What is the Significance of a System for Transferring and Coiling Materials?
This specialized system facilitates the efficient transfer and coiling of materials, often in industrial settings. Its design optimizes processes by reducing downtime and maximizing output. A well-engineered system ensures consistent material handling and a controlled coiling process, leading to high-quality results.
The benefits of such a system extend beyond efficiency. Precise coiling minimizes material waste, reduces the risk of damage during transport, and promotes overall process consistency. These features are crucial in manufacturing environments where standardized procedures and reliable outcomes are paramount. Historically, this technology has evolved alongside advancements in material science and automation, constantly improving to meet increasing production demands and standards.
This discussion now shifts to examine specific examples of how these systems are applied in various industrial settings. Different materials require distinct approaches, and understanding the appropriate system selection is critical to achieve optimal results.
Transcoil
Understanding the multifaceted nature of transcoil systems is crucial for optimizing material handling processes. Each element plays a vital role in achieving efficiency and consistency.
- Material transfer
- Automated coiling
- Precision control
- Reduced downtime
- High-quality output
- Minimize waste
- Consistent processes
- Enhanced safety
Transcoil systems, encompassing automated material transfer and precision coiling, directly impact manufacturing efficiency. Minimizing waste through accurate coiling procedures and consistent processes is paramount. Reduced downtime and enhanced safety features are further benefits. Examples include systems handling steel coils in a rolling mill or plastic film in a packaging plant. These systems, integrated with automated control systems, ensure a consistent workflow and high-quality output.
1. Material Transfer
Material transfer is a fundamental aspect of transcoil systems. Its efficiency directly impacts the overall performance and effectiveness of the entire operation. This involves the movement of materials from one location to another, often in a controlled and automated manner, critical to the functionality of transcoil processes.
- Mechanism and Design
The design of material transfer mechanisms within transcoil systems is crucial. These mechanisms may involve conveyors, robots, or automated guided vehicles (AGVs). Careful consideration of factors such as material type, weight, dimensions, and potential hazards is essential. Appropriate material handling equipment must be selected to ensure safe, efficient, and accurate movement of materials throughout the process.
- Throughput and Capacity
The capacity and throughput of material transfer systems directly affect the production rate. A system designed with limited transfer capacity will limit the overall processing rate, potentially impacting overall efficiency. Systems need to be designed to handle the anticipated volume and variety of materials without compromising speed or accuracy.
- Integration with Coiling Processes
Material transfer systems must seamlessly integrate with the coiling process. The transition between transfer and coiling must be smooth and reliable to maintain consistent material handling. Potential delays or disruptions during the transfer phase can lead to inconsistencies in the final coiled product. The system needs to effectively adjust to the demands of the coiling operation.
- Safety Considerations
Safety is paramount in material transfer systems. Mechanisms should be designed and operated to prevent accidents, minimize risks associated with material handling, and ensure the well-being of personnel. Safety features such as guards, emergency stops, and proper signage are essential components for any transcoil system involving material transfer.
In conclusion, material transfer is not a standalone component but a critical element within transcoil systems. Effective material transfer is directly tied to the efficiency, quality, and safety of the entire coiling process. Optimization of material transfer is essential for enhancing the functionality and productivity of the overall system. A robust, well-engineered transfer system ensures a reliable and consistent flow of materials, laying the groundwork for high-quality output and overall operational success within the transcoil environment.
2. Automated Coiling
Automated coiling is an integral component of transcoil systems. The precise and consistent coiling of materials is a key driver of productivity and efficiency within these systems. Without automation, the process would be significantly slower, prone to human error, and less adaptable to varying material types and volumes. Automated coiling directly enhances the efficiency and quality of transcoil systems, leading to improved output and reduced manufacturing costs. This automation results in a more consistent product, minimizing waste and maximizing the value derived from the coiled material.
