What is the significance of a specific operational efficiency enhancement? A critical approach to optimizing performance yields considerable return.
This specific operational improvement strategy focuses on streamlining processes and minimizing waste to boost overall productivity. It's a comprehensive approach that identifies bottlenecks, eliminates redundancies, and enhances resource allocation. For example, if a manufacturing plant experiences delays in material delivery, analyzing the logistics and implementing solutions to expedite the process would be a component of this type of strategy. The underlying principle is to fine-tune each stage of an operation to achieve peak efficiency.
Such improvements are vital in various industries, particularly those characterized by intense competition or rapidly evolving markets. Effective implementation of this type of operational strategy can increase output while simultaneously decreasing costs. The benefits extend beyond immediate financial gains, fostering enhanced productivity, improved employee morale, and greater adaptability to changing market conditions. Historically, such strategic efficiency improvements have driven innovation and economic growth, helping organizations gain competitive advantage and maintain a sustainable market presence.
The specific methodologies and details of such initiatives will vary based on the unique characteristics of each operation. Further exploration into the details of specific operational contexts will allow for a more detailed understanding of practical implementation.
Operational Efficiency Enhancement (OEE) Delta
Analyzing operational efficiency enhancements requires a focused examination of key components. Quantifying improvements, and understanding the underlying mechanisms of change, is critical for successful implementation.
- Process Optimization
- Resource Allocation
- Waste Reduction
- Productivity Gains
- Cost Savings
- Performance Metrics
- Data Analysis
These key aspects form a cohesive framework for evaluating the impact of operational efficiency initiatives. For instance, optimizing a process (Process Optimization) can lead to enhanced resource allocation (Resource Allocation), while streamlining workflows (Waste Reduction) often yields significant productivity gains (Productivity Gains). Tracking performance metrics (Performance Metrics) through rigorous data analysis (Data Analysis) reveals the extent of cost savings (Cost Savings). A comprehensive approach that considers all these aspects leads to a more robust and measurable evaluation of the effectiveness of operational changes.
1. Process Optimization
Process optimization is a fundamental component of any strategy aimed at increasing operational efficiency. It involves systematically analyzing existing procedures, identifying bottlenecks and inefficiencies, and implementing changes to enhance effectiveness and productivity. A well-defined optimization approach often directly correlates to gains in operational efficiency. Consider a manufacturing facility struggling with production delays due to material handling bottlenecks. Through process optimization, redesigned workflows, optimized material flow, and the implementation of automated systems can streamline the process, reducing delays and increasing overall output, thus improving OEE (operational efficiency enhancement). Another example is a customer service department experiencing high call abandonment rates. Process optimization, such as re-engineering call routing protocols and training staff to handle common queries efficiently, can lead to significant improvements in customer satisfaction and reduce operational costs.
The importance of process optimization as a driver of OEE cannot be overstated. It's not merely about improving a single process; it's about creating a culture of continuous improvement. This involves identifying and addressing potential problems proactively, which includes utilizing data-driven insights to identify areas needing attention. For example, analyzing historical data to determine patterns and trends in customer complaints can guide improvements in service protocols. By optimizing processes, organizations can effectively utilize resources, reduce waste, and improve output levels. The broader benefits extend to improved employee morale and increased competitiveness in the market.
In summary, process optimization is inextricably linked to achieving higher operational efficiency. By systematically scrutinizing existing processes, organizations can identify and eliminate inefficiencies, leading to optimized workflows and increased output. A focus on continuous process improvement, aided by data analysis and strategic interventions, is vital for any organization seeking to enhance operational effectiveness and achieve a sustainable competitive edge.
2. Resource Allocation
Optimal resource allocation is a crucial component in achieving enhanced operational efficiency. Effective allocation ensures resourceshuman, financial, materialare directed toward activities generating the highest possible return. A misallocation of resources can lead to wasted efforts, decreased output, and ultimately, reduced overall operational efficiency. Understanding the connection between resource allocation and operational efficiency enhancement (OEE) is critical for organizations seeking to maximize performance and competitiveness.
