productivity, significant financial losses, and ultimately, reputational damage.
Effective quality control measures extend far beyond the factory floor. A restaurant, for instance, relies on quality checks at every stepfrom ingredient sourcing to food preparation and presentation. Inconsistent quality in food preparation can lead to dissatisfied customers, negative reviews, and lost revenue. Similarly, a service industry like a call center that provides technical support employs quality control mechanisms to ensure consistency in customer interactions, promoting positive customer experiences and building brand loyalty. By establishing standards and implementing checks, these operations improve customer satisfaction and brand value. In each case, the presence of effective quality control practices directly translates to enhanced customer experiences and organizational success.
In summary, quality control is not simply a checklist or set of procedures; it is a crucial element of successful production. Its impact extends from preventing defects and reducing costs to enhancing customer satisfaction and building a strong brand reputation. A company that integrates quality control as a core value within its production strategy fosters sustainable growth and long-term success. By understanding the seamless connection between quality control and production, organizations can develop and implement strategies for enhancing output, improving processes, and minimizing operational losses. Addressing quality control proactively empowers production teams to identify potential issues early, resulting in more efficient workflows and a higher overall return on investment.
5. Process Improvement
Process improvement is inextricably linked to effective production. Optimizing procedures directly impacts efficiency, productivity, and profitability. By systematically analyzing and refining existing methods, organizations can streamline operations, reduce waste, and enhance overall performance. This exploration examines key facets of process improvement and their influence on the execution of production.
- Waste Reduction Strategies
Identifying and eliminating waste in all forms materials, time, effort, or resources is a core aspect of process improvement. Lean methodologies, for example, focus on minimizing waste in production processes by eliminating unnecessary steps and streamlining workflows. In manufacturing, implementing lean principles can involve reorganizing assembly lines to minimize movement, standardizing procedures to reduce errors, or implementing just-in-time inventory systems. Reducing waste not only increases efficiency but also lowers production costs, leading to higher profitability. A printing press, for instance, can improve its process by eliminating unnecessary steps in the paper handling process or reducing material waste through pre-cutting procedures.
- Automation and Technology Integration
Automation and the integration of advanced technologies play a pivotal role in process improvement. Automation can handle repetitive tasks, enhancing speed and precision. Implementing robotic process automation or incorporating software systems for inventory management, quality control, or order tracking can significantly streamline production processes and reduce errors. In logistics, the use of GPS tracking, automated warehousing systems, and route optimization software streamlines delivery processes, improving efficiency and reducing delays. However, successful implementation requires careful planning and consideration of potential disruptions, such as a dependence on the reliability of software systems.
- Data Analysis and Metrics
Data analysis is critical for understanding process bottlenecks and identifying areas for improvement. By tracking key metrics like production time, defect rates, and resource utilization, organizations can gain valuable insights into areas needing attention. Data analysis provides a roadmap for process improvements by revealing trends, patterns, and correlations that might be missed through traditional observation. Analyzing sales data for a retail outlet, for instance, might highlight trends in customer preferences that lead to inventory adjustments, thereby improving the efficiency of stock management.
- Employee Empowerment and Training
Empowering employees to participate in process improvement initiatives is a vital aspect. By soliciting feedback from frontline workers, organizations can identify inefficiencies and uncover novel approaches. Training programs help employees develop new skills, adopt best practices, and contribute effectively to process enhancement. Well-trained employees are better equipped to identify potential improvements in procedures, leading to a more engaged and productive workforce. A restaurant, for instance, could introduce training programs for waitstaff on efficient order taking and table management, resulting in faster service and customer satisfaction.
These facets demonstrate the multifaceted approach required for successful process improvement. By adopting a systematic approach to waste reduction, technology integration, data-driven analysis, and employee engagement, organizations can build more efficient, productive, and profitable production processes. These improvements, in turn, contribute significantly to the overall success of the production operation.