Real-world examples illustrate the importance of automated coiling within transcoil. In steel mills, automated coilers ensure consistent coil dimensions and reduce material waste, impacting profitability and production output. In the textile industry, automated systems for coiling yarn or fabric ensure even tension and consistent product quality, leading to increased customer satisfaction and reduced production errors. The integration of automated coiling into transcoil systems enhances precision, flexibility, and the overall performance of the process. This precision is critical for industries relying on standardized components and tight tolerances.
The practical understanding of automated coiling within transcoil systems underscores the importance of seamless integration and technological advancement. Optimizing the entire transcoil system requires a deep understanding of how automated coiling contributes to the overall efficiency. Furthermore, the application of automated coiling in diverse industries highlights its universal value in enhancing precision, flexibility, and consistency, leading to significant benefits in terms of product quality, reduced waste, and increased productivity.
3. Precision Control
Precision control is paramount within transcoil systems. The ability to precisely control the movement, positioning, and tension of materials during transfer and coiling is essential for achieving consistent product quality, minimizing waste, and optimizing production efficiency. Effective precision control is directly linked to the overall success and performance of transcoil systems.
- Accurate Material Positioning
Precise positioning of materials is vital in transcoil systems. Accurate placement ensures coils are wound with consistent tension and dimensions. Errors in positioning can result in uneven coils, compromising structural integrity and reducing material yield. Applications in industries like steel fabrication or wire manufacturing demonstrate the critical role of accurate positioning to maintain dimensional consistency and prevent structural defects.
- Controlled Tension Management
Maintaining controlled tension during the coiling process is crucial. Precise tension control ensures uniform material density throughout the coil, impacting the coil's strength and longevity. Variable tension can lead to uneven material stress, potentially causing weaknesses or breaks in the coil. Sophisticated control systems are often used in applications where the coiling tension must be consistently maintained, for instance, in the production of high-strength wire coils.
- Automated Monitoring and Adjustment
Automated systems capable of continuously monitoring and adjusting parameters are critical to maintaining precision control. Monitoring ensures compliance with specifications, while automatic adjustments enable adaptability to variations in material properties and production requirements. Real-time feedback loops allow systems to react to deviations from the desired parameters and maintain optimal coiling conditions.
- Integration with Other Systems
Precision control in transcoil systems necessitates seamless integration with other production elements. This involves coordinating movement and tension with other processing stages, like cutting, labeling, or packaging. Effective integration prevents delays and ensures optimal workflow consistency throughout the production line. The system's ability to respond and adapt to changes in the material flow or other connected processes is essential for smooth operation.
The features of precision control, spanning accurate material positioning, tension management, automated adjustments, and system integration, form the bedrock of effective transcoil operations. By minimizing inconsistencies in the coiling process and adapting to changes in materials and production demands, precise control directly contributes to efficiency gains, improved product quality, and reduced material waste in transcoil systems. This results in optimized production output and enhanced overall performance.
4. Reduced Downtime
Reduced downtime is a critical performance metric in transcoil systems. Minimizing interruptions in the transfer and coiling process directly impacts production output and profitability. Efficient transcoil systems are designed to minimize standstill periods, maximizing uptime and operational effectiveness.
- Preventive Maintenance Strategies
Proactive maintenance schedules, including regular inspections and component replacements, are crucial. Identifying potential issues before they lead to system failures prevents costly downtime. Predictive maintenance, leveraging sensor data and machine learning algorithms, can further enhance this approach by anticipating and addressing potential problems before they occur. This proactive approach minimizes unexpected shutdowns.
- Robust System Design
Transcoil systems should be designed with redundant components and fail-safes. Redundancy allows the system to continue operating if one component fails, preventing complete system shutdown. Fail-safes automatically intervene to prevent damage or catastrophic failures, ensuring continued operation. Well-designed systems offer higher resilience to malfunctions, leading to lower downtime.
