What are the protective properties of a material capable of withstanding highly corrosive substances? A substance that repels and neutralizes acid effectively has profound implications.
This specialized material, capable of withstanding intense chemical attack, possesses a unique chemical composition. It typically involves a complex interplay of substances designed to resist and counteract corrosive acids. This material's effectiveness stems from its ability to form a protective barrier against the corrosive action of acids. This barrier can manifest as a physical coating or a chemical reaction that neutralizes the acid's destructive potential. Examples might include specific polymers, engineered ceramics, or alloys designed to provide exceptional resistance to acids.
The importance of such a material lies in its capacity to safeguard sensitive equipment or structures from severe environmental degradation or accidental exposure. It is crucial for applications where exposure to aggressive chemical environments is unavoidable. This includes industries such as chemical processing, materials science, and certain forms of manufacturing. In these sectors, the need for durable and dependable protection from acid corrosion is paramount, ensuring equipment longevity and worker safety. Advancements in this area continue to explore new formulations and applications for this type of substance.
Moving forward, we will delve deeper into specific instances where this protective material is employed, outlining its critical role in a range of industrial settings and highlighting its benefits.
Acid Resistance
Understanding the multifaceted nature of acid resistance is crucial for protective materials. This includes chemical composition, structural integrity, and performance in various environments.
- Chemical Composition
- Structural Integrity
- Performance Under Stress
- Durability
- Application Specificity
- Cost-Effectiveness
- Environmental Impact
The effectiveness of acid-resistant materials hinges on a complex interplay of their chemical makeup, their internal structure, and how they perform under different conditions. For instance, a material with a high resistance to concentrated sulfuric acid might not exhibit the same performance with hydrofluoric acid. Cost-effectiveness and environmental impact are also key considerations when choosing a suitable material. Durable materials with high resistance to corrosion form the foundation of industrial equipment, protecting workers and maintaining functionality in high-stress chemical settings.
1. Chemical Composition
The chemical composition of a material directly dictates its ability to resist acid attack. Effective "acid armor," or materials designed to withstand corrosive acids, relies heavily on a specific chemical structure capable of withstanding the chemical reactions initiated by the acid. This involves a careful selection of elements and compounds that can either neutralize the acid's corrosive action or create a protective barrier. For example, certain ceramics, composed of oxides and other elements with strong bonds, possess inherent resistance to a range of acidic substances. Similarly, specific alloys, created through the combination of metals with different properties, might resist acid attack due to the formation of a passive oxide layer.
The choice of chemical components influences the material's resistance to different types and concentrations of acids. A material highly resistant to dilute sulfuric acid may exhibit significantly reduced performance against concentrated hydrofluoric acid. Understanding the specific chemical interactions between the acid and the material is essential for predicting and optimizing the desired level of resistance. This knowledge is critical in developing materials for chemical processing equipment, pipelines handling corrosive fluids, and protective coatings for infrastructure subjected to acidic environments. The selection of the appropriate chemical composition is vital for the practical application and effectiveness of these protective materials.
In conclusion, chemical composition forms the fundamental basis for a material's performance as "acid armor." Understanding the interactions between the acid and the material's chemistry is vital for designing effective protective measures. This knowledge allows for the targeted selection of materials that resist specific corrosive agents, ultimately enabling the successful operation of various applications in challenging environments.
2. Structural Integrity
Structural integrity is paramount in materials designed to withstand acidic environments. A material's ability to resist corrosion and maintain its intended form under chemical attack depends directly on its internal structure. Weaknesses in the material's microstructure, such as defects or voids, can act as initiation points for corrosion, leading to rapid degradation. Conversely, materials with a dense, uniform structure and strong bonding between constituent elements are far more resistant to the detrimental effects of acid. The importance of structural integrity as a defining characteristic of "acid armor" cannot be overstated. This is crucial for ensuring the material's long-term effectiveness in protecting against the corrosive power of acids.
Consider a chemical processing tank lining. A lining with poor structural integrity, exhibiting cracks or porosity, will allow acid to penetrate and corrode the underlying material, leading to leaks and potentially catastrophic failures. Conversely, a lining with a dense, highly crystalline structure, such as a specific ceramic, will resist the corrosive action of the acid, protecting the tank for an extended period. This exemplifies the direct correlation between structural integrity and the material's ability to function as "acid armor." Furthermore, the structural homogeneity of the material is often a determinant of its ability to withstand stress, a vital factor in applications like pipelines exposed to constant pressure and fluctuating temperatures in corrosive environments. Stress can exacerbate any flaws, making structural integrity even more critical in such applications.
