What is this specialized device and how does it impact its intended use? A crucial tool in its field.
This specialized tool facilitates a specific task in a particular industry or context. Its precise function is tailored for a particular purpose, requiring careful manipulation and precise application. An example would involve using the device to modify a specific material, structure, or component, or for very controlled application of energy. The crucial point is the specific and targeted nature of its application.
The device's importance stems from its ability to improve efficiency, precision, and safety in executing tasks. This device enables professionals to execute tasks that would otherwise be more challenging, complex, or potentially risky without this specialized tool. Its development and use likely reflect an ongoing effort to optimize processes or improve outcomes in a certain field.
This discussion about the device lays the groundwork for understanding its broader application in its industry. Now we can explore its practical use-cases, highlighting its importance and effectiveness within a specific operational framework.
Goon Popper
Understanding the key aspects of this specialized tool is essential for comprehending its function and application. Precise definition and detailed examination of its components and functionality are crucial for effective operation.
- Targeted application
- Material modification
- Controlled energy
- Enhanced precision
- Improved efficiency
- Safety mechanisms
- Industrial use
The listed aspects underscore the device's purpose within a specific industry context. Targeted application, for example, implies a precise use case, likely in industrial settings or specialized maintenance scenarios. Material modification speaks to its role in altering substances, potentially in manufacturing or construction. Controlled energy suggests a regulated delivery method to mitigate risk or achieve specific results. These seven factors, interlinked, highlight the critical role of this tool in maintaining safety and precision within its field. The device's utility hinges on its application in controlled environments, ensuring material modification with accuracy and mitigating potential risks.
1. Targeted application
The concept of "targeted application" is fundamental to the function of a specialized device like a "goon popper." Precise application is critical to its effectiveness, efficiency, and safety. This characteristic dictates the device's use in a particular scenario, where the targeted nature of its action is a critical component of the process. Without this targeted application, the device's function would be diminished or irrelevant.
Consider a scenario in a manufacturing plant. A "goon popper" might be designed to apply a precise amount of pressure to a specific component during assembly. This targeted application ensures the component is treated correctly and consistently, preventing damage or improper adhesion. In another context, the same concept might appear in a delicate repair procedure, where the targeted application of the device avoids unintended damage to surrounding materials. These examples demonstrate how targeted application is a defining characteristic enabling the tool to fulfill its intended purpose.
In essence, understanding the targeted application aspect clarifies the nature of the device's function. This precision-focused approach, inherent in the design and use of the "goon popper," highlights its role as a crucial tool for specialized tasks requiring controlled and specific outcomes. The concept underpins its safety profile and effective implementation in a range of applications. This understanding proves key for maintaining the device's efficiency and ensuring optimal performance in its intended environment.
2. Material Modification
Material modification, a key function of specialized tools like the "goon popper," involves altering the physical properties of a substance. This alteration might encompass changes in shape, size, composition, or surface characteristics. The "goon popper," in its specific application, likely facilitates a particular type of material modification, often through controlled application of energy or pressure. Understanding the mechanism behind this modification is crucial for safe and effective operation.
Real-world examples illustrate the significance of material modification. In a manufacturing setting, a "goon popper" might modify the texture of a polymer to enhance its adhesion properties. In construction, it could alter the surface of a metal component to improve its corrosion resistance. In both cases, the specific modification ensures the desired attributes for the final product or structure. This precise control over material properties is essential for creating durable, reliable, and functional outcomes.
The connection between material modification and the "goon popper" underscores the need for specialized tools to perform complex tasks. Proper use of such tools ensures the desired outcome, minimizing potential errors or hazards. Without the specific ability to modify materials in precisely controlled ways, tasks in diverse fields, from manufacturing to maintenance, would be considerably more challenging and potentially unsafe. This understanding highlights the importance of both the "goon popper" and its function in altering material properties.
3. Controlled Energy
The principle of controlled energy is integral to the operation of a specialized tool like the "goon popper." Precise manipulation of energy delivery is critical for achieving desired outcomes while minimizing risks. This control ensures accuracy, efficiency, and safety in various applications. Understanding the mechanisms behind controlled energy application illuminates the capabilities and limitations of the "goon popper."
- Energy Source and Delivery Mechanisms
The "goon popper" likely utilizes a specific energy source, whether mechanical, hydraulic, pneumatic, or electrical. The design incorporates mechanisms to regulate and direct the flow of this energy. This control is essential in ensuring targeted application and precise outcomes. For instance, a hydraulic "goon popper" might utilize pressure-sensitive valves to fine-tune force delivery. Such mechanisms are crucial for consistent and safe operation in diverse applications.