- Optimized Workflow Design
Streamlined processes and optimized workflows minimize material handling bottlenecks. Efficient material flow prevents congestion and delays, reducing the likelihood of interruptions during coiling operations. Workflow optimization, through process analysis and improvement, leads to quicker cycle times and fewer interruptions, ultimately maximizing production time.
- Rapid Troubleshooting and Repair
Systems should be designed with readily accessible components and clear maintenance procedures. Easy access for maintenance and repair personnel allows quick diagnosis and fixes when issues arise. A well-equipped maintenance team, coupled with readily available parts, significantly decreases the time needed for repairs, minimizing downtime.
In conclusion, reduced downtime in transcoil systems is not merely a goal but a critical aspect of the overall system's effectiveness. By implementing preventive maintenance, robust designs, optimized workflows, and robust repair procedures, transcoil operators can significantly enhance production efficiency and profitability.
5. High-quality output
High-quality output within transcoil systems is inextricably linked to precise and consistent material handling. The quality of the final coiled product hinges on the efficiency and accuracy of the entire process. Maintaining consistent tension, dimensions, and overall structural integrity throughout the coiling process is essential for a high-quality end product. Achieving this demands meticulous control and attention to detail at every stage of material transfer and winding.
- Consistent Coil Dimensions
Uniform coil dimensions are critical in many applications. Precise coiling ensures consistent width, thickness, and overall form, crucial for subsequent manufacturing stages or end-use applications. In industries requiring standardized components, such as automotive or aerospace manufacturing, variations in coil dimensions can lead to significant issues downstream, requiring costly rework or scrap. A well-designed transcoil system guarantees uniform dimensions, optimizing efficiency and minimizing waste.
- Controlled Tension and Uniformity
Uniform tension throughout the coil is essential for product quality. Uneven tension leads to variations in material stress, impacting the finished product's strength, durability, and aesthetic properties. High-quality transcoil systems maintain consistent tension, preventing potential defects and ensuring reliability in the final product. Examples include steel coils for construction or wire coils for electronics, where consistent tension ensures tensile strength and dimensional accuracy.
- Minimal Material Waste
Efficient and precise coiling minimizes material waste. Optimal coiling techniques and controlled processes reduce material loss during the coiling operation, leading to higher yields and lower manufacturing costs. In industries facing strict cost controls, like the packaging or textile industries, minimizing waste through optimized coiling is a significant factor in achieving high-quality output and overall profitability.
- Reduced Defects and Variations
Consistent handling and automated control within a transcoil system minimize the occurrence of defects and variations in the finished coils. This reduces the likelihood of issues with the material's integrity and structural uniformity. High-quality output stems from minimizing the potential for errors in the winding process, leading to a more reliable product. This is critical in industries with stringent quality control standards.
Ultimately, high-quality output in a transcoil system is a result of a comprehensive approach to precision, consistency, and efficiency. By minimizing waste, controlling tension, maintaining dimensions, and reducing defects, a robust transcoil system ensures a consistent and reliable product that meets or exceeds quality standards, making it a fundamental driver of success in many industrial processes.
6. Minimize Waste
Minimizing waste is a critical component of effective transcoil systems. The connection is direct and consequential. Efficient material handling and precise coiling, hallmarks of transcoil systems, directly influence waste reduction. Minimizing material loss during the transfer and coiling process reduces scrap and rework, lowering manufacturing costs and improving profitability. Optimized coil geometry, achieved through precise control mechanisms within transcoil systems, directly reduces material wasted during subsequent processing stages, further enhancing efficiency. Waste reduction is not merely an ancillary benefit; it's an integral aspect of the system's overall design and operation.
Real-world examples highlight the practical significance of this connection. In steel mills, optimized transcoil systems minimize the scrap resulting from improper coiling, saving significant quantities of raw material. In the electronics industry, precise coiling of wire minimizes the amount of unusable material, a factor crucial in maintaining competitive pricing and meeting stringent quality standards. These examples demonstrate the tangible benefits of minimizing waste within transcoil systems. Furthermore, the accurate placement and tensioning of materials in transcoil systems prevent issues like uneven coils, which frequently lead to material damage or scrap during subsequent processing. The precise control inherent in transcoil systems, by extension, reduces the likelihood of wasted materials.