Consider a manufacturing plant. If skilled labor is dedicated to tasks requiring minimal expertise, or if critical materials are insufficiently supplied to key production lines, the outcome will be suboptimal production. Conversely, a well-structured allocation of resourcesallocating skilled workers to complex tasks, ensuring sufficient raw materials and equipment maintenancewill lead to efficient production output and increased OEE. Similarly, in a customer service department, an allocation of resources that emphasizes training and technological support for frontline agents (instead of merely increasing staffing levels indiscriminately) can significantly increase efficiency and customer satisfaction. Resource allocation decisions, therefore, directly impact the overall performance of operations.
The importance of strategic resource allocation extends beyond optimizing immediate operational tasks. A robust understanding of resource allocation and its connection to OEE allows for proactive planning and adaptation to evolving market conditions. By prioritizing resources towards activities with the highest return, organizations can not only improve current operational efficiency but also position themselves for future growth and success. Successfully executing the allocation of resources is fundamentally linked to a strong understanding of the processes themselves. Poor allocation of resources is rarely a stand-alone issueit is often a symptom of deeper problems within the organization's strategic planning. Therefore, effective resource allocation demands comprehensive analysis of operational processes, a realistic evaluation of resource needs, and continuous monitoring and adaptation to ensure optimal results.
3. Waste Reduction
Waste reduction is intrinsically linked to operational efficiency enhancement (OEE). Minimizing waste in all its formsmaterial, time, effort, or resourcesdirectly contributes to improved OEE. This connection stems from the fundamental principle that wasted resources translate to reduced output and increased costs. Identifying and eliminating waste becomes a crucial component for maximizing productivity and minimizing expenses. For instance, a manufacturing plant experiencing high scrap rates due to faulty machinery demonstrates how waste reduction can be crucial to improved efficiency. Reducing scrap through preventative maintenance and quality control improvements can translate directly to increased output, decreased costs, and enhanced OEE.
The practical significance of this understanding extends across diverse sectors. In a service industry, for example, redundant steps in a customer service process represent a type of waste. Eliminating these redundancies through streamlined procedures, improved communication protocols, and the judicious use of technology can significantly reduce wait times, increase customer satisfaction, and ultimately, enhance operational efficiency. Real-world examples abound; retail businesses that minimize overstocking by optimizing inventory management, or healthcare facilities that reduce medical errors through standardized protocols, exemplify the positive impact of waste reduction on operational efficiency. In each instance, reducing waste equates to maximizing the productive use of resources.
Recognizing the interconnectedness of waste reduction and OEE is critical for organizational success. While challenges like entrenched processes or resistance to change may impede waste reduction efforts, a thorough understanding of the positive impact of such initiatives can encourage adoption. By embracing a culture of continuous improvement and actively seeking opportunities to reduce waste, organizations can significantly boost their operational efficiency. The core takeaway is that proactive waste reduction is not merely a cost-saving measure; it's a strategic imperative for any organization aiming to enhance performance and competitiveness in today's dynamic market.
4. Productivity Gains
Productivity gains represent a direct outcome of effective operational efficiency enhancements. Quantifiable improvements in output per unit of input are fundamental to measuring the success of operational changes. These gains are not merely desirable; they are essential for sustained competitiveness and profitability. Analyzing the components driving these gains provides valuable insight into the overall impact of optimization initiatives.
- Improved Process Flow
Streamlined processes, eliminating bottlenecks and redundancies, directly contribute to productivity gains. Consider a manufacturing line where a redesigned workflow eliminated a material handling bottleneck. Reduced delays in production translated to a noticeable increase in output, highlighting the connection between process improvement and productivity gains. Optimized workflows increase efficiency, leading to higher output without additional resource expenditure.
- Enhanced Resource Utilization
Efficient allocation of resourceshuman, financial, materialis paramount to productivity gains. Allocating skilled labor to more complex tasks or implementing technology solutions to optimize resource utilization can significantly impact productivity. For instance, implementing automated inventory management systems in a warehouse can reduce the time spent on manual tasks, freeing up personnel for more valuable activities, and increase overall output.
- Reduced Waste and Downtime
Minimizing waste, both in terms of materials and time, is directly linked to productivity gains. Strategies to reduce waste, such as preventative maintenance of equipment and improved quality control, result in reduced downtime and increased operational output. Preventing equipment failures and minimizing rework directly contribute to increased productivity by maintaining consistent production cycles. In short, reduction in waste translates to higher productivity.
