What are the characteristics and uses of a particular type of high-performance steel?
This specialized steel alloy exhibits exceptional strength, durability, and resistance to wear and tear. Its unique composition and metallurgical processing yield a material suitable for demanding applications requiring high tensile strength and exceptional corrosion resistance. For example, this steel might be employed in the construction of heavy machinery components or high-pressure vessels. The specific properties of this steel are a result of precise control over alloying elements and heat treatment protocols.
The specific benefits of this steel alloy hinge on its ability to withstand extreme mechanical stress and resist corrosion in challenging environments. Its high tensile strength makes it ideal for structural applications, while its corrosion resistance extends its lifespan in harsh environments. The material's strength-to-weight ratio is also significant, making it a valuable choice where weight reduction is critical without compromising performance. The precise metallurgical techniques and control of chemical composition, along with careful heat treatment, determine the desirable properties of this steel type, making it suitable for demanding applications across various industries. Historically, advancements in metallurgy have driven the development of new steel alloys like this, responding to evolving engineering needs.
Moving forward, let's delve into the applications and impact of this specific type of high-performance steel in various industrial sectors.
erossteel
Understanding the key aspects of this specialized steel is crucial for evaluating its suitability in diverse applications. Its properties are carefully engineered to optimize performance in demanding environments.
- Strength
- Durability
- Corrosion resistance
- High tensile strength
- Precision manufacturing
- Alloy composition
These aspects, taken together, define the exceptional characteristics of this steel. Strength and durability are paramount for structural components. Corrosion resistance extends operational lifespans in harsh conditions. High tensile strength enables efficient load bearing. Precision manufacturing ensures consistent quality and dimensional accuracy. Proper alloy composition directly impacts the steel's properties. These six aspects collectively contribute to the steel's suitability for applications requiring exceptional performance, such as high-pressure vessels and critical components in heavy machinery. A deep understanding of these aspects allows engineers to effectively select and integrate this material into complex systems.
1. Strength
The strength of erossteel is a defining characteristic, directly impacting its suitability for diverse applications. Understanding the multifaceted nature of this strength is critical for evaluating the material's performance in challenging environments.
- Tensile Strength and Yield Strength
High tensile and yield strengths are crucial factors in the material's ability to withstand significant stress without permanent deformation. These properties directly influence the material's capacity to support heavy loads and resist failure under pressure. Components fabricated from erossteel with exceptional tensile strength can support higher loads or endure more demanding operational conditions. Examples include pressure vessels in chemical plants or structural components in heavy machinery.
- Fatigue Resistance
The ability to withstand repeated stress cycles, or fatigue resistance, is vital for longevity in dynamic environments. Erossteel's fatigue resistance determines its ability to endure consistent stress over extended periods without failing prematurely. This is critical in applications experiencing fluctuating loads, such as bridges or rotating machinery components.
- Hardness and Toughness
The material's hardness and toughness contribute to its overall strength. Hardness resists indentation, while toughness allows the material to absorb energy without fracturing. These combined properties define erossteel's resistance to wear and tear. Examples include cutting tools, impact-resistant parts, or components subjected to abrasive environments.
- Ductility and Plasticity
While strength is paramount, ductility and plasticity, the material's ability to deform under stress without fracture, are critical for some applications. Erossteel's combination of strength and ductility influences its formability during manufacturing, making it appropriate for parts needing shaping or bending, potentially in situations requiring flexibility and resilience.
The comprehensive understanding of erossteel's strength properties, encompassing tensile strength, fatigue resistance, hardness-toughness balance, and ductility-plasticity characteristics, is indispensable for precise material selection and successful application design. The interplay of these factors makes erossteel a robust and reliable material in challenging applications.
2. Durability
Durability in erossteel is a multifaceted attribute stemming from its metallurgical composition and manufacturing processes. Superior durability is a direct result of the material's inherent resistance to degradation, encompassing factors such as corrosion resistance, fatigue resistance, and impact toughness. The material's composition and subsequent heat treatment procedures directly influence its resistance to wear and tear over extended operational periods. Real-world applications underscore the importance of this characteristic. Components manufactured from erossteel, designed to endure high-stress environments, demonstrate sustained performance in heavy machinery, pressure vessels, and demanding industrial settings. The longevity of such components reflects the material's inherent durability.