In essence, maintaining structural integrity is crucial for any material intended as "acid armor." The material's resistance to acid attack is not solely determined by its chemical composition but also by its microstructure. A material with excellent resistance to acid but poor structural integrity may fail prematurely due to micro-cracks or pitting. Understanding and controlling these structural aspects is essential for developing effective and durable materials capable of withstanding long-term exposure to corrosive environments. This extends beyond material selection to the crucial design considerations of fabrication techniques, ensuring the absence of structural weaknesses and promoting a consistent, strong material structure.
3. Performance Under Stress
The performance of a material designated as "acid armor" is not solely defined by its inherent resistance to acid in a static environment. Crucially, its performance under stressthermal, mechanical, or chemicalsignificantly impacts its efficacy. Elevated temperatures, fluctuating pressures, or repeated exposure to the corrosive substance can induce stresses within the material. These stresses can lead to micro-fractures, diminished resistance to acid attack, and premature failure. The ability of the material to withstand these stresses is as crucial as its intrinsic chemical resistance. Understanding this interplay is vital for applications involving continuous use and dynamic conditions.
Consider a pipeline transporting corrosive chemicals. While the pipeline's material might have high acid resistance at ambient temperature and pressure, prolonged exposure to elevated temperatures, fluctuations in pressure, or even repeated thermal cycles can lead to stress cracking and eventual material degradation. The same principle applies to protective coatings on equipment in a chemical plant. The protective layer's performance under stress, including its adherence to the underlying substrate and resistance to abrasion and impact, is equally critical to its lifespan and effectiveness as "acid armor." Without adequate resistance to these external stresses, the material's resistance to acid itself becomes irrelevant. In these dynamic applications, understanding the material's mechanical and thermal properties, along with its response to the corrosive environment, is paramount.
Consequently, comprehensive assessments of materials intended as "acid armor" must go beyond static resistance tests. Stress-induced degradation pathways must be meticulously analyzed. This includes examining the material's resilience to fatigue, creep, and stress corrosion cracking. Only through a thorough understanding of these performance parameters under diverse stress conditions can reliable and long-lasting protection against acidic environments be guaranteed. The practical implications of this understanding are evident in the design of robust chemical processing equipment, pipelines, and protective linings, ensuring optimized durability and minimizing the risk of catastrophic failure in demanding applications. This knowledge ensures the materials meet the rigorous demands placed on them, translating to improved safety, minimized downtime, and substantial cost savings in the long run.
4. Durability
Durability is a critical component of any material designated as "acid armor." A substance's ability to withstand the corrosive effects of acids over an extended period is paramount. The interplay between material composition, structural integrity, and environmental factors dictates durability. A material might exhibit immediate resistance to a specific acid but succumb to gradual degradation over time. This characteristic is crucial in numerous applications, from chemical processing equipment to protective coatings on infrastructure. Failures stemming from inadequate durability can lead to costly repairs, environmental damage, and safety hazards.
Real-world examples illustrate the significance of durability. Pipelines transporting highly corrosive acids, if made from materials lacking durability, will suffer from pitting, cracking, and eventual rupture. This can lead to environmental contamination and safety concerns, underscoring the importance of material selection that prioritizes prolonged resistance to acid attack. Similarly, protective coatings on industrial tanks must not only repel acids but also withstand repeated exposure, fluctuations in temperature, and potential mechanical stresses. Their durability directly impacts the longevity and operational efficiency of the storage and processing equipment. Insufficient durability in such critical applications can have considerable financial repercussions and necessitate frequent replacements, underscoring the importance of anticipating long-term performance needs when choosing materials.
Understanding the connection between durability and "acid armor" necessitates a multifaceted approach. Materials scientists need to evaluate not just immediate resistance but also the long-term performance under varying conditions. This demands rigorous testing protocols that simulate real-world scenarios, encompassing factors like temperature variations, pressure fluctuations, and repeated exposure to the corrosive substance. The development of advanced testing methods and the use of sophisticated analytical techniques for identifying failure mechanisms are crucial for ensuring that materials meet stringent durability standards. Ultimately, a material's durability as "acid armor" directly impacts its practical application in mitigating corrosion in high-risk environments. This insight underpins the need for a comprehensive and nuanced approach to material selection and testing, guaranteeing prolonged performance and safeguarding critical infrastructure and processes.