6. Efficiency
Efficiency in production is not merely a desirable trait; it is a fundamental component of successful operations. Optimizing production processes for efficiency directly impacts output, resource utilization, and profitability. A highly efficient production system minimizes waste, maximizes output, and reduces operational costs. For example, a streamlined manufacturing process with minimal downtime and efficient material flow results in higher production volumes and reduced per-unit costs, ultimately boosting profitability.
The connection between efficiency and performing production is deeply rooted in effective resource management. Efficient production systems utilize available resourceslabor, materials, and equipmentin a manner that minimizes idleness and maximizes output. This meticulous allocation translates directly into cost savings. Furthermore, efficient procedures often reduce the likelihood of errors and defects, minimizing rework and associated expenses. Consider a fast-food restaurant optimizing its order-taking and kitchen processes. Efficient workflows translate into faster service times, fewer mistakes, and a more satisfied customer base, all contributing to higher profits.
Understanding the importance of efficiency in performing production is crucial for sustainable growth and competitiveness. A lack of efficiency can lead to significant operational inefficiencies, increased costs, and potentially, market share losses. Businesses failing to optimize production processes risk falling behind competitors. The practical application of efficiency principles, including streamlining workflows, minimizing waste, and maximizing resource utilization, is essential for any organization aiming to remain competitive in the long term. Successfully implementing efficiency strategies ensures a more profitable and sustainable future for any production operation.
7. Cost Management
Cost management plays a critical role in successful production. Effective cost management is not a separate function but an integral part of the overall production process. It encompasses a range of activities aimed at optimizing resource allocation and minimizing expenses without compromising quality or output. A well-managed cost structure allows for greater profitability and facilitates investment in further process improvements. For instance, a manufacturing company achieving cost reductions through optimized material usage can reinvest these savings in research and development, leading to more efficient and innovative production methods in the long run.
Several factors directly connect cost management to production performance. Precise budgeting for raw materials, efficient labor scheduling, and judicious equipment maintenance are crucial components. Minimizing waste throughout the production cycle from raw material procurement to finished product dispatch is vital. Implementing strategies like just-in-time inventory systems, reducing energy consumption, and optimizing transportation routes all directly contribute to cost reduction. A well-managed supply chain, for example, ensures timely delivery of components at the lowest possible cost, which directly impacts production timelines and overall production expenses. Companies that effectively manage these elements exhibit superior production efficiency and profitability.
Understanding the interplay between cost management and production is essential for long-term success. Successful cost management in production fosters a culture of efficiency and resourcefulness. By optimizing resource allocation, minimizing waste, and consistently controlling costs, organizations create a platform for growth and stability. Challenges like fluctuating market prices, unpredictable supply chain disruptions, or unexpected equipment malfunctions necessitate agile and adaptable cost management strategies. Navigating such complexities requires a proactive approach, focusing on continuous improvement and adapting to market dynamics. Ultimately, cost management acts as a critical tool in optimizing production processes, fostering profitability, and ensuring the long-term viability of any production-oriented organization.
Frequently Asked Questions about Production Execution
This section addresses common questions regarding the execution of production processes. These questions aim to clarify key concepts and dispel potential misconceptions.
Question 1: What is the difference between production planning and production scheduling?
Production planning outlines the overall strategy for producing goods or services, encompassing resource allocation, process design, and timelines. Production scheduling, on the other hand, takes those plans and defines specific tasks, assigning them to resources, and setting deadlines for each step in the production process. Planning sets the stage, while scheduling brings the plan to life by defining the operational execution.
Question 2: How does automation improve production efficiency?
Automation streamlines processes by handling repetitive tasks with greater speed and accuracy than human workers. This leads to reduced errors, minimized downtime, and increased output. Furthermore, automation often allows for 24/7 operation, enhancing overall production capacity.
Question 3: What are the key indicators of a successful production process?
Key indicators include meeting production targets, maintaining quality standards, minimizing waste, adhering to timelines, and optimizing resource utilization. Successful production strives for efficiency, cost-effectiveness, and consistent quality outputs.
Question 4: How can quality control enhance production outcomes?