Understanding the link between minimizing waste and transcoil is fundamental for optimizing industrial processes. By effectively managing material flow and coiling parameters, organizations can enhance their resource utilization and operational efficiency. Furthermore, this awareness allows for the development of more environmentally sustainable manufacturing practices. The inherent cost savings and improved environmental performance resulting from waste minimization make the focus on transcoil system design a crucial element of modern industrial strategy. Addressing waste reduction within transcoil systems is not simply a cost-saving measure; it's a key component of sustainable and profitable manufacturing.
7. Consistent Processes
Consistent processes are fundamental to the efficacy of transcoil systems. Reliable and repeatable procedures are essential for achieving consistent product quality, minimizing waste, and maximizing operational efficiency. The adherence to established standards ensures predictable outcomes and minimizes variability, a critical factor in industrial settings where high-volume production and strict quality control are paramount.
- Standardized Operating Procedures (SOPs)
Well-defined SOPs are crucial for maintaining consistency. These procedures outline the steps involved in material transfer, coiling, and associated tasks. Consistency in following SOPs ensures that every coil is handled and wound according to the same predefined standards. Deviation from established procedures can lead to variations in coil dimensions, tension, and overall quality, affecting subsequent processes and potentially increasing waste.
- Automated Control Systems
Automated control systems play a vital role in maintaining consistent processes. These systems monitor key parameters like tension, speed, and positioning during the coiling process. Constant monitoring and adjustments based on pre-programmed parameters ensure that each coil meets predefined specifications. Automated systems reduce the potential for human error, fostering consistent outcomes across large production runs.
- Regular Maintenance and Calibration
Regular maintenance and calibration of equipment are critical for maintaining consistency. Routine checks and calibrations of machinery, ensuring optimal function, help minimize deviations in material handling and winding operations. Preventive maintenance procedures decrease the likelihood of unexpected equipment failures, which can lead to inconsistencies in the process and compromise product quality. Accurate measurements are crucial for maintaining dimensions and tension, vital for achieving consistent coil quality.
- Process Monitoring and Data Analysis
Continuous monitoring of the entire transcoil process and analysis of the collected data are essential components of consistent procedures. Detailed data logs enable identification of trends, patterns, and potential bottlenecks in the system. This data-driven approach allows for proactive adjustments, improvements in efficiency, and early detection of inconsistencies that could lead to production issues. Consistent data collection helps pinpoint areas for improvement and refinement in the transcoil system, ensuring ongoing quality.
In summary, consistent processes within transcoil systems are not simply a matter of adherence to procedures but a strategic approach to ensuring high-quality, reliable output. SOPs, automated controls, preventative maintenance, and data-driven adjustments work together to create a repeatable and predictable system, minimizing variability and maximizing the efficiency of the entire manufacturing process. This structured approach directly impacts the quality and reliability of the final product, a critical factor for success in any industrial environment.
8. Enhanced Safety
Enhanced safety within transcoil systems is not merely an add-on; it's a fundamental aspect integral to the system's overall effectiveness and operational success. Safeguarding personnel and minimizing risks associated with material handling are paramount, especially in high-volume industrial settings. A comprehensive approach to safety, encompassing preventive measures and contingency plans, is crucial for minimizing accidents, protecting equipment, and maintaining production continuity.
- Protective Enclosures and Barriers
Implementing physical barriers, enclosures, and safety curtains around moving parts and hazardous zones significantly reduces the risk of personnel injury. These protective measures ensure a safe operational environment by limiting direct contact with potentially dangerous machinery. Specific examples include safety cages around conveyor belts in material transfer systems and shielded enclosures around coiling mechanisms. Properly designed barriers prevent accidental contact with moving equipment and reduce the risk of entanglement or crushing.
