What is the significance of this specialized printing technology? High-performance, specialized printers offer unique capabilities.
Specialized printing technologies often utilize unique methods, materials, or configurations to achieve specific print characteristics. These printers might excel in producing high-resolution graphics, intricate designs, or specialized materials, like medical imaging or industrial prototypes. The precise nature of the print output, and the capabilities needed to achieve it, are crucial in various fields. For example, a printer designed for producing large-format, high-resolution images for architectural blueprints would require different technical specifications compared to a printer used for high-volume, low-cost document printing.
The importance of such specialized printing equipment stems from its application in various fields, such as industry, medicine, and art. High-quality printing allows for the precise reproduction of data, designs, and complex imagery. This precision facilitates critical analyses, accurate visualizations, and detailed documentation. Moreover, specialized printing techniques enable intricate patterns, textures, or materials in manufacturing processes, medical imaging, and artistic expression.
Now let's delve deeper into the specific applications and benefits of such technology, considering the wide range of uses for these advanced printing approaches.
oric printer
Understanding the "oric printer" necessitates exploring its key characteristics. This analysis focuses on essential features that define this specialized printing technology.
- Precision
- Resolution
- Material Handling
- Application Specificity
- Cost
- Maintenance
Precision and high resolution are critical for detailed output, crucial in applications requiring accuracy. Material handling refers to the printer's ability to manage diverse materials, impacting the range of possible applications. Specific applications dictate the necessary functionality and level of cost, while maintenance requirements will vary based on the printer's complexity and the materials used. For instance, a medical imaging printer needs exceptional resolution and material compatibility for image fidelity. Conversely, a high-volume, industrial printer might prioritize cost-effectiveness and consistent output over extremely high resolution.
1. Precision
Precision is a defining characteristic of specialized printing technologies. The inherent need for accuracy in output directly impacts the design and functionality of these systems. High-precision printers, critical in various fields, ensure a degree of accuracy that traditional systems lack. This precision arises from meticulous engineering choices in components like ink jets, print heads, and material handling mechanisms. For example, a medical imaging printer requires extreme precision to render anatomical details accurately. Errors in this precision can compromise diagnoses and treatment plans. Similarly, in industrial applications requiring the reproduction of complex designs, high precision is crucial for maintaining design integrity and ensuring the proper functioning of the final product.
The practical significance of precision in such printers lies in their ability to meet specific output requirements. Precision enables intricate detail reproduction, crucial for tasks like creating high-resolution blueprints, producing microchips with precise circuit patterns, or rendering intricate textures in artistic prints. The ability to faithfully reproduce fine details, in turn, enhances the accuracy, effectiveness, and reliability of the end products.
In conclusion, precision is an indispensable component of specialized printing systems. The demand for accurate and detailed output directly influences the engineering and operational aspects of these advanced technologies. This precision translates to higher quality products and improved accuracy in various applications, from medical diagnostics to industrial manufacturing and art reproduction. Understanding this crucial connection between precision and specialized printers is fundamental for appreciating their capabilities and benefits.
2. Resolution
Resolution, in the context of specialized printing technologies, signifies the level of detail a printer can reproduce. A high resolution allows for the accurate representation of fine lines, subtle gradations, and intricate details. This characteristic is paramount for specialized printers, impacting their ability to meet exacting standards in various applications. A critical link exists between resolution and the printer's capabilities, especially in tasks requiring precision and high visual fidelity.
The importance of resolution in specialized printers is evident in diverse applications. In medical imaging, high resolution is essential for accurate diagnoses. Precise representation of anatomical structures allows clinicians to identify anomalies and guide treatment plans. Similarly, in architectural design, high-resolution prints are crucial for visualizing building plans and intricate details. The ability to represent complex geometries accurately is a direct consequence of the printer's resolution capability. In scientific research, high resolution allows researchers to visualize intricate structures or patterns within samples, potentially leading to breakthroughs. For instance, in material science, high-resolution printing allows the detailed observation of microstructures, which in turn guides the development of new materials with targeted properties.
