What is a Power Take-Off (PTO) system on a Brayton engine, and why is it crucial?
A Power Take-Off (PTO) system, often used in conjunction with Brayton engines, allows for the extraction of mechanical power from the engine's rotating components. This extracted power can then be used to drive various auxiliary equipment, significantly expanding the engine's capabilities beyond its primary function. For instance, a PTO system in a power generation plant might drive a water pump or compressor. The specific configuration of a PTO system is tailored to the requirements of the connected equipment.
The importance of this system lies in its ability to provide additional functionality. By leveraging the engine's rotational energy, a PTO system can reduce the need for separate power sources, thereby increasing overall efficiency. This efficiency enhancement translates to cost savings and reduced environmental impact. Moreover, a well-designed PTO system allows for greater flexibility in applications, extending the versatility of the Brayton engine to a broader range of tasks. Historically, PTO systems have been crucial for applications ranging from agricultural machinery to industrial processes, and their adaptability to modern engine designs ensures continued relevance.
Transitioning now to a deeper exploration of specific applications and designs of PTO systems within the broader realm of mechanical engineering.
Brayton PTO
Power Take-Off (PTO) systems, integral to Brayton engine operation, present critical facets affecting efficiency and application versatility.
- Power extraction
- Auxiliary equipment
- Engine output
- System design
- Efficiency gains
- Reduced emissions
- Application flexibility
These aspects, taken together, define the functionality and significance of a Brayton PTO. Power extraction from the engine's rotational energy drives auxiliary equipment, like compressors or pumps, optimizing engine output. System design choices determine efficiency gains and reduced emissions. For instance, a sophisticated PTO design on a gas turbine power plant could drive generators while maintaining peak performance and minimal environmental impact. The resulting application flexibility caters to diverse needs, from industrial applications to specialized off-road equipment. This highlights the crucial role of a well-engineered Brayton PTO in modern power generation and industrial settings.
1. Power Extraction
Power extraction, a fundamental element of any power take-off (PTO) system, is the process of harnessing mechanical energy from a prime mover, in this case, a Brayton engine. This extracted power isn't simply diverted; it's carefully managed to drive auxiliary equipment. The design of the PTO system directly impacts the amount of power available for extraction, as well as its efficiency. Optimizing this extraction process is critical for maximizing overall system performance.
Consider a gas turbine power plant. A Brayton engine powers the plant. A well-designed PTO system allows extracting power from the engine's rotating shaft to drive a compressor for air intake or a generator for electricity generation. This decoupling of the engine's primary function from secondary tasks allows for optimized performance of each component. A poorly designed PTO, conversely, may result in power losses, reduced efficiency, and decreased overall output. In agricultural applications, a PTO system extracts rotational energy to power implements such as harvesters and sprayers. Similarly, in industrial processes, a PTO system might drive pumps or conveyors.
Understanding the intricate connection between power extraction and Brayton PTO systems is crucial for optimizing engine performance and functionality. Proper design ensures the extracted power is efficiently transferred to the auxiliary equipment. This understanding enables engineers to make informed choices in system configuration, thereby maximizing the effectiveness of the Brayton engine and minimizing energy loss. Further, it enables the design of PTO systems tailored for specific applications and constraints, ensuring optimal performance in various scenarios.
2. Auxiliary Equipment
Auxiliary equipment, in the context of a Brayton power take-off (PTO) system, represents a crucial extension of the engine's capabilities. These devices, often compressors, pumps, or generators, rely on the rotational energy extracted via the PTO to function. The connection is causal: the Brayton engine's output powers the auxiliary equipment. Without a functioning PTO, the auxiliary equipment cannot operate. This interdependence underscores the significance of auxiliary equipment as a component of a complete Brayton PTO system.
Real-world applications highlight the practical importance of this understanding. In a gas turbine power plant, a PTO-driven compressor might increase the pressure and density of the incoming air, boosting the engine's overall efficiency. Similarly, a PTO-driven generator converts the engine's rotational energy into electrical power, expanding the plant's output and capabilities. In a mobile power generation context, a PTO system might drive an on-site water pump, enabling the system to provide water for cooling or other essential tasks. These diverse applications showcase how auxiliary equipment enhances the utility and effectiveness of a Brayton engine, transforming its function from a singular power source to a multifaceted energy hub.