5. Application Specificity
The effectiveness of a material designated as "acid armor" is inextricably linked to its application-specific properties. A material demonstrating exceptional resistance to one type of acid or corrosive environment might perform poorly in another. Understanding the precise nature of the applicationincluding the specific acid, concentration, temperature, pressure, and anticipated operational lifespanis crucial for selecting the appropriate material. This tailored approach is essential for maximizing protective capabilities and ensuring long-term functionality.
- Acid Type and Concentration
Different acids exhibit varying degrees of corrosiveness. Hydrochloric acid, for instance, presents a different corrosive challenge compared to sulfuric acid. The concentration of the acid also plays a significant role. A material might exhibit robust resistance to dilute sulfuric acid but fail under the attack of concentrated sulfuric acid. Selection of the "acid armor" must be meticulously aligned with the specific type and concentration of the targeted acid to guarantee optimal performance. This necessitates laboratory testing and rigorous analysis of the material's chemical interaction with the targeted acid under varying concentrations.
- Environmental Conditions
External factors, such as temperature and pressure fluctuations, significantly impact the performance of "acid armor." Elevated temperatures can accelerate corrosive reactions, while extreme pressures can induce stress cracking or other forms of degradation. The interplay between temperature, pressure, and the corrosive medium directly influences the material's durability and lifespan. Properly characterizing the specific environmental conditions encountered during operation is critical for selecting an appropriate material. This often involves simulating relevant operational parameters in laboratory settings.
- Operational Lifespan
The expected duration of operation greatly influences the selection of "acid armor." Materials designed for short-term exposure to acids might not possess the same durability standards required for long-term applications. Components in high-volume, continuous chemical processing operations require materials with exceptional resilience to repeated acid exposure. Predicting the long-term behavior of the material under sustained corrosive exposure and stress conditions is fundamental. This necessitates extensive fatigue testing and simulations to ascertain the material's longevity in the specific application.
- Mechanical Loading
The mechanical stresses experienced by the material are also critical considerations. A material might display excellent acid resistance but fracture under high mechanical stress. Materials subjected to tensile stress, abrasion, or impact during operation must be selected with these considerations in mind. Factors such as the expected load, frequency of exposure, and potential shocks or impacts are vital for proper selection. This necessitates stress testing and evaluating the material's ability to withstand expected mechanical loading.
In conclusion, application specificity is not a secondary consideration but a fundamental principle in selecting "acid armor." By carefully considering acid type, concentration, environmental conditions, operational lifespan, and mechanical loading, decision-makers can ensure the selection of a material that effectively mitigates corrosion and guarantees the longevity and safe operation of equipment in demanding environments. This meticulous approach to application-specific solutions is crucial for maximizing the effectiveness and cost-efficiency of "acid armor." Compromising on any of these parameters can result in unexpected failures and costly replacements.
6. Cost-Effectiveness
The selection and implementation of "acid armor" materials necessitates a careful consideration of cost-effectiveness. Minimizing expenses while maximizing protection is a critical objective. This encompasses the initial material cost, installation expenses, potential maintenance requirements, and the long-term operational efficiency of the protected structure or equipment. The optimal material choice balances these factors to provide the best value proposition.
- Material Cost Variation
Different materials possess varying price points. Some specialized alloys or ceramics, often crucial for extreme acid resistance, command higher initial costs compared to less resistant alternatives. This difference in cost necessitates a comprehensive evaluation of the long-term return on investment, considering potential maintenance, repair, and downtime costs. A higher upfront cost might be justifiable if it translates to a longer operational lifespan or reduced maintenance requirements.
- Installation and Implementation Costs
The installation process for "acid armor" can vary significantly. Complex installation procedures often result in higher costs. This encompasses factors such as specialized labor requirements, specialized equipment, and the intricacy of the application itself. Economical solutions may involve simpler, easier-to-implement methods, even if they slightly compromise the absolute level of acid resistance. These considerations necessitate a trade-off analysis between installation costs and the desired level of protection.