Consequently, understanding the resolution capabilities of a specialized printer is critical for determining its suitability for a particular application. Higher resolution often translates to increased cost and complexity in the printer's design and operation. This necessitates careful consideration of the specific application needs and the trade-offs between resolution, cost, and overall system performance. The choice of a specialized printer is fundamentally tied to the desired level of resolution and the inherent capabilities needed to achieve it, emphasizing the need for a comprehensive understanding of this aspect for optimal results.
3. Material Handling
Material handling capabilities are integral to the functionality of specialized printing systems. The ability to manage diverse materials directly impacts the printer's range of applications and overall performance. This crucial aspect dictates the printer's suitability for particular tasks and the quality of the resulting output.
- Material Compatibility
The printer must be compatible with a variety of materials, whether inks, papers, films, or specialized substrates. This compatibility dictates the range of possible applications. For example, a printer designed for medical imaging must handle specific film types with high precision and consistency to ensure accurate imaging. Similarly, a printer for industrial applications might need to handle heat-resistant materials or particular polymers to meet the demands of specific production processes. The printer's inherent limitations in material handling will restrict its range of applicability.
- Precision in Handling
Accurate handling is vital for quality output. The process of loading, positioning, and transferring materials must be precise to prevent imperfections or damage. The printers mechanisms for handling materials, such as rollers, vacuum systems, or robotic arms, are crucial. In high-resolution printing, even slight inconsistencies in material handling can result in visibly flawed outputs. The need for precision underscores the complexity of the material-handling systems within such specialized printers.
- Throughput and Speed
The rate at which materials can be processed impacts the printer's overall efficiency. A high-volume production printer requires fast material handling to keep pace with production demands, whereas a printer focused on precision might prioritize the quality of handling over speed. The speed of handling directly correlates with the printer's output capabilities and overall performance metrics.
- Safety and Environmental Considerations
Safety and environmental considerations in material handling are important. Specialized printers may handle hazardous materials, necessitating robust safety protocols and environmentally responsible disposal methods for used materials. Compliance with industry regulations and safety guidelines is essential for the operation of these systems. The operational safety and environmental impact of material handling procedures are essential considerations for the design and implementation of these specialized printers.
In conclusion, material handling within a specialized printing system is not merely an auxiliary function; it is a core component of its effectiveness and applicability. Understanding material compatibility, precision, throughput, and safety factors is essential for choosing and implementing specialized printing solutions for diverse applications. These factors, ultimately, determine the printer's capability to fulfill specific production needs and deliver high-quality output.
4. Application Specificity
The inherent nature of specialized printing technologies, such as the "oric printer," necessitates a strong focus on application-specific design. This is because the optimal performance and utility of these systems are intricately tied to their intended use cases. Understanding how these systems cater to distinct requirements is crucial for evaluating their suitability and overall effectiveness.
- Target Application Needs
Different applications demand unique print characteristics, such as resolution, color gamut, material compatibility, and speed. A printer designed for high-resolution medical imaging will differ significantly from one used for large-format architectural blueprints. Recognizing these distinct needs is fundamental for the design, development, and subsequent success of the specialized printing equipment. The printer's functionality must align precisely with the application's exacting requirements, ensuring accurate and appropriate output. Examples include specialized materials like medical films for imaging, or heat-resistant polymers for industrial prototypes.
- Output Requirements
Specific output requirements drive the choice and configuration of the equipment. High-quality photorealistic images might necessitate specialized ink formulations or print heads designed for high-fidelity rendering. Likewise, high-volume production printing will emphasize speed and durability, while meticulous precision in a scientific application may demand exceptional resolution and accuracy in fine details. These output demands often dictate the optimal printer configuration, including ink types, print mechanisms, and operational parameters. For example, a printer required for intricate circuit patterns will necessitate particular resolution and materials compared to one designed for high-quality color posters.