Quality control implemented at various stages of the production process prevents defects, identifies issues early, and minimizes the need for costly rework. This, in turn, leads to higher product quality, reduced waste, and increased customer satisfaction.
Question 5: What role does data analysis play in process improvement?
Data analysis provides insights into production bottlenecks, inefficiencies, and areas requiring improvement. By tracking key performance indicators (KPIs) and analyzing production data, organizations can identify trends, predict future issues, and implement targeted solutions to optimize workflows and reduce costs.
In conclusion, effective production execution relies on a comprehensive understanding of planning, scheduling, resource allocation, quality control, and process improvement. The skillful implementation of these elements ensures efficient operations, minimizes waste, and ultimately enhances the profitability and sustainability of any production enterprise.
Next, we will explore the importance of lean principles in enhancing production efficiency.
Conclusion
This exploration of production execution underscores the critical role of meticulous planning, efficient scheduling, optimized resource allocation, rigorous quality control, and continuous process improvement in achieving optimal results. The interconnectedness of these elements is paramount; a weakness in one area can cascade throughout the entire production process, impacting efficiency, cost-effectiveness, and overall profitability. Effective production management demands a comprehensive understanding of these interconnected aspects, enabling organizations to navigate challenges, adapt to market fluctuations, and achieve sustainable growth. The discussed strategies, from resource allocation to waste reduction, highlight the multifaceted approach necessary for success in today's dynamic business environment.
Production execution is not a static process but an ongoing endeavor requiring adaptation and innovation. Maintaining a focus on continuous improvement, fostering a culture of quality, and embracing technological advancements are vital for staying ahead of the curve. The future of production hinges on organizations' ability to anticipate and respond to evolving market demands while optimizing their internal operations. Ultimately, the successful execution of production is fundamental to sustained economic growth and the creation of value in any industry.