- Increased Employee Efficiency
Investing in employee training, skill development, and ergonomic workspaces can dramatically improve employee efficiency. Empowering staff with the tools and knowledge to work effectively reduces errors, speeds up tasks, and improves overall output. This includes ensuring sufficient resources are available to support employees, and creating an environment for them to thrive.
In essence, productivity gains are a composite effect of optimized processes, judicious resource allocation, waste minimization, and empowered employees. These interconnected factors collectively create a positive feedback loop, where enhancements in one area often yield benefits across others. Organizations consistently striving for productivity gains through operational improvements are better positioned to thrive in a dynamic and competitive environment. The success of any operational efficiency enhancement hinges upon recognizing and leveraging these factors to achieve meaningful productivity gains.
5. Cost Savings
Cost savings are a direct and crucial component of operational efficiency enhancement (OEE). Improved efficiency translates directly into reduced operational expenses. This connection arises from the elimination of waste, optimized resource allocation, and increased productivity. A reduction in material waste, for example, decreases direct material costs. Similarly, reduced downtime and fewer errors translate to lower maintenance and labor costs. Optimizing processes often leads to reduced labor hours needed to complete tasks, saving further on operational costs.
Real-world examples illustrate this connection. A manufacturing company streamlining its production line, eliminating bottlenecks, and decreasing material waste directly reduces raw material costs and production time. A healthcare facility implementing efficient scheduling and reduced waiting times decreases staffing costs and increases patient throughput. These examples demonstrate that cost savings are not simply a byproduct of OEE but a demonstrable, quantifiable outcome of effective implementation. The savings can be substantial and impact the bottom line. Quantifying these savings is vital for demonstrating the return on investment of efficiency initiatives.
Understanding the correlation between cost savings and operational efficiency enhancement is critical for organizational decision-making. Management can justify investments in process improvements and technology upgrades by clearly demonstrating the potential for cost reduction. Strategies for achieving cost savings through OEE improvements must be meticulously planned and executed. This understanding also highlights the importance of measuring and tracking cost savings throughout the implementation process. A lack of such tracking can obscure the true impact of OEE and potentially lead to misallocation of resources in future improvements. The link between cost savings and operational efficiency enhancement highlights a fundamental principle: improved efficiency directly impacts profitability, demonstrating the tangible value of OEE initiatives.
6. Performance Metrics
Performance metrics are indispensable for evaluating the effectiveness of operational efficiency enhancement (OEE) initiatives. They provide a quantifiable means to assess the impact of changes, identify areas for improvement, and demonstrate the return on investment. Without robust performance metrics, the success of OEE strategies remains ambiguous and difficult to validate. A clear understanding of relevant metrics is crucial for evaluating the effectiveness of any operational change and determining the extent of improvement.
The selection and application of appropriate performance metrics directly affect the ability to track progress and identify areas needing adjustment. Metrics must be directly aligned with the specific goals of OEE initiatives. For instance, in a manufacturing setting, key performance indicators (KPIs) might include defect rates, production output, cycle times, and equipment uptime. In a customer service environment, metrics might include customer satisfaction scores, average handling times, and resolution rates. In each scenario, chosen metrics must reflect the operational processes and contribute to a clear picture of efficiency improvements.
Effective implementation of OEE necessitates a system for consistently collecting and analyzing performance data. This data informs decisions about resource allocation, process adjustments, and employee training. Consider a retail business aiming to reduce checkout times. By tracking average checkout times, the business can pinpoint bottlenecks, optimize staffing levels, and identify specific procedures requiring improvement. Such consistent monitoring through metrics facilitates a proactive approach to continuous operational improvement. Comprehensive data analysis further enhances the ability to pinpoint performance trends, revealing patterns that may indicate potential issues or suggest opportunities for further optimization. This understanding is pivotal for identifying specific actions to address underperforming areas, leading to sustained efficiency gains.
Ultimately, the incorporation of performance metrics provides a clear pathway for tracking progress, measuring the impact of operational improvements, and ultimately driving sustained operational efficiency. The consistent use of well-defined metrics offers tangible evidence of the success of OEE initiatives, making a compelling case for future improvements and resource allocation. By meticulously tracking and analyzing performance data, organizations can establish a culture of continuous improvement and adapt proactively to changing market demands. This, in turn, positions organizations to thrive in competitive environments.