In essence, the connection between auxiliary equipment and a Brayton PTO system reveals a fundamental principle of energy conversion and distribution. Careful consideration of the specific auxiliary equipment needs and the engine's output capacity is paramount for optimal system design. This integrated approach ensures efficient energy utilization and enables the targeted application of the Brayton engine's power to diverse tasks. Challenges in this area might include optimizing the power transfer between the engine and the auxiliary equipment to minimize energy loss. Furthermore, the selection of appropriate auxiliary equipment based on the specific application and the constraints of the Brayton PTO system is critical to achieving optimal performance.
3. Engine Output
Engine output is a fundamental factor in the operation of a Brayton power take-off (PTO) system. The amount of power available for extraction through the PTO is directly linked to the engine's output. A high-output engine provides a greater capacity for driving auxiliary equipment. Conversely, a low-output engine limits the PTO's ability to supply the needed power to external devices. This relationship is crucial because it dictates the system's overall performance and the range of tasks it can handle.
Real-world examples illustrate this connection. In a gas turbine power plant, a Brayton engine with substantial output can drive multiple generators and compressors simultaneously. This high output supports the plant's required electrical production and the essential air compression process. Conversely, a small-output engine might only be suitable for smaller-scale applications, like powering specialized equipment in remote locations. This illustrates how engine output acts as a crucial design parameter, influencing the suitability of a Brayton PTO system for particular applications. Factors such as the engine's rotational speed, torque, and efficiency all contribute to the overall output and, consequently, the capabilities of the connected PTO system. A higher-output engine with robust efficiency enables a wider range of auxiliary equipment and increased operating capacity, compared to one with lower output.
Understanding the relationship between engine output and a Brayton PTO system is vital for effective engineering design and operational planning. Adequate engine output is essential for achieving desired performance in various applications. Engine output limitations might necessitate modifications to the PTO system design or the choice of auxiliary equipment, affecting the overall system cost-effectiveness and efficiency. Furthermore, accurate predictions of engine output are crucial for anticipating system limitations, thereby enabling proactive maintenance strategies and maximizing the lifespan of the Brayton engine and its associated PTO system. This critical linkage highlights the interdependencies between engine characteristics and the successful implementation of a functional Brayton PTO.
4. System Design
System design plays a critical role in the effectiveness of a Brayton power take-off (PTO) system. The design dictates how power is extracted from the Brayton engine and delivered to auxiliary equipment. A well-designed system ensures efficient power transfer, minimizing energy losses and maximizing the engine's overall output. Conversely, a poorly designed system can lead to significant power loss, reduced efficiency, and potential damage to both the engine and the auxiliary equipment. Robust design considerations are paramount for optimal performance and longevity.
Factors integral to a successful system design include the precise location and configuration of the PTO components, the selection of appropriate materials withstanding the operating conditions, and the implementation of safeguards to prevent overloading or damage. For example, in a gas turbine power plant, a correctly designed PTO system allows precise power extraction from the engine's rotating components for powering compressors and generators. This design must accommodate varying operating conditions, including fluctuating engine speeds and loads, ensuring the system's reliability. A poorly designed PTO, on the other hand, might suffer from premature wear or damage from excessive stress, resulting in reduced efficiency, unexpected downtime, and increased maintenance costs. Moreover, the selection of appropriate couplings and bearings is crucial to maintain smooth power transmission and prevent excessive vibration. Considerations such as lubrication systems and cooling mechanisms are equally vital in maintaining optimal performance and extending the system's operational lifespan.
In summary, system design is not merely a technical aspect of a Brayton PTO but a foundational element impacting the overall efficiency, reliability, and longevity of the entire system. Proper design translates to reduced operational costs, minimized downtime, and enhanced performance under various operating conditions. A deep understanding of system design principles is essential for engineers and operators to ensure a high-performing and durable Brayton PTO system, facilitating optimal utilization of the engine's power for diverse applications. Challenges in this area often stem from accommodating the varied demands of different applications and ensuring the design accounts for future operational needs. This highlights the ongoing importance of research and development in refining and enhancing Brayton PTO system designs.