The practical significance of understanding erossteel's durability extends to several key areas. Engineers can confidently design systems requiring prolonged operation in challenging environments, knowing the material's resistance to degradation. This translates into optimized component lifespans, reduced maintenance requirements, and substantial cost savings over the material's lifespan. Predictable performance under stress, fatigue, and exposure to corrosive elements is a crucial aspect of selecting erossteel for specific applications, ensuring the integrity and reliability of the entire system. Choosing erossteel for applications demanding prolonged operation, in industries ranging from aerospace to energy production, exemplifies the practical advantages of durable materials.
In summary, erossteel's durability is a critical consideration in its application. The material's inherent resistance to degradation, manifested through its specific alloy composition and processing, enables exceptional longevity. Understanding the interconnectedness between material properties and operational demands allows engineers to select and design durable systems. This understanding is essential for optimized performance, reduced maintenance, and overall system reliability. The successful integration of erossteel in various industrial sectors underscores the significant impact of this critical material property in achieving long-term operational effectiveness and cost-efficiency.
3. Corrosion Resistance
Corrosion resistance is a critical attribute of erossteel, directly influencing its suitability for applications in demanding environments. The ability of this alloy to withstand corrosive agents is essential for extended service life and operational reliability in various industrial settings. Understanding the mechanisms underpinning this resistance provides insights into its selection for specific applications. Factors such as the material's chemical composition and metallurgical processing play a crucial role.
- Alloy Composition and its Role
The specific alloying elements in erossteel play a pivotal role in its corrosion resistance. The presence of certain elements creates a protective layer, often an oxide film, on the surface of the material. This passive layer inhibits further corrosion by preventing direct contact between the metal and corrosive elements. The precise composition and its control are essential for optimizing this protective barrier. Variations in alloying elements, intentional or accidental, can directly impact the material's resistance to specific corrosive environments.
- Passive Film Formation
The formation of a passive film, crucial in corrosion resistance, is often an electrochemical process. The film acts as a barrier, separating the metal from the corrosive medium. The stability and integrity of this film are directly tied to the material's resistance to degradation. Variations in environmental conditions, such as pH and the presence of specific ions, can affect the passive film's stability. This highlights the need for careful consideration of the specific corrosive environment in which erossteel components will operate.
- Environmental Factors and their Impact
The specific corrosive environment is a significant determinant of erossteel's performance. Factors like the concentration of corrosive elements, presence of oxygen, and temperature variations directly impact the rate of corrosion. These factors must be carefully considered during the design phase. For example, erossteel components in a saltwater environment may exhibit different corrosion rates than in a neutral solution. The selection of erossteel necessitates a thorough understanding of the specific environmental conditions to which the material will be exposed.
- Practical Applications and Demonstrated Performance
Erossteel's corrosion resistance is exemplified in diverse applications. In high-pressure vessels in chemical processing plants or structural components in marine environments, where protection from corrosion is critical, erossteel consistently demonstrates exceptional performance. Real-world operational data often substantiates the material's reliability under challenging conditions. Detailed assessments are often essential in determining suitability and lifespan. The suitability of erossteel in specific applications hinges on matching the material's inherent corrosion resistance with the anticipated environmental stresses.
In conclusion, the corrosion resistance of erossteel arises from a combination of factors, including alloying composition, passive film formation, and the specific corrosive environment. Understanding these elements is crucial for engineers when designing components for long-term reliability in challenging conditions. The extensive application history demonstrates the practical utility of erossteel in applications where corrosion resistance is a critical performance factor. Consequently, meticulous analysis is essential when choosing materials for specific conditions.
4. High Tensile Strength
High tensile strength is a defining characteristic of erossteel, directly impacting its suitability for demanding applications. The material's ability to withstand substantial tension without yielding is a consequence of its precise metallurgical composition and meticulous manufacturing processes. This attribute is crucial for applications requiring components to bear heavy loads, resist deformation, and maintain structural integrity under pressure. The high tensile strength of erossteel allows for the creation of lighter-weight, yet stronger, components, an important consideration in aerospace and other industries requiring weight optimization without sacrificing robustness. For instance, in high-pressure vessels used in chemical processing, the high tensile strength of erossteel ensures structural integrity under extreme conditions.
The importance of understanding the relationship between high tensile strength and erossteel extends beyond its inherent properties. Engineers leverage this understanding to design and optimize components, enabling them to withstand specific forces. Components fabricated from erossteel with high tensile strength can be designed with smaller cross-sectional areas, leading to weight reduction without compromising structural performance. This is crucial in industries where weight is a critical factor, such as aerospace, where reduced weight translates directly to increased fuel efficiency and performance. The reliable performance of erossteel under stress, as demonstrated in various applications, highlights the significance of this material property.