7. Data Analysis
Data analysis plays a critical role in evaluating and optimizing operational efficiency enhancements (OEE). Comprehensive data analysis is essential for identifying areas requiring improvement, measuring the effectiveness of implemented changes, and ultimately, achieving sustainable improvements. Without a robust data analysis framework, it's challenging to assess the true impact of OEE strategies and ensure resources are allocated effectively.
- Identifying Bottlenecks and Inefficiencies
Data analysis uncovers operational bottlenecks and inefficiencies often hidden within complex processes. Analyzing historical data, such as production cycle times, machine downtime, and error rates, can reveal patterns suggesting bottlenecks in specific steps or processes. For instance, in a manufacturing setting, a consistent increase in rework time within a particular production stage might signal a need for process redesign or equipment maintenance. By identifying these bottlenecks, targeted improvements can be implemented, increasing efficiency.
- Quantifying the Impact of Changes
Data analysis provides a structured method for quantifying the impact of implemented OEE strategies. By comparing performance metrics before and after implementing changes, the effectiveness of interventions can be objectively measured. This comparison allows organizations to understand the degree to which changes affect key metrics like production output, cost reductions, and cycle times. For example, monitoring production output before and after the introduction of a new scheduling system demonstrates the tangible impact of the implemented change.
- Predictive Modeling and Forecasting
Advanced data analysis techniques, including predictive modeling, enable forecasting future operational needs and potential issues. By identifying trends in historical data, organizations can anticipate potential problems, optimize resource allocation, and proactively address challenges before they impact productivity or profitability. A retail company, for example, can use sales data to predict seasonal demand fluctuations and adjust inventory levels accordingly, preventing stockouts or overstocking.
- Monitoring Key Performance Indicators (KPIs)
Data analysis provides the foundation for monitoring key performance indicators (KPIs). Continuously tracking these KPIs provides insights into the ongoing performance of operations. By monitoring metrics like machine utilization rates, defect rates, and cycle times, organizations can rapidly identify variances from the norm and take prompt corrective action. For example, if a decline is observed in equipment uptime, data analysis can pinpoint the cause, whether it's a maintenance issue, a design flaw, or operator error.
In conclusion, data analysis is not just a tool but a fundamental component in the pursuit of operational efficiency enhancements. Effective utilization of data analysis techniques empowers organizations to identify areas for improvement, assess the impact of changes, and proactively address potential issues. This, in turn, leads to more efficient operations, reduced costs, and enhanced overall performance.
Frequently Asked Questions about Operational Efficiency Enhancement (OEE)
This section addresses common inquiries regarding operational efficiency enhancement (OEE). Clear answers to these questions aim to promote a deeper understanding of OEE principles and their application.
Question 1: What is operational efficiency enhancement (OEE)?
Operational efficiency enhancement (OEE) encompasses a set of strategies and techniques aimed at optimizing operational processes. These strategies focus on maximizing output while minimizing waste, improving resource utilization, and enhancing overall productivity. The core objective is to streamline operations, ultimately leading to greater efficiency and profitability.
Question 2: How does OEE impact various industries?
The application of OEE principles is relevant across numerous industries. Manufacturing, service sectors, and logistics can all benefit from improved operational processes. OEE implementation in manufacturing, for instance, can lead to increased production output, reduced material waste, and minimized downtime. In service industries, OEE can boost customer service response times, reduce wait times, and improve overall customer satisfaction.
Question 3: What are the key elements of a successful OEE initiative?
Successful OEE initiatives rely on several critical components. These include a thorough understanding of existing processes, the identification of bottlenecks and inefficiencies, meticulous data analysis to quantify impacts, the implementation of targeted improvements, and ongoing monitoring and evaluation. An effective OEE approach also requires a commitment to continuous improvement.
Question 4: What are the benefits of implementing OEE?
Implementing OEE offers numerous benefits. These include increased productivity, reduced operational costs, enhanced resource utilization, improved quality, and higher profitability. Furthermore, robust OEE strategies lead to a more adaptable and resilient organization capable of responding to dynamic market conditions.