- Emergency Stop Systems and Interlocks
Robust emergency stop systems and interlocks provide rapid shutdown mechanisms for critical parts of the transcoil system. These critical safety features allow for immediate intervention in case of an emergency, preventing continued operation while enabling swift personnel evacuation from hazardous areas. For instance, an emergency stop button near material transfer points or pressure sensors interlocked with coiling mechanisms allow immediate response to potentially hazardous situations.
- Personnel Training and Protocols
Comprehensive training programs for personnel handling transcoil equipment are essential. Training should cover proper operating procedures, emergency response protocols, and the recognition of potential hazards. Regular refresher courses and updated training materials are crucial for maintaining awareness of evolving safety standards. Training programs enable staff to identify potential dangers, react correctly to emergency situations, and utilize safety equipment effectively.
- Robust Maintenance Schedules and Inspections
Implementing rigorous maintenance schedules and meticulous equipment inspections are vital for preventing malfunctions and equipment failures. Regular maintenance reduces the chance of mechanical breakdowns, which can lead to accidents and create unsafe conditions. Early detection and prompt repairs of potential hazards directly contribute to a safer operational environment. Inspection protocols should cover all parts of the transcoil system, from material transfer mechanisms to coiling equipment, to ensure consistent safety and reduce risks associated with equipment malfunction.
Integrating enhanced safety measures into transcoil systems is not an added expense; it is an investment in long-term operational success. By prioritizing safety, organizations can reduce downtime associated with accidents, minimize the risk of injuries and property damage, and foster a more reliable and productive work environment. The reduction of safety incidents directly translates into significant cost savings in the long run.
Frequently Asked Questions about Transcoil Systems
This section addresses common inquiries regarding transcoil systems, providing clear and concise answers to facilitate understanding of these essential industrial processes. Questions range from fundamental system aspects to more advanced operational considerations.
Question 1: What is a transcoil system, and what are its primary functions?
A transcoil system encompasses a collection of integrated components designed for the efficient transfer and precise coiling of materials. Primary functions include automated material movement, controlled winding, and precise tensioning during the coiling process. These systems optimize manufacturing by minimizing material handling time, reducing waste, and ensuring consistent product quality.
Question 2: What are the key benefits of using a transcoil system?
Benefits include increased production efficiency due to automated processes, reduced material waste resulting from precise coiling, consistent product quality ensured by controlled tensioning, and reduced downtime from improved equipment reliability. Further advantages involve enhanced safety through minimized human interaction with hazardous machinery and greater operational consistency.
Question 3: What factors should be considered when selecting a transcoil system?
Material type, volume of material processed, required coil dimensions, specific tension needs, and the overall production environment must be considered. The chosen system must integrate seamlessly with existing infrastructure and be scalable to accommodate future growth needs. System redundancy and safety features are also key selection factors.
Question 4: How does a transcoil system minimize waste and increase efficiency?
Precise coiling and controlled tensioning reduce material waste during the coiling process. Automated operation reduces human error and minimizes manual handling, further optimizing efficiency. Streamlined material flow and optimized workflows minimize delays and bottlenecks, thereby improving production output and reducing overall operational costs.
Question 5: What are the key safety considerations associated with transcoil systems?
Safety is paramount. Design features should include protective enclosures around moving components, emergency shut-off systems, and clear safety protocols. Employee training on proper operation and emergency procedures is essential to mitigate risks and maintain a safe working environment. Rigorous maintenance schedules and inspection protocols are also vital to identify and address potential hazards proactively.
This FAQ section provides a basic understanding of transcoil systems. Further detail can be found in specific applications and industry guidelines.
The next section will explore specific case studies and applications of transcoil technology.