- Performance Metrics
Measuring and comparing performance under specific workloads is crucial in evaluating a printer's suitability. Metrics like resolution, print speed, and material compatibility are evaluated within the target application. Analysis using standard test procedures and performance benchmarks within an appropriate context allow for the systematic assessment of the equipment's performance within real-world use cases. For instance, comparing a printers printing speed for large-scale graphics on architectural blueprints versus its ability to produce high-resolution images for medical imaging will highlight differing performance aspects. The relevance of different performance parameters varies according to the specific application.
- Integration with Workflow
Integration with pre-existing workflows is critical. A printer's design should facilitate its seamless incorporation into existing production processes. Its interface, connectivity options, and operational protocols should align with the procedures already in place to eliminate delays or complications. The degree of integration greatly affects the practical usability and efficiency of specialized printing solutions. For example, a manufacturing facility's printer must integrate seamlessly with their current production line control systems for optimal operation.
In essence, the "oric printer," or any specialized printing system, is effectively tailored to specific needs. A deep understanding of the target application, output requirements, performance metrics, and workflow integration are critical for its appropriate selection and efficient utilization. Choosing a specialized printing system depends on meticulous analysis of each specific application, ensuring the optimal balance between equipment capabilities and the unique requirements of the task at hand.
5. Cost
The cost of an "oric printer," or any specialized printing system, is a critical factor in its selection and implementation. Cost isn't merely a price tag; it encompasses a range of factors, including initial purchase price, ongoing maintenance expenses, and potential replacement costs over time. The relationship between cost and functionality is complex, often requiring careful evaluation to ensure that the investment aligns with the specific needs of the application. The initial acquisition cost, while significant, is often just a portion of the overall expense, especially when factoring in long-term maintenance and potential future upgrades. For instance, a high-resolution medical imaging printer, while initially expensive, may require frequent maintenance and potentially specialized consumables, increasing the total cost of ownership over its lifespan.
Several factors influence the cost of specialized printing systems. The complexity of the printer's design, the precision of its components, and the materials used in its construction directly impact the initial purchase price. For example, intricate print heads and specialized ink formulations will contribute to higher costs compared to simpler systems. Moreover, the need for specialized maintenance or repair personnel can elevate overall operational expenses. The volume of anticipated print jobs also plays a significant role. Cost optimization involves careful evaluation of these factors alongside anticipated output volume, material types, and the complexity of the print jobs. A facility needing a high-volume, industrial printer may choose a more cost-effective, though less precise, solution over a smaller, high-precision system optimized for specific scientific research.
Understanding the cost implications of specialized printing is crucial for informed decision-making. The total cost of ownership (TCO) should be considered, including not only the initial purchase price but also ongoing maintenance costs, potential consumables, and the cost of downtime if a system malfunctions. Ultimately, the best approach balances the need for high-quality printing with the availability of budgetary resources. This awareness ensures that the investment in specialized printing equipment aligns with the long-term operational needs and financial constraints of the user, ultimately supporting cost-effectiveness, functionality, and quality output across various applications.
6. Maintenance
Maintenance of specialized printing systems, like the "oric printer," is paramount for sustained performance and optimal output. Neglecting preventative measures can lead to costly repairs, decreased efficiency, and compromised print quality. Effective maintenance strategies ensure the longevity of the equipment and its ability to meet demanding application needs.
- Regular Servicing and Calibration
Routine maintenance, including servicing and calibration, is crucial for preventing unexpected breakdowns. This involves inspecting critical components, adjusting settings, and ensuring optimal performance within prescribed intervals. Precise calibration is essential for consistent output quality. Failure to maintain calibration can result in variations in resolution, color accuracy, or print speed, compromising the output's reliability. Examples include checking ink levels and nozzle patterns in inkjet systems or adjusting print head alignment. Ignoring regular servicing can lead to reduced lifespan for the printer and the need for costly replacements.