Question 5: How long does it typically take to implement OEE?
The timeframe for implementing OEE initiatives varies based on factors such as the complexity of existing processes, the extent of desired improvements, and the resources dedicated to the project. Some organizations might see initial results relatively quickly, while others may require more time for a complete implementation and to see the full benefits. The key is a phased approach and a commitment to continuous improvement.
These FAQs provide foundational information about OEE. Further exploration of specific applications and case studies will offer a deeper understanding of how OEE principles can be implemented to achieve significant operational improvements.
This concludes the FAQ section. The following section will delve into detailed methods for achieving operational efficiency.
Conclusion
This exploration of operational efficiency enhancement (OEE) has underscored the critical role of strategic optimization in achieving sustainable improvements. Key components such as process optimization, resource allocation, waste reduction, and the analysis of performance metrics are essential for success. Quantifiable gains in productivity and cost savings are direct results of effective OEE implementation. The analysis revealed a strong correlation between these elements and the demonstrable positive impact on organizational performance. The interconnectedness of these factors highlights the importance of a comprehensive approach to operational improvement.
Moving forward, organizations must recognize the ongoing need for continuous improvement. Adopting a data-driven approach, focused on analyzing performance metrics and identifying areas for enhancement, is crucial. The ability to adapt to changing market conditions and technological advancements through proactive OEE strategies is vital for achieving and maintaining a competitive edge. The integration of comprehensive performance metrics and insightful data analysis is essential to ensure the long-term success of any operational efficiency enhancement initiative. A sustained commitment to these principles is paramount for organizational longevity and prosperity in today's dynamic marketplace.

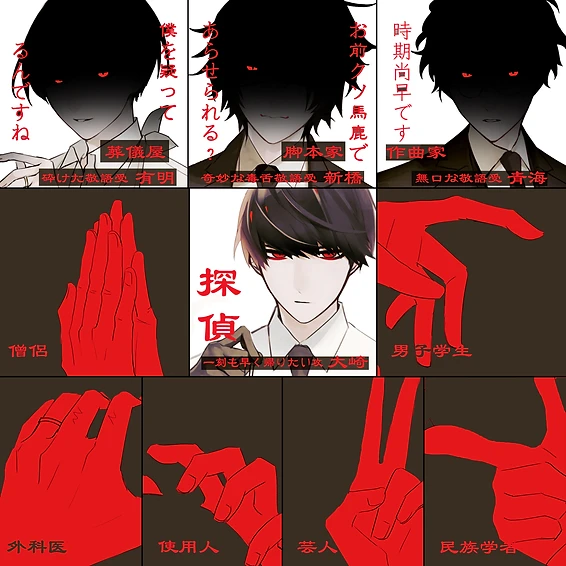

Detail Author:
- Name : Mrs. Kathryne Parisian
- Username : lauryn.hahn
- Email : davis.earlene@weber.biz
- Birthdate : 1991-09-20
- Address : 566 Era Trail New Jaidamouth, AL 23466
- Phone : 458.810.0082
- Company : Erdman, Durgan and Pollich
- Job : Legal Secretary
- Bio : Perspiciatis reiciendis dolorum natus natus sed a. Aut sapiente molestiae distinctio dolorem necessitatibus sint architecto. Recusandae neque qui unde nam ut nemo iusto.
Socials
facebook:
- url : https://facebook.com/jayne_schmidt
- username : jayne_schmidt
- bio : Animi consequatur impedit voluptatem porro.
- followers : 3839
- following : 2230
tiktok:
- url : https://tiktok.com/@jayne_schmidt
- username : jayne_schmidt
- bio : Dolorem dolores et blanditiis dignissimos qui officia magni.
- followers : 3102
- following : 1101
twitter:
- url : https://twitter.com/jayne_official
- username : jayne_official
- bio : Ea corporis vero qui earum perferendis. Qui officiis ut alias ut. Quos non maiores et. Temporibus qui libero expedita molestias praesentium est id.
- followers : 5933
- following : 2229
instagram:
- url : https://instagram.com/jayne_schmidt
- username : jayne_schmidt
- bio : Eveniet quam enim est culpa dolor. Illum qui autem pariatur unde.
- followers : 848
- following : 2159