In summary, the high tensile strength of erossteel is a direct consequence of its metallurgical composition. This property allows for the design of lightweight yet robust components, making erossteel indispensable in numerous high-stress applications. Engineers must carefully evaluate the specific tensile strength requirements of an application when selecting materials, ensuring a reliable and efficient design. The understanding and application of high tensile strength in erossteel are vital for achieving optimal performance and cost-effectiveness in various industries.
5. Precision Manufacturing
Precision manufacturing is intrinsically linked to the properties and applications of erossteel. The high performance and exacting requirements of erossteel necessitate manufacturing processes capable of achieving tight tolerances and consistent quality. This meticulous approach ensures the material's intended properties are realized in finished components.
- Dimensional Accuracy
Precise control over dimensions during manufacturing is paramount. Erossteel components frequently require tight tolerances to function correctly in intricate systems. For example, in high-pressure vessels, precise dimensions are essential for proper sealing and stress distribution. Deviations from specified tolerances can lead to component failure, compromised performance, or even safety risks. The precision manufacturing process ensures the consistency of these dimensions across numerous components, guaranteeing reliable functionality.
- Surface Finish and Quality
The surface finish of erossteel components significantly impacts their performance and lifespan. Smooth surfaces minimize friction, potentially improving efficiency in moving parts. In addition, certain surface treatments, achieved through precision manufacturing, contribute to enhanced corrosion resistance and longevity. Applications requiring a polished surface, such as components in high-end machinery, benefit from precision manufacturing methods ensuring a consistent and desirable surface finish.
- Material Uniformity and Consistency
Erossteel's properties depend on a consistent and uniform metallurgical structure. Precision manufacturing methods play a key role in maintaining this uniformity across the material. Processes like controlled heat treatments, intricate alloying procedures, and optimized forging techniques contribute to consistent strength, hardness, and ductility. Maintaining these uniform properties is critical for ensuring predictable behavior and reliable performance in diverse applications.
- Complex Geometries and Component Fabrication
The demanding nature of some erossteel applications frequently necessitates the creation of complex geometries. Advanced manufacturing techniques like CNC machining, additive manufacturing, and specialized forging methods are required to produce components with intricate shapes and features. These techniques, integral to precision manufacturing, contribute to the design flexibility and functionality possible with erossteel. For instance, intricate components in aerospace applications or specialized tooling in industrial machinery rely heavily on precision manufacturing capabilities.
In conclusion, the interplay between precision manufacturing and erossteel is vital for achieving optimal performance and reliability. The ability to consistently produce components with precise dimensions, surface finishes, and material properties ensures the desired functionality and lifespan of erossteel parts. This precision ultimately underpins the reliability and applicability of erossteel in diverse industries.
6. Alloy Composition
Alloy composition is fundamental to the properties of erossteel. The precise selection and proportioning of elements directly influence the material's strength, durability, and corrosion resistance. Understanding this interplay is critical for appropriate material selection and application design.
- Constituent Elements and Their Impact
The specific elements comprising erossteel, and their relative percentages, determine the material's characteristics. Careful control over these elements directly affects the microstructure, and consequently, the mechanical and physical properties. For instance, the presence of chromium contributes to corrosion resistance, while nickel may enhance toughness. Variations in the proportions of these elements can dramatically alter the material's behavior under stress.
- Phase Transformations and Microstructure
The interactions between alloying elements during processing lead to specific phase transformations and microstructures. These microstructural features, often microscopic in scale, dictate the material's ultimate mechanical properties. For example, controlled precipitation of specific phases can strengthen the material, while the size and distribution of these phases directly affect its susceptibility to fracture or deformation.
- Effect on Mechanical Properties
Alloy composition directly influences erossteel's mechanical characteristics, including tensile strength, hardness, and ductility. Adjusting element ratios can fine-tune these properties to meet the requirements of specific applications. Higher carbon content may increase hardness but decrease ductility, while increased nickel content can enhance toughness. This direct relationship between composition and properties necessitates careful consideration for the intended application.
- Corrosion Resistance Mechanisms
Alloy composition plays a vital role in shaping erossteel's corrosion resistance. Specific elements, particularly chromium and nickel, promote the formation of a protective passive oxide layer on the material's surface. This layer hinders the penetration of corrosive agents, extending the material's lifespan in harsh environments. The optimal composition for corrosion resistance depends on the specific corrosive elements and conditions.
In conclusion, the alloy composition of erossteel is a critical determinant of its performance in various applications. Precise control over constituent elements and their proportions allows for tailoring the material's properties to meet the demanding needs of specific applications. This detailed understanding underpins the effective selection, fabrication, and implementation of erossteel components in engineering projects.