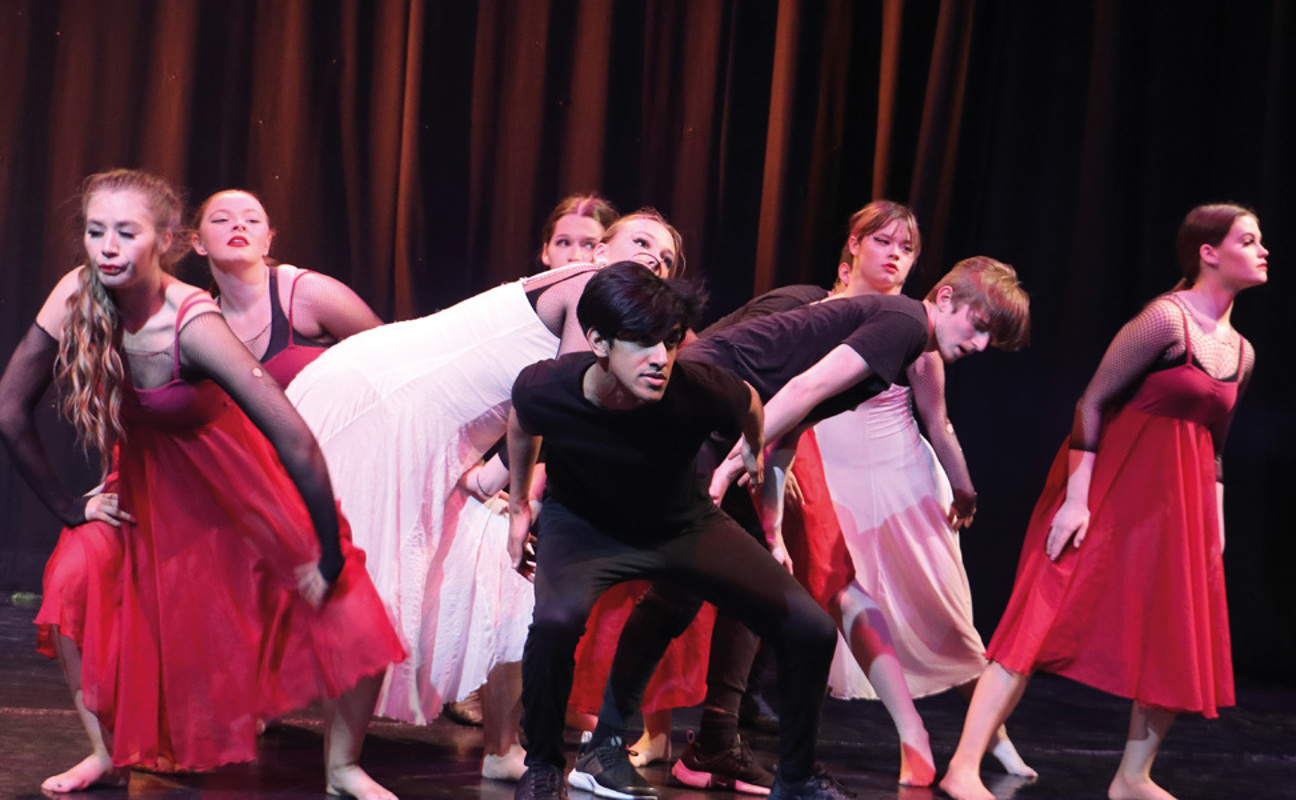
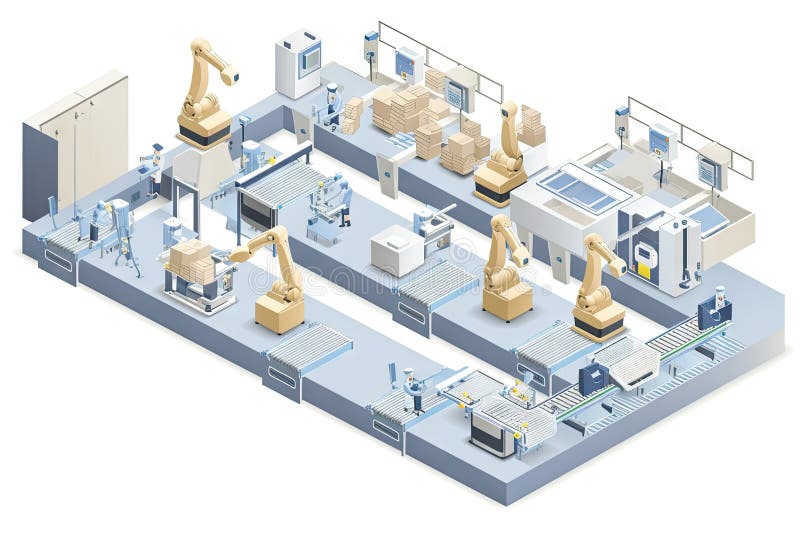
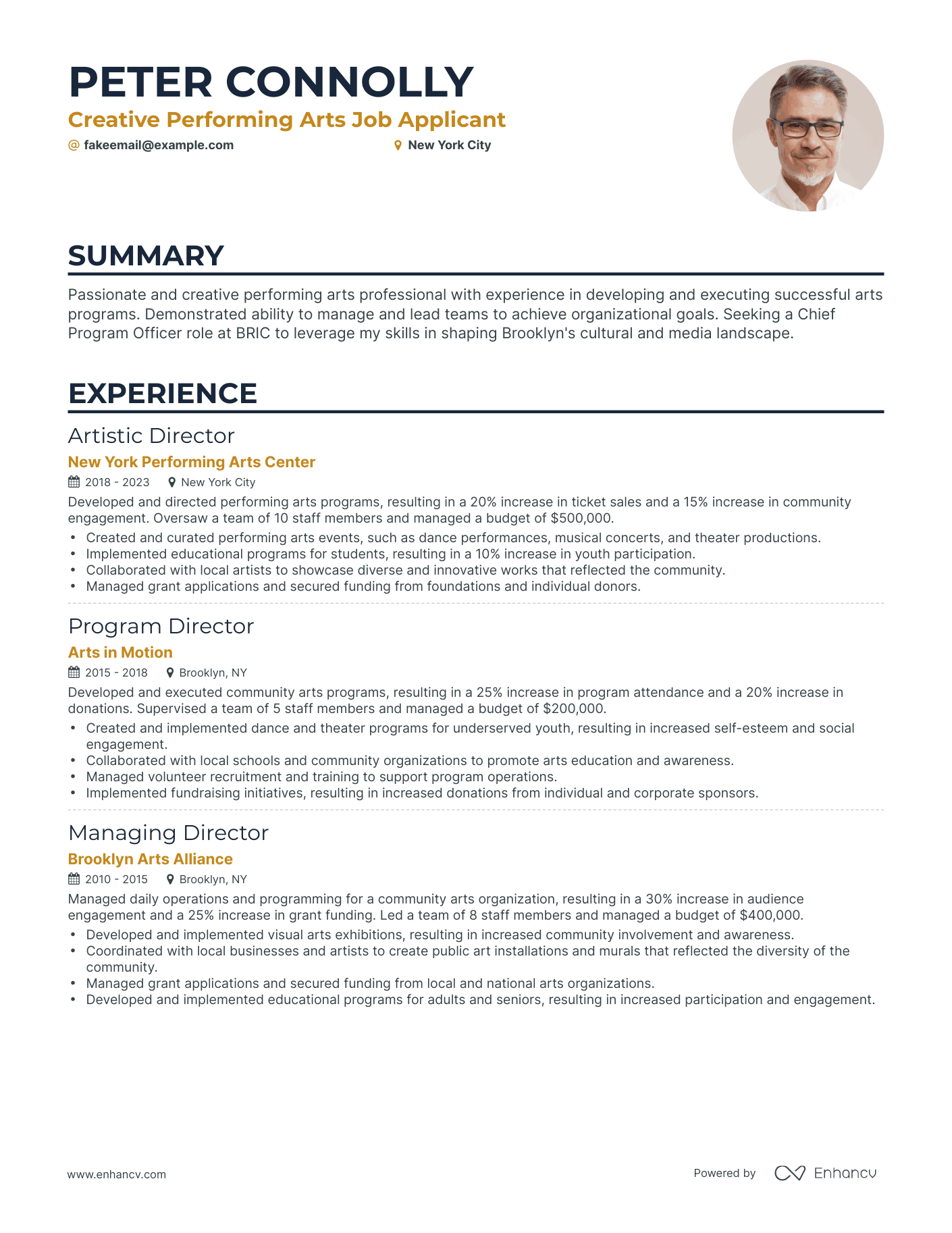
Detail Author:
- Name : Dr. Seth Kessler DVM
- Username : frederic99
- Email : bryon62@yahoo.com
- Birthdate : 1993-03-01
- Address : 6397 Jana Falls Suite 459 South Camron, VA 31854-6946
- Phone : +13864390264
- Company : Von-Orn
- Job : Auditor
- Bio : Sapiente et consequatur perspiciatis ut. Dolorem nihil rerum necessitatibus quo. Excepturi aliquam quo tempora ex hic voluptate et. Mollitia alias sed recusandae sint quam magni est.
Socials
twitter:
- url : https://twitter.com/devan_id
- username : devan_id
- bio : Esse sed facere in esse. Corporis reprehenderit vitae sunt dolore sapiente. Eos fugiat accusantium doloremque iure atque dolorum accusamus. Ex rerum quo ut.
- followers : 3136
- following : 1626
instagram:
- url : https://instagram.com/devan_o'kon
- username : devan_o'kon
- bio : Omnis consequatur ex ea dolor reiciendis et. Neque qui laborum earum. Eos culpa voluptatum tempora.
- followers : 3448
- following : 12
tiktok:
- url : https://tiktok.com/@do'kon
- username : do'kon
- bio : Rerum neque aut quidem in et repellat ut. Exercitationem impedit nemo esse ut.
- followers : 5292
- following : 1831