- Component Replacement and Upgrades
Regular replacement of worn-out components is essential to maintain peak performance and prevent critical failures. This may involve replacing print heads, ink cartridges, or other parts nearing their lifespan. Upgrades to components can enhance performance, such as adopting newer, more efficient ink systems or print heads. Proper component replacement, based on usage and recommended schedules, ensures optimal functionality and avoids potential output errors. Careful consideration of replacement parts is critical to maintain compatibility with the printer's existing design and operational parameters.
- Environmental Control and Operating Conditions
Maintaining appropriate environmental conditions is essential for optimal printer performance and longevity. Factors like temperature, humidity, and dust levels directly affect the printer's internal mechanisms and the quality of the print output. An excessively humid environment might lead to ink clogging or print head issues, while temperature fluctuations can cause damage to components. Environmental control measures, including temperature regulation and air filtration, are critical for maintaining consistent performance and reducing downtime. Failure to address environmental factors can lead to costly repairs or necessitate frequent replacements of parts.
- Data Backup and Logging
Implementing a robust data backup and logging system is essential for tracking maintenance history and addressing potential issues proactively. Maintaining detailed records of servicing, component replacements, and calibration adjustments facilitates troubleshooting and preventive maintenance planning. This data allows for analysis of usage patterns, identifying potential wear points or areas requiring prioritized attention. This proactive approach can help anticipate and avoid problems. Detailed maintenance records can facilitate efficient repair and prevent costly system downtime.
Effective maintenance practices, encompassing routine servicing, component upgrades, and environmental control, are crucial for the long-term viability of specialized printing systems like the "oric printer." A proactive maintenance strategy minimizes downtime, ensures consistent print quality, and maximizes the equipment's operational lifespan, ultimately reducing the total cost of ownership. Carefully documented maintenance history is invaluable for both immediate troubleshooting and long-term performance prediction.
Frequently Asked Questions (oric Printer)
This section addresses common questions regarding the oric printer, providing concise and informative answers to clarify key aspects of this specialized technology.
Question 1: What are the primary applications of the oric printer?
The oric printer is designed for specific applications demanding high precision and specialized output. These applications often include, but are not limited to, medical imaging, scientific research, high-resolution graphic arts, and industrial prototyping, where detailed accuracy and material handling capabilities are critical.
Question 2: What distinguishes the oric printer from other standard printers?
The oric printer stands out through its superior resolution, material handling capabilities, and application-specific design. These features allow for the precise reproduction of intricate details and a wider range of materials, which are not possible or practical with standard printers.
Question 3: What factors influence the cost of the oric printer?
The cost of an oric printer is multifaceted. Factors include the complexity of design, the precision of components, specialized materials utilized, and potential need for specific maintenance personnel. These aspects impact both the initial purchase price and the long-term total cost of ownership.
Question 4: How does the oric printer maintain consistent output quality?
Consistent output quality hinges on meticulous maintenance procedures. This includes regular calibration, timely component replacement, and stringent environmental control to manage factors like temperature and humidity. Adequate preventative maintenance is key to ensuring optimal performance and accuracy.
Question 5: What are the critical maintenance considerations for the oric printer?
Regular servicing, precise calibration, and timely replacement of components are fundamental to maintaining optimal oric printer performance. Strict adherence to recommended maintenance schedules and environmental control procedures are also critical for maximizing the lifespan and quality of print output.
In summary, the oric printer's specialized design and capabilities cater to particular application needs. Understanding the application-specific features, the role of meticulous maintenance, and the multifaceted cost structure is crucial for informed decision-making regarding this advanced printing technology.
This concludes the Frequently Asked Questions section. Now let's move on to explore the comprehensive technical specifications and applications of the oric printer in greater detail.