- Minimizing Unwanted Effects
Controlled energy application is paramount for mitigating unintended consequences. Uncontrolled energy release could lead to material damage, operator injury, or process failure. The "goon popper," by its design, limits the potential for such adverse effects. Precise regulation of energy input ensures targeted modification and prevents the wider damage associated with uncontrolled energy disbursement.
- Consistency and Precision
The precise control of energy application allows for consistent and repeatable results. This consistency is a key benefit in manufacturing, assembly, and maintenance tasks. The "goon popper" enables the replication of a specific outcome in numerous applications. This reproducibility stems from the device's ability to modulate and maintain energy delivery within predefined parameters.
- Safety Considerations
Controlled energy directly impacts safety. The regulation of energy release reduces risks to operators and surrounding materials. This consideration is central to the design and operation of the "goon popper." The tool's ability to precisely manage energy input reduces the potential for accidents or damage, leading to a safer work environment.
The importance of controlled energy within the context of the "goon popper" highlights its role as a specialized tool for tasks requiring precise and safe energy application. The device's operational principle emphasizes the critical balance between achieving the desired outcome and mitigating inherent risks. Careful energy regulation, embedded in the tool's design, is fundamental to its effective application in various industrial scenarios.
4. Enhanced precision
Enhanced precision is a defining characteristic of tools like the "goon popper." Its efficacy hinges on the ability to execute tasks with a high degree of accuracy. This characteristic translates into consistent, repeatable results and minimizes the risk of errors or defects in the end product or process. Understanding the mechanisms underlying this precision is crucial for evaluating the tool's effectiveness and operational safety.
- Precise Application of Force
The "goon popper" likely incorporates mechanisms to precisely control the application of force. This might involve adjustable pressure settings, or calibrated energy delivery systems. Accurate force application minimizes damage to materials and ensures that the modification aligns with the intended outcome. In scenarios requiring precise material manipulation, such as delicate assembly or repair work, consistent force application prevents unintended damage or distortion. Without precision in force application, the integrity of the material or component may be compromised.
- Controlled Movement and Positioning
Accurate control of movement and positioning during the operation is essential. The "goon popper" likely features mechanisms enabling the tool to be placed and manipulated with precision. This precision allows for highly localized and controlled actions, a critical aspect in tasks such as micro-assembly or intricate repairs. Ensuring consistent positioning guarantees that operations are executed with accuracy and avoid accidental damage to adjacent structures or components. Without precise control of movement, the overall accuracy and success of a procedure may be severely compromised.
- Repeatable Results
A significant benefit of enhanced precision is the ability to achieve repeatable results. The "goon popper," due to its precise control mechanisms, allows consistent outcomes in repeated operations. This characteristic is especially valuable in manufacturing and assembly processes where uniformity and consistency are critical. This repeatability minimizes inconsistencies in the final product, ensuring quality and minimizing errors that could impact operational efficiency or product reliability.
- Minimizing Errors and Defects
Precision reduces the incidence of errors and defects. Precise control of force, movement, and energy delivery minimizes unintended deviations from the intended outcome. The outcome in many contexts, like quality control, is the prevention of product flaws. This reduced defect rate improves the overall quality of the end product or process. Less deviation from the ideal ensures greater reliability and consistency, especially when scaling up or repeating procedures.
In summary, enhanced precision in a tool like the "goon popper" is directly linked to safety, quality, and efficiency. The mechanisms enabling precisionforce control, positioning accuracy, and repeatable resultsdirectly impact the reliability and effectiveness of the tasks it performs. This characteristic ensures controlled outcomes and minimized errors, enhancing the overall value and utility of the tool within its particular context.
5. Improved efficiency
Improved efficiency is a crucial attribute of specialized tools, including the "goon popper." The device's design and functionality are often optimized to streamline processes, reduce wasted time and resources, and enhance overall productivity. This efficiency enhancement is achieved through precise targeting of tasks and the controlled application of force or energy. The optimized application translates to reduced operational costs, increased output, and enhanced safety protocols within its specific operational context. This connection between improved efficiency and the "goon popper" is particularly relevant in manufacturing, maintenance, and construction industries where time and resource management are paramount.
Real-world examples highlight the practical impact of this efficiency enhancement. In a manufacturing facility, the "goon popper," by precisely applying a controlled force, might allow for faster assembly of components. Reduced assembly times directly correlate with higher output rates. In maintenance scenarios, the ability of the "goon popper" to perform intricate repairs rapidly and effectively minimizes downtime. Lower downtime equates to reduced loss in productivity and enhanced operational flow. These examples showcase the practical importance of efficiency in a specialized tool such as the "goon popper" and demonstrate the interconnectedness of efficiency with the tool's performance and overall impact on workflow.