Frequently Asked Questions about Erossteel
This section addresses common inquiries about erossteel, providing concise and informative answers to promote a comprehensive understanding of this material.
Question 1: What distinguishes erossteel from other high-strength steels?
Erossteel's unique alloy composition, meticulously controlled manufacturing processes, and subsequent heat treatments result in specific mechanical properties. These factors often lead to superior strength, corrosion resistance, and durability compared to standard high-strength steels. Detailed analysis of the alloying elements and manufacturing protocols is essential for comparing and contrasting its performance with other similar materials.
Question 2: What are the primary applications for erossteel?
Erossteel finds widespread application in demanding environments where high strength, durability, and corrosion resistance are crucial. Examples include critical components in heavy machinery, pressure vessels in chemical processing, and structural elements in demanding industrial settings. The specific applications frequently necessitate an in-depth examination of the operational conditions, including stresses and environmental factors.
Question 3: How does the corrosion resistance of erossteel differ from other steels?
Erossteel's corrosion resistance stems from its unique alloying elements and precise metallurgical processing. This leads to the formation of a protective passive layer on the surface, mitigating corrosion. Comparative analysis often involves examining the specific corrosive environment and the resultant corrosion rates of different steel types under those conditions.
Question 4: What factors influence the selection of erossteel for a particular project?
The selection process for erossteel typically considers the specific application requirements, including environmental conditions, load specifications, desired lifespan, and cost-effectiveness. A careful balance between these factors guides the choice of materials to ensure the appropriate performance and reliability for the specific project. Detailed calculations and assessments play a pivotal role in this decision-making process.
Question 5: What are the potential limitations of using erossteel?
While erossteel offers considerable advantages, its cost, availability, and potential limitations in terms of formability, weldability, or certain specialized treatments need to be evaluated against the application's specific requirements. A thorough cost-benefit analysis is frequently needed alongside an assessment of potential limitations related to material properties.
A thorough understanding of these FAQs will enable a more informed decision-making process when considering erossteel for specific applications. Further inquiry about specific aspects of this alloy can be directed to qualified specialists in materials engineering.
Conclusion
Erossteel, a specialized steel alloy, emerges as a valuable material in demanding industrial applications. Its exceptional strength, durability, and corrosion resistance stem from a precise alloy composition and meticulous manufacturing processes. This article explored key attributes, including high tensile strength, enabling robust support of heavy loads; exceptional fatigue resistance, ensuring longevity under cyclic stresses; and noteworthy corrosion resistance, extending service life in harsh environments. The intricate interplay of these properties underpins the material's effectiveness in high-pressure vessels, heavy machinery components, and critical structural elements. The consistent quality achieved through precision manufacturing further underscores the material's reliability in complex systems. Ultimately, the exploration highlights erossteel's significant role in optimizing performance and reliability in various industrial sectors, directly impacting structural integrity and operational efficiency.
Further investigation into the specific performance characteristics of erossteel under different environmental conditions, combined with advanced modeling and simulations, will lead to even more sophisticated applications. This knowledge will be critical in driving innovation across industries requiring high-strength, durable, and corrosion-resistant materials. The material's continued use in challenging environments and its application in cutting-edge technologies promise to shape future engineering designs and manufacturing practices.