Conclusion
This exploration of transcoil systems reveals their critical role in modern industrial processes. The analysis underscores the multifaceted benefits derived from these integrated systems, ranging from enhanced production efficiency and reduced material waste to improved product quality and enhanced safety. Key considerations, including precise control, automated coiling, and consistent processes, emerged as integral components driving the system's effectiveness. The inherent advantages of minimized downtime and maximized uptime, achieved through robust design and preventive maintenance, highlight the significant contribution of these systems to operational excellence.
Moving forward, the continued evolution and integration of advanced technologies into transcoil systems are expected. Real-time monitoring, predictive maintenance, and AI-driven optimization hold substantial promise for further improvements in efficiency, precision, and safety. A thorough understanding of these principles and ongoing commitment to innovation in transcoil technology will remain crucial for businesses seeking to enhance their competitive advantage and maintain market leadership in the evolving industrial landscape. Sustained investment in the development and application of transcoil systems promises to be pivotal in shaping the future of manufacturing.
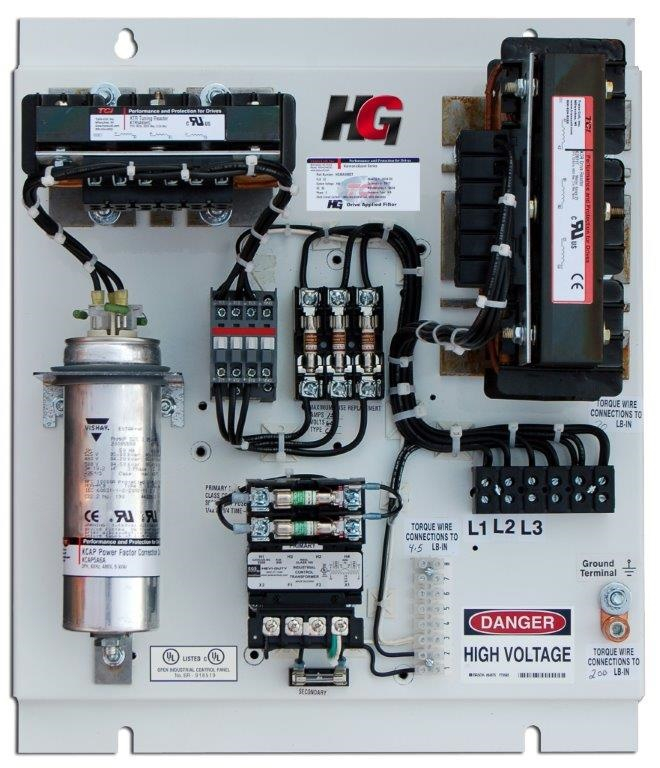
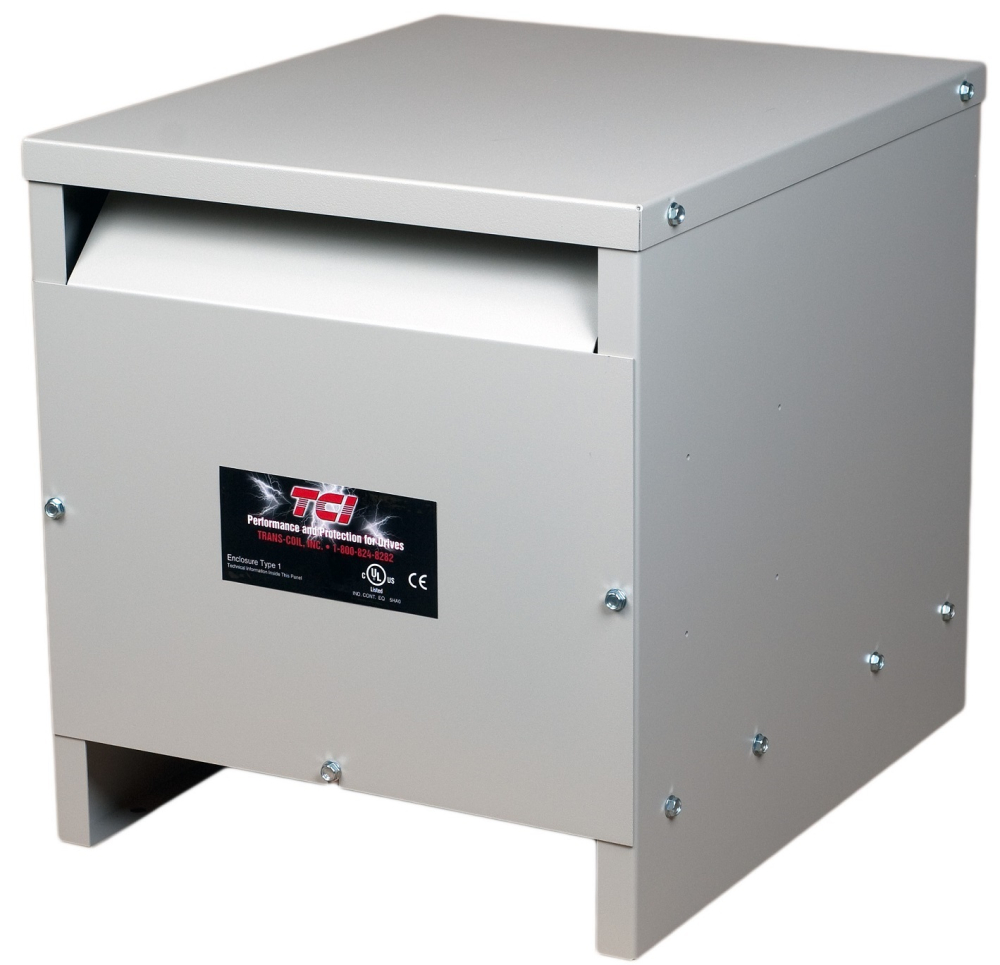
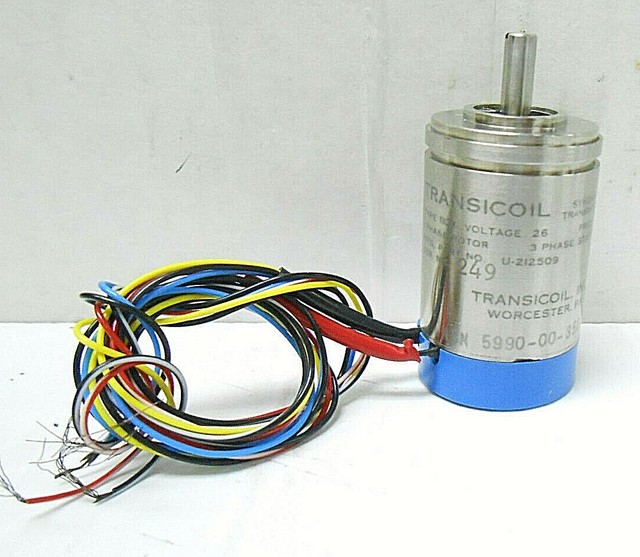
Detail Author:
- Name : Prof. Torrance Schinner I
- Username : jasmin.gorczany
- Email : wcollier@moore.com
- Birthdate : 2005-05-31
- Address : 31901 Barbara Streets Alejandrinville, CT 42241-4376
- Phone : (223) 862-3606
- Company : Gibson, Dietrich and Turner
- Job : Petroleum Pump System Operator
- Bio : Officia eum facilis soluta voluptatibus ea. Tempore sint error dignissimos reprehenderit. Rerum vitae impedit sit rem rem voluptate.
Socials
tiktok:
- url : https://tiktok.com/@renner1993
- username : renner1993
- bio : In at et exercitationem voluptatem omnis eos quis dolore.
- followers : 3892
- following : 164
facebook:
- url : https://facebook.com/krenner
- username : krenner
- bio : Esse ipsum aut quis recusandae nulla quia.
- followers : 6278
- following : 1821