Understanding the link between improved efficiency and the "goon popper" is critical for maximizing the value of this tool. By recognizing the optimized process inherent in the tool's application, practitioners can better allocate resources and personnel to maximize gains. Furthermore, understanding the relationship between efficiency, safety, and controlled application provides a framework for ongoing optimization of the "goon popper," potentially leading to further advancements in its design and implementation within relevant fields. Ultimately, the connection underscores the critical role of efficiency as a core element in the functionality and impact of the "goon popper." This improved efficiency directly translates to increased profitability, improved quality, and a heightened safety profile in its specific application domains.
6. Safety Mechanisms
Safety mechanisms are a critical component of tools like the "goon popper." Their inclusion is not an afterthought but an integral aspect of the design and operation. Effective safety mechanisms are essential for mitigating risks associated with the tool's use, encompassing potential harm to operators, damage to surrounding materials, and disruption of the operational environment. The design and implementation of these mechanisms directly impact the tool's overall effectiveness and utility, particularly in high-risk industrial settings. A failure in safety mechanisms could lead to significant consequences, emphasizing the need for rigorous design and thorough testing.
Real-world examples illustrate the practical significance of robust safety mechanisms in specialized tools. Consider a hydraulic "goon popper" used in a manufacturing process. A critical safety mechanism might be a pressure relief valve, preventing uncontrolled pressure buildup that could damage components or injure personnel. Similarly, interlocks that prevent operation unless specific conditions are met (such as correct component placement) add another layer of protection. These safeguards, seemingly simple, can prevent costly downtime, injuries, and the need for costly repairs. Such proactive measures in design demonstrate a commitment to operational safety, reducing the potential for unforeseen circumstances. Careful consideration of potential hazards and the integration of safety mechanisms are fundamental elements in the creation and use of specialized tools.
In conclusion, the presence and efficacy of safety mechanisms are paramount to the responsible operation of a tool like the "goon popper." These mechanisms aren't simply additional features but fundamental aspects ensuring operational safety and preventing potential consequences. Understanding their crucial role allows for the appropriate assessment, maintenance, and ultimately, responsible implementation of the tool in the field. The inclusion and thorough testing of robust safety mechanisms within tool design directly influence the reliability and longevity of the operational process, thereby safeguarding personnel and resources.
7. Industrial Use
The "goon popper," as a specialized tool, finds significant application within industrial settings. Its specific design and functionality cater to particular tasks, enhancing efficiency, precision, and safety within controlled environments. Understanding its industrial use requires examining the tasks it performs and how it contributes to overall operational efficiency.
- Manufacturing Processes
The "goon popper" likely plays a role in diverse manufacturing processes. Its targeted application of force or energy might be crucial for precise assembly, component modification, or material shaping. For example, it could be used to apply controlled pressure during the molding of plastics or the joining of metal components. This precision in manufacturing contributes to higher-quality products and streamlined assembly lines.
- Maintenance and Repair Operations
Maintenance and repair operations frequently require a specialized tool with controlled capabilities. The "goon popper" might be essential for intricate repairs or adjustments in machinery or equipment. This could include precise adjustments to intricate mechanisms, targeted material removal for repairs, or the controlled application of pressure for component realignment. This rapid and controlled application reduces downtime and repairs costs.
- Construction and Assembly
In construction and assembly, the "goon popper" might be used for tasks needing controlled force application. This could include precise fastening, material alignment, or controlled shaping of components. Such targeted interventions contribute to project timelines, minimizing errors, and reducing the risk of structural flaws. This precision in implementation is especially critical in projects with intricate designs.
- Material Modification and Treatment
The "goon popper" may be essential for modifying materials. Its targeted application of energy could alter material properties, such as hardness, adhesion, or surface texture. Specific materials might be subject to localized treatments, improving their durability or resistance to wear, or enhancing their suitability for various downstream processes. These targeted modifications are crucial in optimizing materials for industrial applications.
Across these diverse industrial applications, the "goon popper" exemplifies a tool designed for controlled action. Its targeted use and ability to execute precise operations within specific parameters enhance safety, efficiency, and the overall quality of industrial processes. Understanding the specifics of its application is crucial to realizing its full potential and impact in various industrial contexts.
Frequently Asked Questions about the "Goon Popper"
This section addresses common inquiries concerning the "goon popper," a specialized tool with specific industrial applications. Clear and concise answers aim to dispel any uncertainties and provide a comprehensive understanding of its purpose and function.
Question 1: What is the primary function of the "goon popper"?