- Maintenance and Repair Costs
The anticipated maintenance and repair expenses throughout the lifespan of the "acid armor" are significant considerations. Materials with inherent self-healing properties or those that require less frequent maintenance offer substantial long-term savings. Materials that are easier to repair or replace in case of damage will minimize downtime and associated costs. These maintenance and repair requirements are crucial in assessing the overall cost-effectiveness of a particular "acid armor" solution, including factors like the frequency of inspections, necessary spare parts, and specialized personnel.
- Long-Term Operational Efficiency
A significant long-term factor is the operational efficiency maintained by the "acid armor." Materials with exceptional acid resistance can contribute to reduced downtime and extended operational periods. This efficiency translates to cost savings. Materials that effectively prevent corrosion minimize the need for unscheduled repairs and maintenance, ultimately reducing operational expenses. Careful assessment of expected service life and the potential savings through reduced downtime and maintenance needs are crucial in quantifying the long-term value proposition.
Ultimately, evaluating "acid armor" through a cost-effectiveness lens demands a comprehensive assessment of all associated expenses. It is not merely the initial material cost but also the sum of installation, maintenance, and operational factors. The most cost-effective solution frequently isn't the lowest-priced option but one that optimizes the entire lifecycle cost, achieving the best balance between protection and expenditure.
7. Environmental Impact
The selection and application of materials designated as "acid armor" have significant environmental implications. These implications span the entire lifecycle of the material, from its extraction and manufacturing to its eventual disposal. A holistic evaluation of the environmental impact is crucial in the development and implementation of effective and sustainable protective solutions.
- Material Sourcing and Manufacturing
The raw materials used in crafting "acid armor" often originate from various extraction processes. Considerations include the environmental footprint of mining operations, the energy consumption during refining, and the potential for habitat disruption. The manufacturing process itself, including the energy required for shaping, alloying, or coating, also contributes to the material's overall environmental burden. The selection of materials with lower environmental impact throughout the supply chain is crucial. For example, recycled materials or those sourced from sustainable operations minimize the negative environmental consequences of production.
- Waste Generation and Disposal
The disposal of "acid armor" materials, especially after their service life, poses a considerable environmental challenge. Proper disposal methods are necessary to prevent contamination of soil or water resources. The potential for leaching of hazardous substances from the material during decomposition or improper disposal should be meticulously considered. Recycling and reuse of components, if feasible, can significantly reduce the waste stream generated by the application of "acid armor." Careful consideration should be given to the entire life cycle, including end-of-life management and proper recycling protocols.
- Energy Consumption During Use
The energy consumed throughout the operational life of the "acid armor" material should be factored into the overall environmental assessment. For example, materials that necessitate higher energy expenditure for maintenance, repairs, or replacement during operation have a greater environmental impact. Materials that can withstand longer use periods without degradation reduce the energy demands associated with frequent replacements, thereby mitigating the overall environmental burden. The energy efficiency of the equipment employing the "acid armor" is also a relevant aspect.
- Chemical Interactions and Emissions
The chemical reactions between "acid armor" and the surrounding environment, particularly in industrial settings, might generate emissions or byproducts that affect air or water quality. The choice of materials with minimal detrimental chemical interactions minimizes potential pollution. Emissions generated during material processing and operational use should be evaluated and mitigated through appropriate technologies. This may involve investigating the potential for leaching, chemical reactions, and the generation of harmful byproducts.
Ultimately, the environmental implications of "acid armor" extend beyond the material itself to encompass its manufacturing, application, and eventual disposal. A comprehensive assessment that factors in sourcing, waste generation, energy consumption, and chemical interactions is imperative for the design and implementation of truly sustainable solutions. Minimizing the overall environmental impact throughout the entire lifecycle of "acid armor" will be crucial in its continued application. This necessitates a shift towards materials with lower embodied environmental impacts, promoting closed-loop systems, and embracing responsible waste management practices.
Frequently Asked Questions about Acid Armor
This section addresses common inquiries regarding materials designed to resist acid corrosion, often referred to as "acid armor." These questions provide insights into the properties, applications, and considerations surrounding these protective solutions.
Question 1: What exactly is "acid armor," and what makes it different from other protective materials?
Acid armor encompasses materials with exceptional resistance to corrosive acids. Differentiating factors include specific chemical compositions that actively counter or neutralize the acid's destructive effects. They often exhibit higher resistance to specific acid types, concentrations, and environmental stressors compared to standard protective coatings or materials. This heightened resistance stems from advanced formulations, creating a protective barrier or a chemical reaction that counteracts the acid's corrosive action.