5. Efficiency Gains
Efficiency gains associated with Brayton power take-off (PTO) systems stem from the optimized extraction and utilization of energy. A well-designed PTO system minimizes energy loss, thereby increasing the overall efficiency of the Brayton engine. This optimization is crucial for applications where maximizing output while minimizing waste is paramount.
- Reduced Transmission Losses
Optimized power transfer mechanisms in the PTO system directly affect overall efficiency. By minimizing friction and other forms of resistance during power transfer from the engine to auxiliary equipment, efficiency gains are realized. For instance, employing advanced couplings, bearings, and seals in the PTO design reduces energy lost as heat or friction. This results in more of the engine's output being available for work by the auxiliary equipment.
- Improved Component Integration
Effective integration of components in a Brayton PTO system can dramatically enhance efficiency. A well-designed layout minimizes parasitic losses by positioning components for optimal energy flow. Precisely aligned gears and pulleys in the PTO reduce friction and improve power transmission efficiency. Improved component integration minimizes energy lost due to inefficiencies within the PTO itself.
- Optimized Engine Operation
A properly designed PTO system often facilitates optimized engine operation. By allowing the engine to operate at peak efficiency and without the strain of driving unnecessary equipment, the PTO contributes to overall system efficiency. This optimized operation reduces the engine's energy consumption and maximizes its output for the intended purpose, thus improving system efficiency. For instance, a PTO enables a Brayton engine to focus on its primary function, such as power generation, leading to a more efficient energy conversion process.
- Improved Auxiliary Equipment Performance
A well-engineered PTO can positively impact the performance of connected auxiliary equipment. A reliable and efficient power delivery system improves the operational efficiency of the connected pumps, compressors, or generators. By ensuring a consistent and reliable power supply, the PTO system enables the auxiliary equipment to operate at peak efficiency, further enhancing the overall efficiency of the entire system.
In conclusion, efficiency gains achieved through optimized Brayton PTO systems are a direct result of minimizing energy loss at various points within the system. The improved integration of components, reduced transmission losses, and optimized engine and auxiliary equipment performance collectively translate to increased efficiency. These gains are especially critical for applications requiring high output with minimal energy waste, such as in power generation or industrial settings.
6. Reduced Emissions
Reduced emissions are a significant consideration in the context of Brayton power take-off (PTO) systems. The relationship hinges on the efficiency of the overall energy conversion process. A highly efficient Brayton cycle, facilitated by a well-designed PTO, leads to lower emissions per unit of output. This efficiency translates directly to reduced greenhouse gas and other pollutant emissions. A PTO system that minimizes energy loss during power transfer enhances the overall efficiency of the Brayton cycle, resulting in a more sustainable energy generation method.
Practical examples illustrate this connection. In power plants, a sophisticated PTO system driving generators can enhance overall plant efficiency by minimizing parasitic losses. Reduced energy loss throughout the system directly correlates with decreased emissions. In industrial settings, a well-engineered Brayton PTO powering compressors or pumps contributes to efficiency gains, ultimately resulting in lower emission outputs compared to systems with higher energy waste. This principle extends to various applications, from portable power generation for remote locations to stationary power plants within urban centers. Careful engineering in the design and operation of the PTO directly impacts the environmental footprint of the entire system.
In summary, the connection between reduced emissions and Brayton PTO systems is fundamentally linked to efficiency. Minimizing energy loss through careful PTO design directly contributes to a smaller environmental impact. Improved efficiency in power conversion reduces the generation of harmful byproducts. Understanding this relationship is critical for advancing sustainable energy solutions. Challenges remain in optimizing PTO design for specific application needs while maintaining high efficiency and minimizing operational costs. Further research into material science and advanced control systems holds promise for achieving even greater reductions in emissions for diverse Brayton engine applications.
7. Application Flexibility
Application flexibility, a critical characteristic of Brayton power take-off (PTO) systems, underscores the adaptability and versatility of these systems across diverse applications. This adaptability is achieved through careful engineering and design choices, enabling a single Brayton engine to power a broad spectrum of auxiliary equipment. Exploring the facets of this flexibility provides insight into the wide-ranging utility of Brayton PTOs.