Conclusion
This exploration of the oric printer has illuminated its significance in specialized applications demanding precision and high-resolution output. Key characteristics, including precision, resolution, material handling capabilities, application specificity, cost, and maintenance requirements, were examined. The analysis underscored the intricate balance needed between performance, cost, and sustained functionality within distinct use cases. The oric printer, through its specialized design, addresses specific demands across diverse sectors, highlighting the critical need for tailored solutions to fulfill precise output requirements. The detailed exploration of these characteristics, ranging from complex material management to optimal maintenance strategies, ultimately underscores the specialized design that distinguishes this type of printer from standard models.
The oric printer represents a sophisticated advancement in printing technology. Future developments may focus on further optimizing the intricate balance between cost-effectiveness and high-performance output, while also enhancing user-friendliness and integration within existing workflows. This technology's continued advancement promises to drive progress in various fields, from medical diagnostics to industrial manufacturing and scientific research. Understanding the multifaceted nature of the oric printer, from its initial cost to long-term operational expenses, is vital for informed decision-making in selecting and implementing this advanced printing solution for specific applications. Careful consideration of these elements will lead to the most productive integration into target processes.


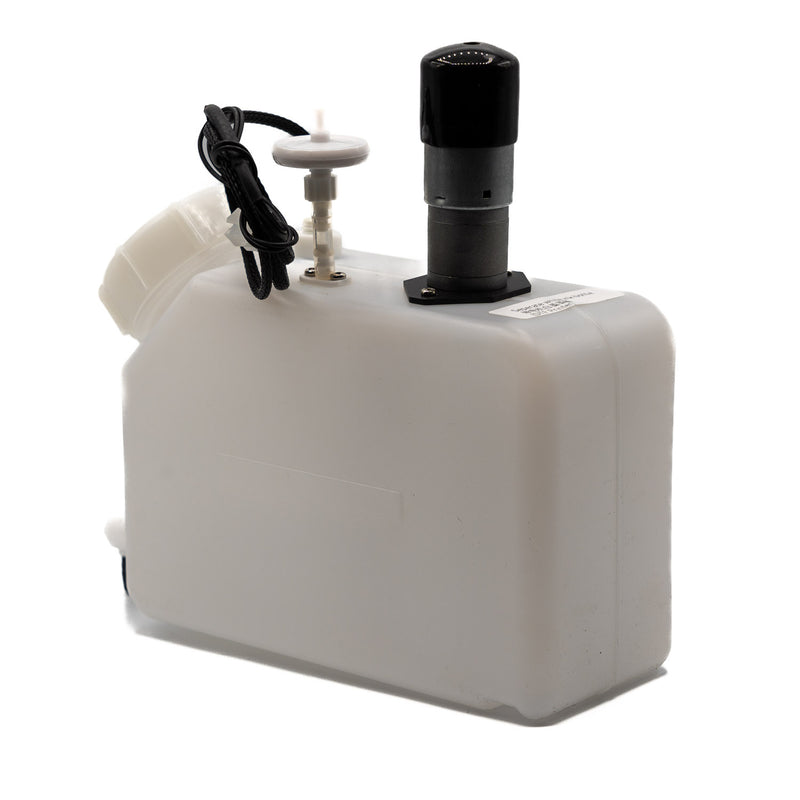
Detail Author:
- Name : Lavon Kautzer III
- Username : okon.gladyce
- Email : wokon@denesik.info
- Birthdate : 1997-03-16
- Address : 193 Aurore Oval Suite 683 East Camrenstad, KY 91177-4664
- Phone : 520-796-9934
- Company : Steuber-Upton
- Job : Government Service Executive
- Bio : Laboriosam minima quis sapiente nam delectus placeat. Repellendus dolore sed quam unde occaecati. Ut dolorem et hic amet molestiae enim qui id.
Socials
tiktok:
- url : https://tiktok.com/@juwan_howe
- username : juwan_howe
- bio : Consequuntur ad ipsum vitae. Sit quis et debitis deserunt.
- followers : 307
- following : 2602
instagram:
- url : https://instagram.com/howe2016
- username : howe2016
- bio : Neque laudantium et dolores est. Sunt qui hic repellat quisquam.
- followers : 3580
- following : 972