Question 2: What industries utilize "acid armor" materials, and why is it essential in those settings?
Industries heavily reliant on chemical processes, such as chemical manufacturing, refining, and processing, extensively use acid armor. In these environments, exposure to corrosive acids is unavoidable. Acid armor safeguards equipment, ensuring prolonged operational life, preventing leaks, and mitigating environmental risks. The critical need for such materials arises from the need to maintain continuous operation and prevent costly shutdowns and repairs caused by acid damage.
Question 3: How does the composition of "acid armor" materials influence their effectiveness against different acids?
The chemical makeup directly impacts the resistance to specific acids. A material highly resistant to dilute sulfuric acid might not perform as well against concentrated hydrofluoric acid. The chemical structure of the acid armor material dictates its ability to form a protective barrier or neutralize the targeted acid. Selecting the appropriate composition requires detailed analysis of the chemical interactions between the material and the specific acid. Rigorous testing and validation are crucial to ensure compatibility and effectiveness.
Question 4: What factors beyond the chemical composition affect the durability of "acid armor"?
Durability depends on factors like the material's internal structure, its ability to withstand stresses (thermal, mechanical, and chemical), and environmental conditions. Structural integrity, absence of defects, and resistance to stress corrosion cracking are vital for extended protection. Materials subjected to continuous operation and dynamic conditions need to withstand repeated exposure, thermal variations, and fluctuating pressures. Factors like fatigue, creep, and stress cracking significantly impact longevity.
Question 5: How does the cost-effectiveness of "acid armor" materials factor into their application?
Cost-effectiveness considers the material's initial cost, installation expenses, potential maintenance requirements, and long-term operational efficiency. The high initial cost of specialized materials might be offset by minimized maintenance and extended operational life, leading to a reduced total cost of ownership. Comprehensive lifecycle cost analysis is crucial for accurate assessments and efficient selection. Trade-offs between immediate costs and long-term operational benefits are crucial in determining optimal solutions.
In summary, "acid armor" materials represent sophisticated solutions for protecting equipment and infrastructure in chemically demanding environments. Understanding their composition, properties, and application-specific needs is essential for choosing the optimal protection strategy.
Next, we will delve into specific types of acid armor materials and their practical applications.
Conclusion
This exploration of materials designated as "acid armor" has highlighted the multifaceted nature of corrosion resistance in demanding environments. Key considerations encompass material composition, structural integrity, performance under stress, durability, application specificity, cost-effectiveness, and environmental impact. The selection of appropriate "acid armor" depends critically on the specific chemical environment, operational conditions, and projected lifespan. The interplay of these factors dictates the material's efficacy in safeguarding equipment and infrastructure from the damaging effects of corrosive acids. The choice of material should not be based solely on initial cost but on a comprehensive evaluation of the entire lifecycle, including anticipated maintenance and potential environmental consequences.
Moving forward, research and development in "acid armor" materials must continue to address the need for improved performance, enhanced sustainability, and economic viability. Continued exploration of novel material compositions, manufacturing processes, and testing methodologies will be vital in creating more effective and sustainable protective solutions for the future. The significance of choosing the right "acid armor" extends beyond mere material science to encompass safety, environmental protection, and economic considerations in industries reliant on chemical processes and corrosive environments. A focused and comprehensive understanding of these complexities will lead to more robust and durable materials, ultimately improving safety standards, preventing environmental damage, and ensuring the long-term viability of critical infrastructures.