- Adaptability to Varied Equipment Loads
Brayton PTO systems exhibit flexibility in handling varying loads. This is particularly crucial in applications demanding fluctuating power requirements, such as mobile power generation. For instance, a PTO system powering a generator in a remote site may require significantly different power outputs compared to driving a compressor in an industrial setting. The PTO's design capabilities enable the system to adapt to these different load demands, without compromising overall efficiency.
- Compatibility with Diverse Auxiliary Devices
The suitability of a Brayton PTO often hinges on its compatibility with a range of auxiliary devices. Different applications necessitate varied equipment interfaces and power transmission protocols. A well-designed PTO can facilitate connections with various types of compressors, pumps, or generators, providing adaptability to different industrial and mobile applications. The engineering of the PTO system dictates the specific auxiliary equipment compatible with the system.
- Scalability and Modular Design
Scalability is a key feature of a flexible Brayton PTO system. The modular design of the system allows for potential expansion of functionalities and power outputs. This adaptability is crucial for meeting future needs, including those arising from expanding industrial processes or energy production demands in mobile settings. The adaptability in scaling PTO systems is facilitated by careful engineering design that allows for incremental additions of components or power outputs.
- Integration with Existing Infrastructure
Flexibility in a Brayton PTO also encompasses its integration with existing infrastructure. A modular and adaptable system design ensures it can be readily incorporated into existing industrial processes without significant disruptions. This compatibility is critical for integrating new power generation systems into existing industrial sites without requiring extensive renovations or overhauls. The design ensures the system can seamlessly adapt to existing infrastructure and equipment.
In essence, application flexibility in Brayton PTO systems stems from the careful engineering design choices that facilitate adaptability across diverse auxiliary equipment, load requirements, and existing infrastructure. This feature, crucial for adaptability and broad applicability, underscores the importance of well-engineered PTO systems for versatile deployment in various industrial and mobile power generation contexts. This multifaceted adaptability is critical for the broader adoption and practical application of Brayton engine technology.
Frequently Asked Questions about Brayton Power Take-Off (PTO) Systems
This section addresses common inquiries regarding Brayton power take-off (PTO) systems, providing concise and informative answers. These questions often arise from a desire to understand the technical aspects, capabilities, and applications of this technology.
Question 1: What distinguishes a Brayton PTO system from other PTO systems?
A Brayton PTO system is specifically designed for use with Brayton cycle engines. Key differences often lie in the specific operating parameters, such as temperature ranges and rotational speeds, which directly influence component selection and design. The unique thermal characteristics and dynamic operational requirements of Brayton engines shape the design considerations for a functional PTO system. Consequently, a Brayton PTO system is optimized for the high-temperature and high-speed characteristics typical of Brayton engines.
Question 2: What are the key performance metrics for evaluating a Brayton PTO system?
Key performance metrics encompass efficiency, power output, operational temperature limits, and reliability. The efficiency of a Brayton PTO system is assessed by measuring the ratio of power delivered to the auxiliary equipment to the power extracted from the engine. Power output is evaluated by measuring the maximum torque and speed at which the PTO can deliver power. Thermal limits, crucial for high-temperature applications, are a critical design consideration. Lastly, reliability factors include the PTO's ability to consistently deliver expected performance over prolonged operation cycles and resistance to damage during operational stresses.
Question 3: What are the typical applications for a Brayton PTO system?
Brayton PTO systems find application in diverse settings requiring high power density and thermal resilience. Power generation, particularly in mobile and remote locations, represents a significant application area. Industrial applications involving compressors or pumps in high-temperature environments are also common. Furthermore, specialized off-road vehicles, particularly those employing high-power energy storage systems, represent a niche application area.
Question 4: What are the potential maintenance considerations for a Brayton PTO?