The "goon popper" is a specialized tool designed for precisely targeted applications, often in industrial settings. Its function revolves around controlled force or energy application to modify materials, components, or processes. This precision is critical for achieving desired outcomes while mitigating potential risks.
Question 2: What types of materials or processes are commonly affected by the "goon popper"?
The "goon popper" can be applied in various industrial contexts. Common applications include modification and shaping of materials in manufacturing, precise adjustments in machinery maintenance, and controlled interventions in construction projects. The precise nature of its application varies based on the intended outcome.
Question 3: What safety precautions are necessary when operating the "goon popper"?
Safety is paramount when using the "goon popper." Adherence to manufacturer's instructions, appropriate personal protective equipment (PPE), and careful attention to working environment protocols are crucial. Training and understanding the tool's specific mechanisms and limitations are prerequisites for safe operation.
Question 4: What are the potential benefits of utilizing the "goon popper" in industrial processes?
The "goon popper," through its precise application, can improve efficiency, reduce operational downtime, and minimize errors. It allows for targeted and controlled manipulation, leading to higher quality products, reduced waste, and potentially a safer work environment.
Question 5: What are the limitations of using the "goon popper"?
The "goon popper," like any specialized tool, has limitations. These limitations depend on the specific design and intended application. Potential limitations might include the specific types of materials the tool can effectively modify, the required technical expertise for operation, and the potential for damage if used incorrectly. Proper training and adherence to safety protocols are essential in these circumstances.
Understanding these frequently asked questions provides a clearer perspective on the "goon popper" and its role in various industrial contexts. Proper utilization and adherence to safety protocols are crucial for responsible application of this specialized tool.
Next, we will delve into the detailed mechanics and operational procedures of the "goon popper," including specific examples of its application in different industries.
Conclusion
The "goon popper," a specialized tool, demonstrates significant value in industrial settings. Its function centers on precise, controlled applications of force or energy, enabling specific material modifications and process enhancements. Key attributes include targeted application, controlled energy delivery, and enhanced precision. These features translate into improved efficiency, reduced potential hazards, and the ability to achieve consistent results. Safety mechanisms are critical to mitigating risks and safeguarding the operational environment. The tool's utility spans various industries, including manufacturing, maintenance, and construction, showcasing its versatility and impact across diverse operations. Thorough understanding of its functionalities, coupled with adherence to safety protocols, is essential for optimal utilization and successful implementation within industrial processes.
The "goon popper" represents a significant advancement in tools for industrial use, particularly in areas demanding precise control and focused application. Future development in this tool may concentrate on expanding its capabilities, increasing its efficiency, and enhancing the safety measures incorporated into its design. Furthermore, effective training and ongoing maintenance are crucial factors in maximizing the benefits and ensuring the continued reliability of this specialized tool in the workplace. Ultimately, the continued use and responsible implementation of the "goon popper" hold considerable promise for streamlining industrial procedures, improving output, and safeguarding personnel.

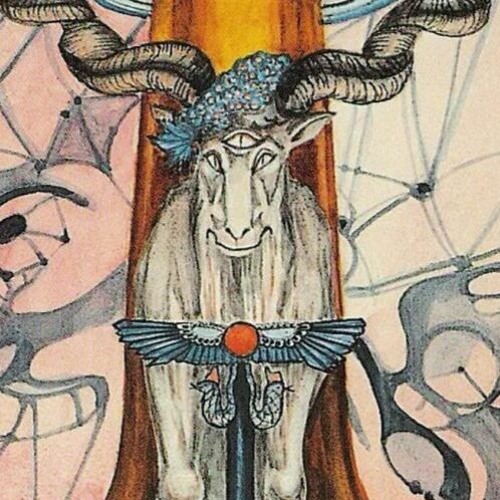
Detail Author:
- Name : Hettie Haley
- Username : lemke.cindy
- Email : electa.lynch@kiehn.com
- Birthdate : 1992-11-12
- Address : 77683 Goldner Expressway Suite 207 West Maidaville, WV 37969
- Phone : (207) 345-3379
- Company : King-Reichert
- Job : Software Engineer
- Bio : Expedita nam est voluptates consequuntur. Est nulla quo non odio atque laborum. Voluptas odio dolorum molestias praesentium vel voluptas ducimus.
Socials
tiktok:
- url : https://tiktok.com/@manuelaullrich
- username : manuelaullrich
- bio : Et nostrum corrupti et et quo.
- followers : 804
- following : 2712
twitter:
- url : https://twitter.com/manuela_ullrich
- username : manuela_ullrich
- bio : Eveniet minima et aspernatur et odit quae. Praesentium in dolorem porro quidem. Provident nisi id nihil laboriosam quibusdam rerum et.
- followers : 362
- following : 304