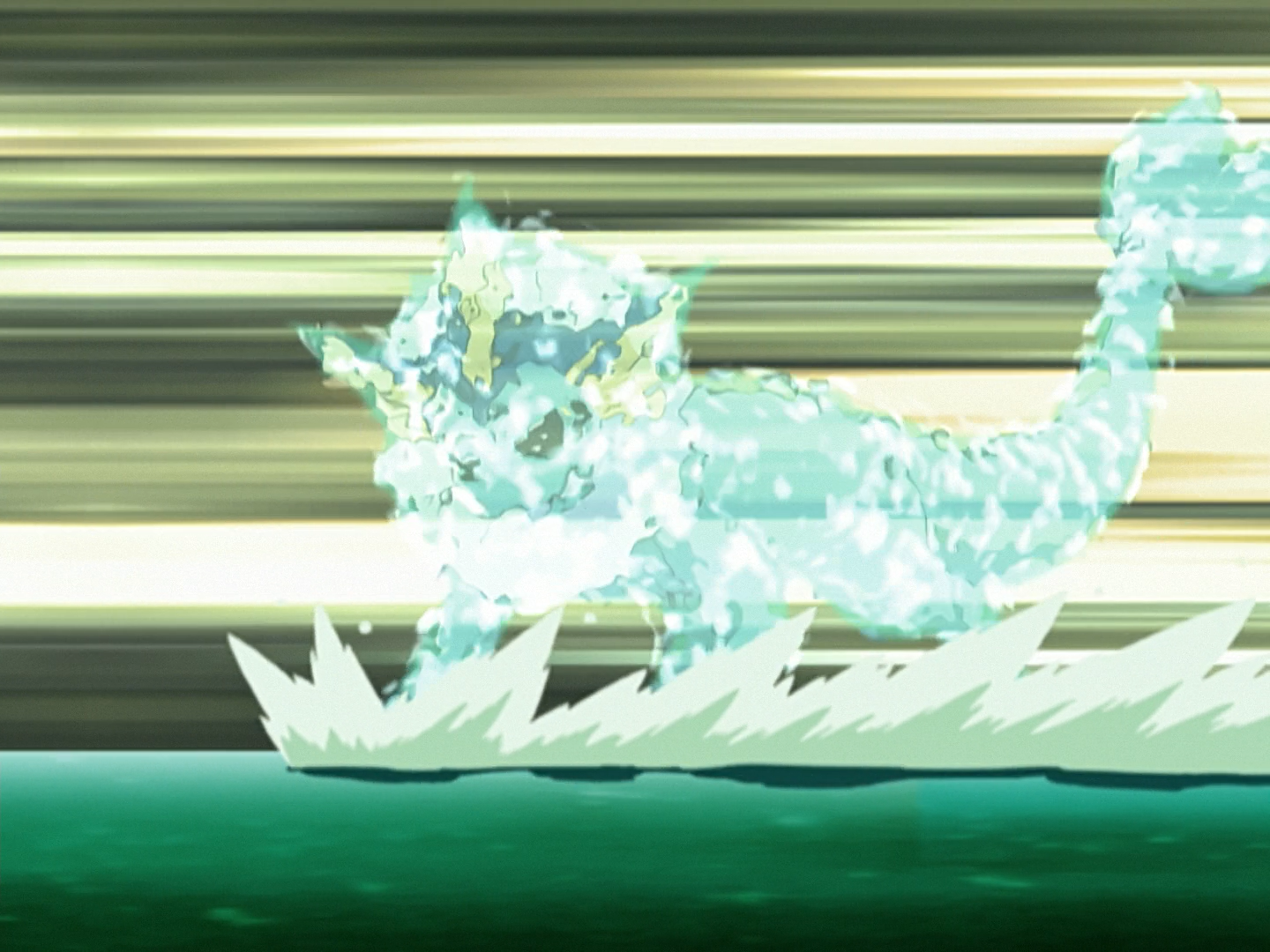

Detail Author:
- Name : Aracely Schulist Jr.
- Username : reinhold.reinger
- Email : tromp.guido@hotmail.com
- Birthdate : 1972-10-20
- Address : 373 Nienow Inlet Apt. 990 Fannymouth, AR 58704
- Phone : 703-298-1086
- Company : McLaughlin-Zieme
- Job : Paperhanger
- Bio : Dolore nostrum sunt mollitia. Eligendi ipsam saepe odio accusantium. Suscipit ipsum qui assumenda officiis atque voluptates odit.
Socials
instagram:
- url : https://instagram.com/vincenzo_cole
- username : vincenzo_cole
- bio : Numquam tenetur dicta quo dolorem minima. Aut et sint modi soluta. Nemo recusandae consectetur aut.
- followers : 6995
- following : 2657
linkedin:
- url : https://linkedin.com/in/colev
- username : colev
- bio : Praesentium et magni impedit magnam omnis quidem.
- followers : 2451
- following : 2632
facebook:
- url : https://facebook.com/vincenzo_cole
- username : vincenzo_cole
- bio : Officia doloribus dicta hic facere fugit voluptas et explicabo.
- followers : 5239
- following : 1267