Maintenance considerations are crucial for ensuring the operational longevity and reliability of a Brayton PTO. Specific components, such as bearings and seals, require regular inspections and lubrication due to their high-temperature and high-speed operation. Regular monitoring of system parameters, including temperature and pressure, is vital. Proper maintenance protocols and schedules are essential to mitigate potential failures, reduce downtime, and maintain the PTO's operational efficiency. Specialized expertise in high-temperature components and lubrication procedures is often needed.
Question 5: What are the long-term operational costs associated with a Brayton PTO system?
Long-term operational costs encompass maintenance, spare parts, and potential downtime. The high operating temperatures and potential for high-speed components can introduce higher maintenance costs compared to lower-temperature systems. The system's complexity and use of specialized materials contribute to potential spare parts costs. Proactive maintenance strategies and efficient operation minimize downtime and associated costs. Accurate cost estimates require a detailed analysis of specific application needs and operational conditions.
Understanding these frequently asked questions provides crucial context for evaluating the suitability and practicality of a Brayton PTO system within specific application scenarios. These systems represent a sophisticated technological solution with unique characteristics.
Transitioning now to a comparative analysis of different PTO technologies within the realm of energy conversion.
Conclusion
This exploration of Brayton power take-off (PTO) systems reveals a complex interplay of engineering considerations. The systems' effectiveness hinges on meticulous design choices, encompassing optimal power extraction methods, compatible auxiliary equipment, and efficient energy conversion. Key factors, such as engine output, system design, and application flexibility, are crucial determinants of the overall performance and suitability for diverse operational environments. The potential for enhanced efficiency and reduced emissions underscores the systems' importance in modern energy production and industrial applications. Careful consideration of these factors allows for optimized system design tailored to specific requirements.