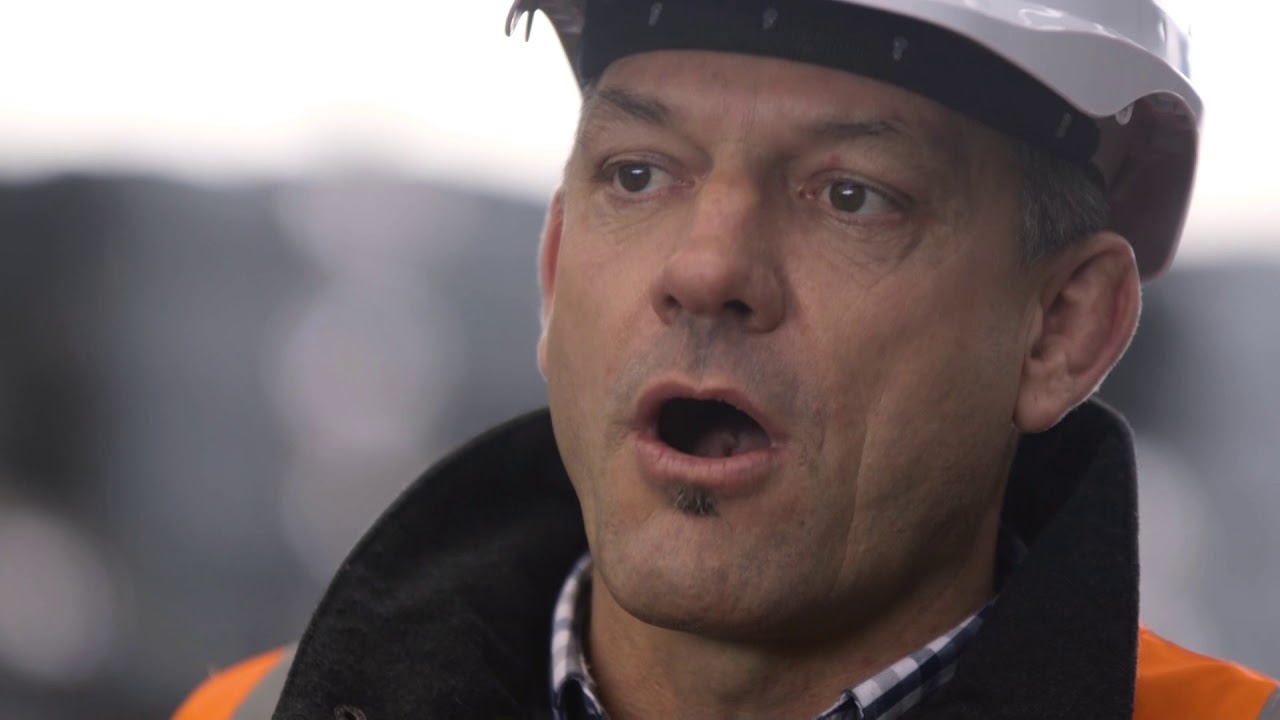
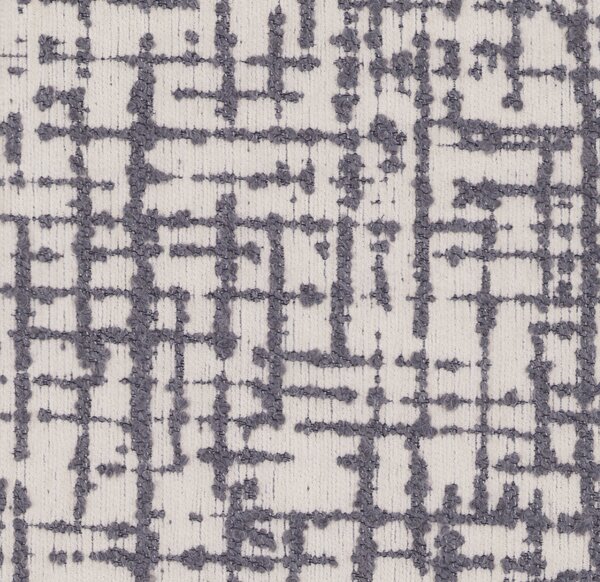
Detail Author:
- Name : Rogelio Hartmann I
- Username : vconroy
- Email : kyle64@yahoo.com
- Birthdate : 2000-05-16
- Address : 641 Kub Valleys Apt. 290 New Tatum, TN 26037-1547
- Phone : +1 (551) 534-8064
- Company : Runolfsson-Lockman
- Job : Environmental Engineer
- Bio : Blanditiis sit natus tenetur ut explicabo quo error eum. Dolore quia facilis nulla voluptate. Et deserunt sed et voluptatum. Vel illum eligendi et blanditiis eos distinctio cum.
Socials
twitter:
- url : https://twitter.com/kylee.luettgen
- username : kylee.luettgen
- bio : Velit velit est aut libero ut qui. Quo vel accusantium sint maiores quos qui. Placeat quia harum qui animi.
- followers : 3830
- following : 590
facebook:
- url : https://facebook.com/kylee7954
- username : kylee7954
- bio : Totam consequatur et accusamus. Nihil necessitatibus doloribus deserunt nam.
- followers : 6378
- following : 955
instagram:
- url : https://instagram.com/kylee.luettgen
- username : kylee.luettgen
- bio : At suscipit illo sint et quia. Itaque pariatur ullam omnis possimus voluptatum est.
- followers : 4376
- following : 1008
tiktok:
- url : https://tiktok.com/@kyleeluettgen
- username : kyleeluettgen
- bio : Quod non necessitatibus veritatis beatae ullam et ratione error.
- followers : 2689
- following : 917
linkedin:
- url : https://linkedin.com/in/kyleeluettgen
- username : kyleeluettgen
- bio : Qui quo aliquid molestiae aut.
- followers : 2003
- following : 2041