Moving forward, research and development in materials science, advanced control systems, and innovative design strategies are vital for further optimizing Brayton PTO systems. The ongoing pursuit of greater efficiency and reduced environmental impact will shape the future trajectory of these systems. Further advancements in these technologies are likely to lead to broader applications and expanded use cases across various sectors, from power generation to industrial processes. The continued development of these systems is crucial to address growing energy demands and the need for sustainable solutions.
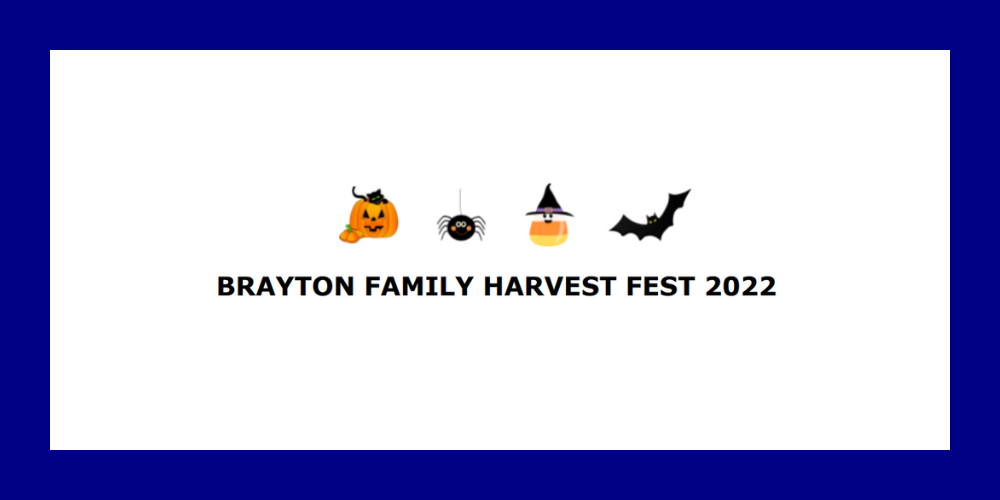

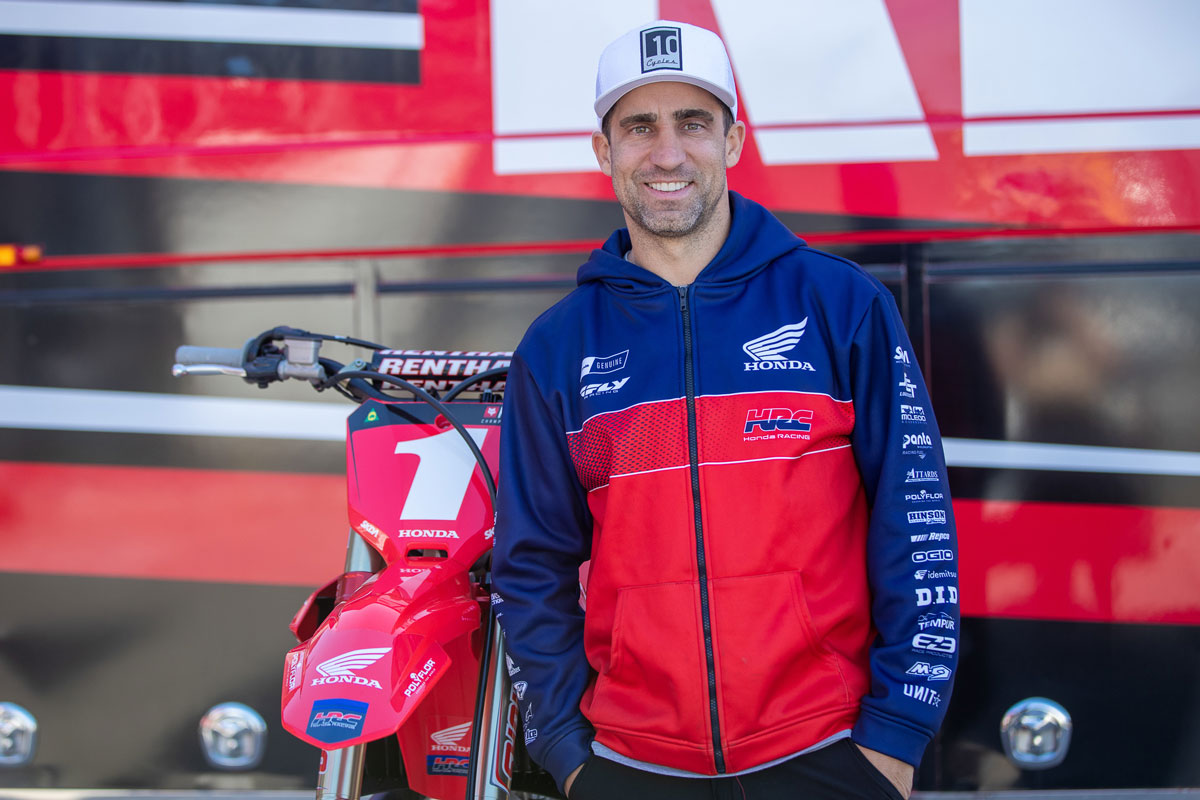
Detail Author:
- Name : Mrs. Kathryne Parisian
- Username : lauryn.hahn
- Email : davis.earlene@weber.biz
- Birthdate : 1991-09-20
- Address : 566 Era Trail New Jaidamouth, AL 23466
- Phone : 458.810.0082
- Company : Erdman, Durgan and Pollich
- Job : Legal Secretary
- Bio : Perspiciatis reiciendis dolorum natus natus sed a. Aut sapiente molestiae distinctio dolorem necessitatibus sint architecto. Recusandae neque qui unde nam ut nemo iusto.
Socials
facebook:
- url : https://facebook.com/jayne_schmidt
- username : jayne_schmidt
- bio : Animi consequatur impedit voluptatem porro.
- followers : 3839
- following : 2230
tiktok:
- url : https://tiktok.com/@jayne_schmidt
- username : jayne_schmidt
- bio : Dolorem dolores et blanditiis dignissimos qui officia magni.
- followers : 3102
- following : 1101
twitter:
- url : https://twitter.com/jayne_official
- username : jayne_official
- bio : Ea corporis vero qui earum perferendis. Qui officiis ut alias ut. Quos non maiores et. Temporibus qui libero expedita molestias praesentium est id.
- followers : 5933
- following : 2229
instagram:
- url : https://instagram.com/jayne_schmidt
- username : jayne_schmidt
- bio : Eveniet quam enim est culpa dolor. Illum qui autem pariatur unde.
- followers : 848
- following : 2159